解析:3D打印用球形金屬粉末制備工藝
時間:2019-02-01 13:01 來源:南極熊 作者:中國3D打印網(wǎng) 閱讀:次
球形金屬粉末是金屬3D打印的核心材料, 是3D打印產(chǎn)業(yè)鏈中最重要的環(huán)節(jié), 與3D打印技術(shù)的發(fā)展息息相關(guān)。本文對3D打印用金屬粉末的主要制備工藝的基本原理進(jìn)行了闡述, 并分析了其優(yōu)缺點, 目的是進(jìn)一步提高3D打印用金屬粉末的制備技術(shù)水平, 促進(jìn)3D打印技術(shù)的發(fā)展和應(yīng)用。
球形金屬粉末是金屬3D打印的核心材料, 是3D打印產(chǎn)業(yè)鏈中最重要的環(huán)節(jié), 與3D打印技術(shù)的發(fā)展息息相關(guān)。在“2013世界3D打印技術(shù)產(chǎn)業(yè)大會”中, 權(quán)威專家對3D打印金屬粉末的性能要求給出了清晰的定義, 即尺寸小于1 mm的金屬粉末, 此外, 還要求金屬滿足純度高、球形度好、粒徑分布窄、含氧量低、流動性好等要求。2014年6月頒布的ASTM F3049-14標(biāo)準(zhǔn)規(guī)定了3D打印金屬粉性能的范圍和表征方法。目前, 3D打印用金屬粉末材料主要集中在鐵、鈦、鈷、銅、鎳等金屬及其合金方面。
隨著金屬3D打印技術(shù)的飛速發(fā)展, 球形金屬粉末的市場將保持高增長態(tài)勢。2016年3D打印金屬粉的市場規(guī)模約為2.5億美元, 據(jù)IDTechEx表示, 到2025年, 3D打印金屬粉末的市場規(guī)模將達(dá)到50億美元。但目前3D打印用球形金屬粉主要由國外廠家壟斷, 國內(nèi)生產(chǎn)的球形粉末存在性能不穩(wěn)定、成本高、收得率低等問題。因此, 研究3D打印金屬粉末的制備尤為重要, 本文對3D打印用金屬粉末的主要制備工藝的基本原理進(jìn)行了闡述, 并分析了其優(yōu)缺點, 目的是進(jìn)一步提高3D打印用金屬粉末的制備技術(shù)水平, 促進(jìn)3D打印技術(shù)的發(fā)展和應(yīng)用。
1 3D打印用金屬粉末制備工藝現(xiàn)狀
目前針對3D打印用金屬粉末的制備方法主要有霧化法、旋轉(zhuǎn)電極法、球化法等。
1.1 霧化法
霧化法制取的粉末已占當(dāng)今世界金屬3D打印粉末的80%以上, 其原理是以快速運(yùn)動的流體 (霧化介質(zhì)) 沖擊或以其他方式將金屬或合金液流破碎為細(xì)小液滴, 隨之冷凝為固體粉末的粉末制取方法, 其原理結(jié)構(gòu)圖如圖1所示, 根據(jù)霧化介質(zhì)不同, 霧化法主要分為水霧化和氣霧化。
水霧化是以水為霧化介質(zhì)制備金屬粉末, 其生產(chǎn)成本低, 霧化效率高, 常用來生產(chǎn)鋼鐵粉末、含油軸承用預(yù)合金粉末、鎳基磁性材料粉末等。相對氣霧化, 水的比熱容比較大, 在霧化過程中破碎的金屬熔滴快速凝固變成不規(guī)則狀, 導(dǎo)致粉體形狀難以控制, 且難以滿足金屬3D打印對粉末球形度的要求, 此外由于活性金屬及其合金在高溫下與霧化介質(zhì)水接觸后會發(fā)生反應(yīng), 增加粉末氧含量, 這些問題限制了水霧化法制備球形度高、氧含量低的金屬粉末。
1.1.2 氣霧化
氣霧化的原理是通過高速氣流將液態(tài)金屬流粉碎為小滴并快速冷凝成粉末的過程。氣霧化制備金屬粉末具有粒度細(xì)、球形度高、純度高等優(yōu)點, 是目前生產(chǎn)3D打印用金屬粉末的主要方法, 其制備的3D打印粉末金屬占霧化法制備粉末的40%左右。但氣霧化技術(shù)也存在一定的不足, 在氣流破碎金屬液體的過程中, 氣流能量低, 霧化效率低, 增加了金屬粉末制備成本。
德國Nanoval公司在氣霧化技術(shù)的基礎(chǔ)上, 對噴嘴結(jié)構(gòu)進(jìn)行改進(jìn), 提出層流霧化技術(shù)。層流霧化噴嘴結(jié)構(gòu)如圖2所示。該技術(shù)使氣流和金屬液流在層流霧化噴嘴中呈層流分布, 氣流在金屬表面產(chǎn)生的剪切力和擠壓力, 將金屬液流剪切成直徑不斷縮小的液滴, 其冷卻速度達(dá)106~107K/s, 制備的粉末粒度分布窄, 在2.0MPa的霧化壓力下, 霧化制備的金屬粉末平均粒度可以達(dá)到10μm。且氣體消耗低, 生產(chǎn)成本低, 適用于大多數(shù)3D打印用金屬粉末的生產(chǎn), 但這種制備技術(shù)在霧化的過程中不穩(wěn)定, 難以有效控制霧化過程, 生產(chǎn)效率低, 限制了其生產(chǎn)量, 難以適用于大規(guī)模3D打印用金屬粉末生產(chǎn)。
HJE公司和PSI公司采用研制出了一種熱氣體霧化制備新技術(shù), 對霧化介質(zhì)進(jìn)行加熱, 可以進(jìn)一步提高細(xì)粉收得率, 降低氣體消耗量, 實際應(yīng)用效果良好, 是一項具有應(yīng)用前景的技術(shù)。在霧化壓力1.72 MPa條件下, 將氣體加熱至200~400℃, 霧化所得粉末的平均粒徑和標(biāo)準(zhǔn)偏差均隨溫度升高而降低, 但由于熱氣體霧化技術(shù)受到氣體加熱系統(tǒng)和噴嘴的限制, 僅有少數(shù)幾家研究機(jī)構(gòu)進(jìn)行研究。
昆明冶金研究院通過對霧化噴嘴的改進(jìn), 在溫度1 800℃, 霧化壓力2.0MPa條件下, 采用氮氣霧化技術(shù)制備316 L不銹鋼金屬粉末, 并與德國EOS公司粉體形貌進(jìn)行對比, 微觀結(jié)構(gòu)情況見圖3。
球形金屬粉末是金屬3D打印的核心材料, 是3D打印產(chǎn)業(yè)鏈中最重要的環(huán)節(jié), 與3D打印技術(shù)的發(fā)展息息相關(guān)。在“2013世界3D打印技術(shù)產(chǎn)業(yè)大會”中, 權(quán)威專家對3D打印金屬粉末的性能要求給出了清晰的定義, 即尺寸小于1 mm的金屬粉末, 此外, 還要求金屬滿足純度高、球形度好、粒徑分布窄、含氧量低、流動性好等要求。2014年6月頒布的ASTM F3049-14標(biāo)準(zhǔn)規(guī)定了3D打印金屬粉性能的范圍和表征方法。目前, 3D打印用金屬粉末材料主要集中在鐵、鈦、鈷、銅、鎳等金屬及其合金方面。
隨著金屬3D打印技術(shù)的飛速發(fā)展, 球形金屬粉末的市場將保持高增長態(tài)勢。2016年3D打印金屬粉的市場規(guī)模約為2.5億美元, 據(jù)IDTechEx表示, 到2025年, 3D打印金屬粉末的市場規(guī)模將達(dá)到50億美元。但目前3D打印用球形金屬粉主要由國外廠家壟斷, 國內(nèi)生產(chǎn)的球形粉末存在性能不穩(wěn)定、成本高、收得率低等問題。因此, 研究3D打印金屬粉末的制備尤為重要, 本文對3D打印用金屬粉末的主要制備工藝的基本原理進(jìn)行了闡述, 并分析了其優(yōu)缺點, 目的是進(jìn)一步提高3D打印用金屬粉末的制備技術(shù)水平, 促進(jìn)3D打印技術(shù)的發(fā)展和應(yīng)用。
1 3D打印用金屬粉末制備工藝現(xiàn)狀
目前針對3D打印用金屬粉末的制備方法主要有霧化法、旋轉(zhuǎn)電極法、球化法等。
1.1 霧化法
霧化法制取的粉末已占當(dāng)今世界金屬3D打印粉末的80%以上, 其原理是以快速運(yùn)動的流體 (霧化介質(zhì)) 沖擊或以其他方式將金屬或合金液流破碎為細(xì)小液滴, 隨之冷凝為固體粉末的粉末制取方法, 其原理結(jié)構(gòu)圖如圖1所示, 根據(jù)霧化介質(zhì)不同, 霧化法主要分為水霧化和氣霧化。
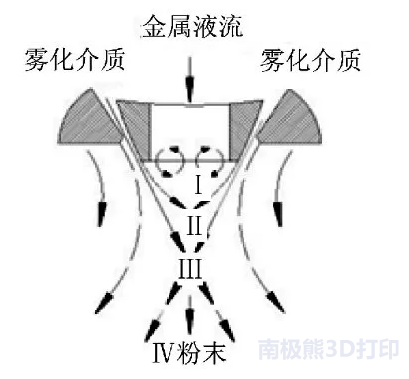
圖1 霧化制粉原理圖
1.1.1 水霧化水霧化是以水為霧化介質(zhì)制備金屬粉末, 其生產(chǎn)成本低, 霧化效率高, 常用來生產(chǎn)鋼鐵粉末、含油軸承用預(yù)合金粉末、鎳基磁性材料粉末等。相對氣霧化, 水的比熱容比較大, 在霧化過程中破碎的金屬熔滴快速凝固變成不規(guī)則狀, 導(dǎo)致粉體形狀難以控制, 且難以滿足金屬3D打印對粉末球形度的要求, 此外由于活性金屬及其合金在高溫下與霧化介質(zhì)水接觸后會發(fā)生反應(yīng), 增加粉末氧含量, 這些問題限制了水霧化法制備球形度高、氧含量低的金屬粉末。
1.1.2 氣霧化
氣霧化的原理是通過高速氣流將液態(tài)金屬流粉碎為小滴并快速冷凝成粉末的過程。氣霧化制備金屬粉末具有粒度細(xì)、球形度高、純度高等優(yōu)點, 是目前生產(chǎn)3D打印用金屬粉末的主要方法, 其制備的3D打印粉末金屬占霧化法制備粉末的40%左右。但氣霧化技術(shù)也存在一定的不足, 在氣流破碎金屬液體的過程中, 氣流能量低, 霧化效率低, 增加了金屬粉末制備成本。
德國Nanoval公司在氣霧化技術(shù)的基礎(chǔ)上, 對噴嘴結(jié)構(gòu)進(jìn)行改進(jìn), 提出層流霧化技術(shù)。層流霧化噴嘴結(jié)構(gòu)如圖2所示。該技術(shù)使氣流和金屬液流在層流霧化噴嘴中呈層流分布, 氣流在金屬表面產(chǎn)生的剪切力和擠壓力, 將金屬液流剪切成直徑不斷縮小的液滴, 其冷卻速度達(dá)106~107K/s, 制備的粉末粒度分布窄, 在2.0MPa的霧化壓力下, 霧化制備的金屬粉末平均粒度可以達(dá)到10μm。且氣體消耗低, 生產(chǎn)成本低, 適用于大多數(shù)3D打印用金屬粉末的生產(chǎn), 但這種制備技術(shù)在霧化的過程中不穩(wěn)定, 難以有效控制霧化過程, 生產(chǎn)效率低, 限制了其生產(chǎn)量, 難以適用于大規(guī)模3D打印用金屬粉末生產(chǎn)。
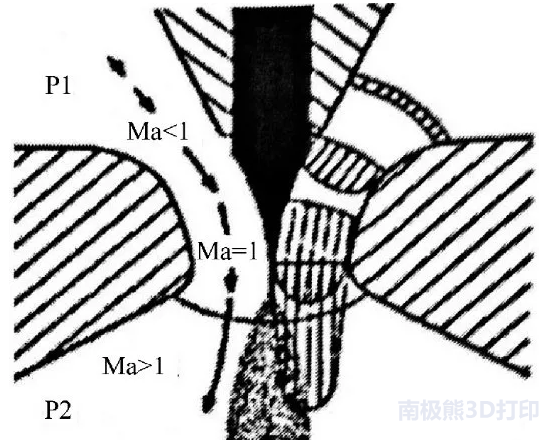
圖2 層流霧化噴嘴結(jié)構(gòu)圖
英國PSI公司在緊密耦合霧化技術(shù)的基礎(chǔ)上對緊耦合環(huán)縫式噴嘴結(jié)構(gòu)進(jìn)行了結(jié)構(gòu)優(yōu)化和改進(jìn), 使氣流的出口速度超過聲速, 可在較小的霧化壓力下獲得高速氣流, 在2.5 MPa壓力下, 氣體速率可達(dá)到540 m/s, 此外超聲緊密耦合霧化技術(shù)可以提高粉末的冷卻速度, 效率高, 成本低, 且應(yīng)用范圍廣, 是氣霧化技術(shù)重要的發(fā)展方向之一, 且具有工業(yè)實用意義, 對于促進(jìn)3D打印用金屬粉末的工業(yè)化生產(chǎn)制備有著重要的意義。HJE公司和PSI公司采用研制出了一種熱氣體霧化制備新技術(shù), 對霧化介質(zhì)進(jìn)行加熱, 可以進(jìn)一步提高細(xì)粉收得率, 降低氣體消耗量, 實際應(yīng)用效果良好, 是一項具有應(yīng)用前景的技術(shù)。在霧化壓力1.72 MPa條件下, 將氣體加熱至200~400℃, 霧化所得粉末的平均粒徑和標(biāo)準(zhǔn)偏差均隨溫度升高而降低, 但由于熱氣體霧化技術(shù)受到氣體加熱系統(tǒng)和噴嘴的限制, 僅有少數(shù)幾家研究機(jī)構(gòu)進(jìn)行研究。
昆明冶金研究院通過對霧化噴嘴的改進(jìn), 在溫度1 800℃, 霧化壓力2.0MPa條件下, 采用氮氣霧化技術(shù)制備316 L不銹鋼金屬粉末, 并與德國EOS公司粉體形貌進(jìn)行對比, 微觀結(jié)構(gòu)情況見圖3。
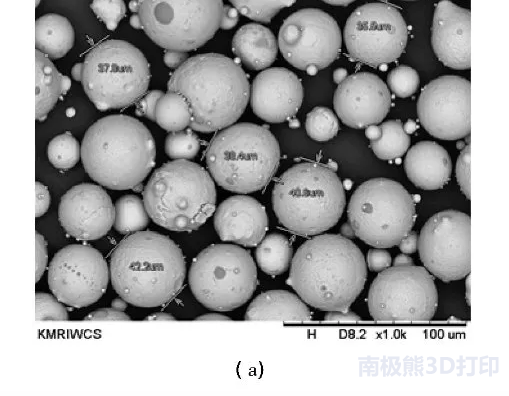
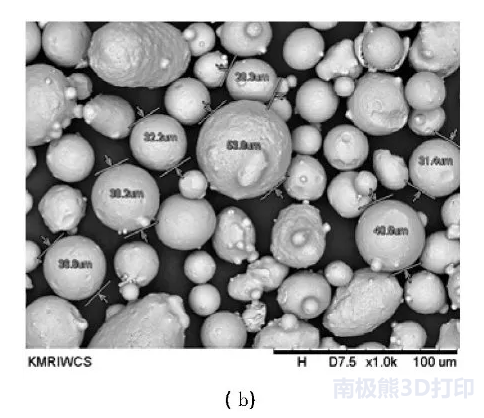
圖3 316 L不銹鋼微觀組織
(責(zé)任編輯:admin)
最新內(nèi)容
熱點內(nèi)容