螺桿擠出熔融沉積建模增材制造致密氧化鋯陶瓷
時間:2021-10-09 14:31 來源:未知 作者:admin 閱讀:次
隨著近年來的快速發展,塑料和金屬增材制造技術已有一定的工業應用,然而工程陶瓷的增材制造技術仍然難以在材料可靠性、尺寸精度和制造成本之間取得平衡。傳統的聚合物基FDM設備通常使用固定直徑的柔性長絲,但聚合物粘結劑與陶瓷粉的混合料在低固相含量(30%
wt
%)時表現出脆性,不易制備柔性陶瓷長絲。然而對于高性能原料來說,固相含量有時需要超過80wt%甚至更高。在陶瓷注射成型中,這種高固相含量的原料通常被粉碎成顆粒狀,通過螺桿擠出的方式進行輸送,并通過加熱和擠壓,最終在噴嘴處獲得致密均勻的絲。對于陶瓷注射成型而言,有機粘結劑的選擇、原料的制備、脫脂和燒結的方法和設備已經進行了幾十年的深入研究和成功開發。這些知識可以用于優化螺桿基礎打印設備的工藝參數,該設備配有螺桿擠壓裝置,適用于使用Al2O3、ZrO2、Si3N4或SiC粉末從微米到納米級的增材制造工程陶瓷部件。
在這項工作中,作者提出一種基于螺桿擠出的適用于高固體負荷原料的FDM方法。確定了氧化鋯陶瓷增材制造螺桿的優化結構參數和加工窗口。并對燒結陶瓷的層間結合和機械強度進行了評價。研究結果表明,基于螺桿擠壓的FDM方法用于制備復雜形狀陶瓷零件是可行的。
圖3為測試不同層厚時坯體和燒結體的密度和彎曲強度。層厚度對印刷體和燒結體的密度沒有顯著影響(見圖3(a))。坯的密度為0.35 g/cm3,達到3Y-TZP理論密度的58%,燒結坯的密度約為6.0 g/cm3,達到TD的99%。如圖3(b)所示,不同層厚制備的坯體抗彎強度達到注塑坯體30mpa抗彎強度的一半以上,證明坯體內部的層間粘結足夠。厚度為0.15 mm的燒結體強度超過厚度為0.1 mm和0.2 mm的燒結體強度,達到890MPa,接近干壓或注塑所能達到的水平。進一步優化印刷參數,以最大限度地減少加工缺陷,并提高制備材料的可靠性將在后續研究中進行。
基于螺桿擠出的FDM系統適用于打印高固相含量的ZrO2顆粒料,對其他工程陶瓷如Si3N4和Al2O3的增材制造也具有廣闊的應用前景。設計螺桿直徑為12mm,長寬比為17:1,緊湊比為2.34。其強度足以承受擠壓過程中產生的剪切應力。通過對打印溫度、螺桿速度和噴嘴尺寸的監測,優化了獲得穩定、精確可控的擠出流量和充分的層間結合的均勻組織的加工窗口。氧化鋯坯體和燒結氧化鋯坯體的密度分別達到理論密度的58%和99%,接近干壓或注射成型所能達到的水平。驗證了基于螺桿擠出的FDM系統適用于復雜幾何形狀陶瓷零件的打印,尺寸精度可控。
在這項工作中,作者提出一種基于螺桿擠出的適用于高固體負荷原料的FDM方法。確定了氧化鋯陶瓷增材制造螺桿的優化結構參數和加工窗口。并對燒結陶瓷的層間結合和機械強度進行了評價。研究結果表明,基于螺桿擠壓的FDM方法用于制備復雜形狀陶瓷零件是可行的。
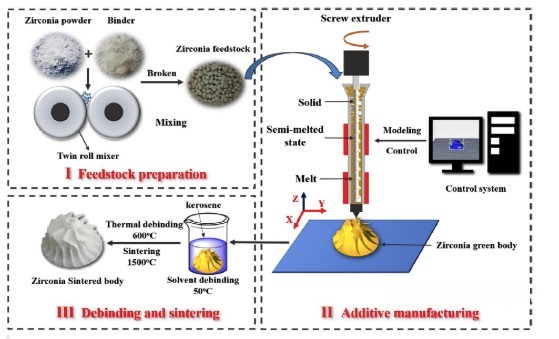
圖1 螺桿擠出熔融沉積致密氧化鋯陶瓷流程
該研究制備氧化鋯陶瓷部件的加工流程如圖1所示。首先,將氧化鋯陶瓷粉與有機粘結劑混合得到原料。然后,將原料板通過螺桿送入料管,再加熱,從噴嘴擠出。陶瓷坯體逐層制造,然后在有機溶劑中進行脫脂。最后,通過熱脫脂和燒結得到致密的陶瓷零件。
擠出流量主要受螺桿轉速和機筒溫度的影響,是評價螺桿擠出裝置性能的重要指標。當螺桿轉速為5 r/min、10 r/min、15 r時,在130 ~
190 C范圍內均可獲得連續穩定的擠出效果。在較高的螺桿轉速(20r /min和25r /min)下,原料不能在130℃和25r
/min下連續擠出。
當筒體溫度超過150℃時,擠出膨脹效果不明顯,當筒體溫度達到160℃后時,擠出的線材直徑幾乎與噴嘴尺寸相等,有利于較高的印刷精度。這可能是由于溫度較高后材料粘度變低,流動性變好導致的。因此,筒體溫度是決定擠出線直徑穩定性的關鍵因素,對打印精確性非常重要。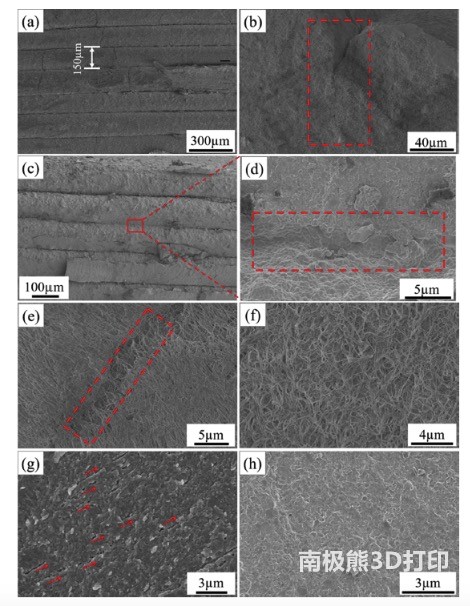
圖2 打印件SEM圖像
本研究主要關注的兩個方面是表面質量和層間結合。表面質量直接關系到燒結材料的精度和后續的加工成本,而層間結合則影響燒結材料的可靠性。在層厚為0.15
mm的表面拍攝的SEM圖像如圖2(a)所示。表面各層之間的間隙是可見的,FDM技術很難避免。然而,從截面圖像估計,這種層間縫隙的深度僅為0.1
mm左右(圖2(b))。在收縮率為20%左右的燒結后,層厚度變為0.1
mm(圖2(c)),在圖2(d)放大圖像中可以清楚地看到,層間區域的顯微組織與內層一樣致密均勻。圖2(b)和圖2(d)中的紅線標記了印刷和燒結部分的層間區域。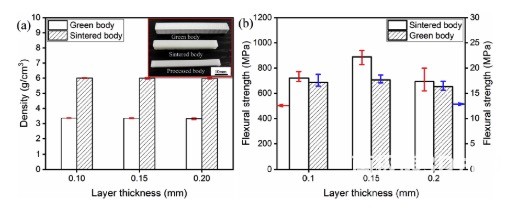
圖3氧化鋯陶瓷打印密度及強度
圖3為測試不同層厚時坯體和燒結體的密度和彎曲強度。層厚度對印刷體和燒結體的密度沒有顯著影響(見圖3(a))。坯的密度為0.35 g/cm3,達到3Y-TZP理論密度的58%,燒結坯的密度約為6.0 g/cm3,達到TD的99%。如圖3(b)所示,不同層厚制備的坯體抗彎強度達到注塑坯體30mpa抗彎強度的一半以上,證明坯體內部的層間粘結足夠。厚度為0.15 mm的燒結體強度超過厚度為0.1 mm和0.2 mm的燒結體強度,達到890MPa,接近干壓或注塑所能達到的水平。進一步優化印刷參數,以最大限度地減少加工缺陷,并提高制備材料的可靠性將在后續研究中進行。
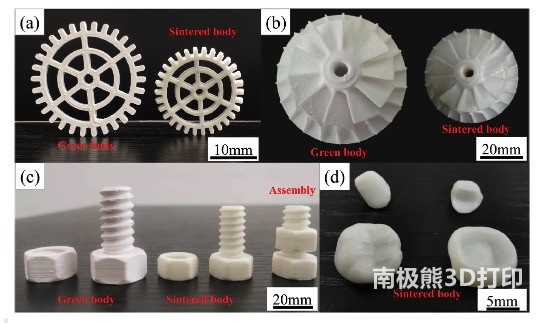
圖4 螺桿擠出熔融沉積致密氧化鋯陶瓷零件
圖4為本研究開發的FDM法制備的一些氧化鋯陶瓷零件。矩形棒料從印坯到燒結件的縱向線形收縮率為20.5%。通過對比坯體的幾何形狀,證實了該方法具有可靠的保形能力(見圖b))。基于螺桿擠出的FDM系統適用于打印高固相含量的ZrO2顆粒料,對其他工程陶瓷如Si3N4和Al2O3的增材制造也具有廣闊的應用前景。設計螺桿直徑為12mm,長寬比為17:1,緊湊比為2.34。其強度足以承受擠壓過程中產生的剪切應力。通過對打印溫度、螺桿速度和噴嘴尺寸的監測,優化了獲得穩定、精確可控的擠出流量和充分的層間結合的均勻組織的加工窗口。氧化鋯坯體和燒結氧化鋯坯體的密度分別達到理論密度的58%和99%,接近干壓或注射成型所能達到的水平。驗證了基于螺桿擠出的FDM系統適用于復雜幾何形狀陶瓷零件的打印,尺寸精度可控。
(責任編輯:admin)
最新內容
熱點內容