17-4PH高強鋼增材制造組織與性能研究
17-4PH高強鋼為超低碳鋼,依靠析出第二相使材料產生強化作用,作為一種具有高強度和強耐腐蝕性的不銹鋼材料,在醫療器械、化工、汽車制造、軍工、航空航天及核工業等方面有著廣泛的應用,由于材料只能長期服役在低于300℃下,對于其性能要求更高,以及其沉淀硬化而產生的高硬度使得該材料變得很難加工,傳統的高溫加工工藝已經不能滿足零件的加工,如鑄造工藝缺陷問題,給后續變形加工和熱處理造成的難度較大,以及焊接的復雜零件易產生應力集中,因此用選區激光熔化(SLM)成形技術步解決了成形問題。
SLM成形技術利用金屬粉末在激光束的熱作用下快速熔化冷卻,克服了傳統技術制造具有復雜形狀金屬零件的難題,但SLM成形熱循環過程導致殘余應力、形成裂紋、成形過程中發生飛濺,以及氣孔的形成對力學性能或成形零件的表面粗糙度產生不利影響,以及在制造過程中存在各向異性、孔隙、殘余應力和分層等問題。近年來,通過對SLM成形參數(激光功率、掃描速度、掃描間距、層厚、構建方向、保護氣氛等)的研究,提高SLM成形零件的整體性能成為研究者的重要目標。
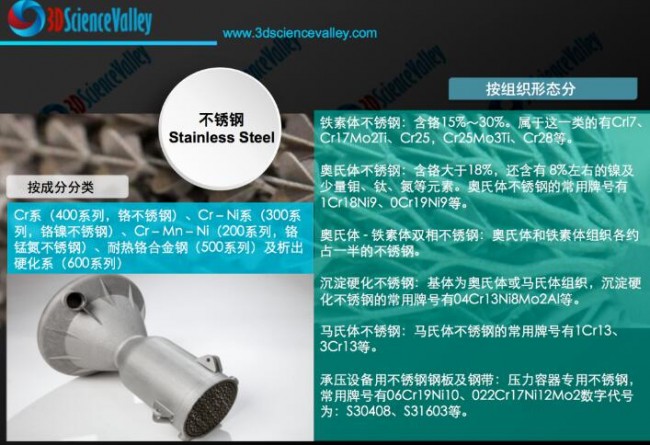
研究團隊采用選區激光熔化(SLM)增材制造技術制備了17-4PH高強鋼,研究了激光功率和掃描間距對試樣組織和性能的影響,確定了最佳工藝參數,對試樣組織進行表征同時對拉伸性能和斷裂機制進行研究。
結果表明,在激光功率為165W時,激光能量密度低粉末吸收能量較少,導致粉末存在未熔化區域;隨著激光功率增加到205W時,粉末吸收能量增多,導致出現球化現象,試樣氣孔增多;掃描間距對孔隙缺陷影響比掃描功率小。激光功率為185 W和掃描間距為110 μm工藝參數下,氣孔分布少,硬度(HV)達到370。
17-4PH高強鋼SLM成形微觀組織主要由馬氏體和奧氏體組成,沉淀硬化相為ε-Cu,提高了材料的硬度;斷口韌窩形狀大小相似且尺寸較小,表明試樣有較高的強度和良好的韌性。
使用的17-4PH高強鋼粉體的主要化學成分(質量分數)為:Cr 為14.10%,Ni 為3.94%,Cu 為5.64%,Si為 0.47%,Mn為 0.37%,Nb為 0.21%,C為 0.07%,Fe余量。對17-4PH不銹鋼粉末進行篩選,過濾出粉末中的雜質,將過濾后的粉末放入烘干箱進行干燥處理,經過干燥后的金屬粉末中無水分。
使用選區激光熔化成形設備,其搭載200 W/500 W水冷光纖激光器,激光波長為106~1090 nm,成形室內用氬氣保護。對影響成形的工藝參數進行優化設計,影響選區激光熔化成形試樣的因素有激光功率、掃描間距、掃描速度、曝光時間、層厚等。試驗中固定掃描速率620mm·s -1和層厚30 μm,選擇不同激光功率P、掃描間距d進行研究,具體見表1。
l 17-4PH高強鋼SLM成形工藝參數優化
圖2為激光掃描速率為620 mm·s -1,掃描間距為110 μm,掃描層厚為30/μm,在不同功率下氣孔分布。隨著激光功率逐漸增大,能量密度也會逐漸變大,充足的激光束能量會使金屬粉末充分熔化,金屬層內的液相流動性提高,這有利于金屬顆粒之間接觸面的凝固成形,會使材料孔洞減少、致密度明顯的提高。然而,當激光功率繼續增大,激光束能量吸收過多導致粉末過熔,形成缺陷。
圖2 為激光掃描速率為620 mm·s -1,掃描間距為110 μm,掃描層厚為30/μm,在不同功率下氣孔分布
(a)165W(b)185W(c)205W(d)激光功率185W氣孔SEM形貌
圖3為激光功率為185W,激光掃描速率為620mm·s -1,掃描層厚為30 μm,在不同描間距下的試樣氣孔分布。可以看出,整體氣孔分布變少,說明掃描間距對孔隙缺陷影響較小。
圖3 激光功率為185W,激光掃描速率為620mm·s -1,掃描層厚為30 μm,在不同描間距下的試樣氣孔分布
(a)90 μm(b)110 μm(c)130 μm(d)掃描間距110 μm氣孔SEM形貌
圖4 為不同激光功率下試樣硬度分布。圖5為不同掃描間距下試樣硬度分布。從圖4和圖5可以看出,在功率165W時,激光能量密度最低,氣孔最多,導致密度降低,從而試樣硬度下降。掃描間距對孔隙缺陷影響較小,但是金屬層被激光掃描時,金屬粉末液相之間需要搭接;掃描間距為90 μm時,能量密度增大,試樣存在過熔狀態,導致硬度降低;掃描間距為130 μm時,掃描面上掃描軌跡間搭接距離變大,能量密度降低,殘余奧氏體含量會增多,導致硬度降低。在功率為185W和掃描間距為110 μm下氣孔數量減少,孔隙率降低,密度增加,基體硬度變大,硬度升高,而且因基體內部沉淀出ε-Cu以及一些碳化物沉淀相,可進一步提高試樣的硬度。
最終確定SLM成形工藝參數為:激光功率為185W,掃描間距為110μm,掃描速度為620mm·s -1,掃描層厚為30μm,激光能量密度為90.42J·mm-3。
(責任編輯:admin)