增材制造高熵合金的組織結構和性能(2)
(2)掃描速度:掃描速度對冷卻速率和凝固模式有直接影響。較高的掃描速度可能促進熔池快速凝固和細晶形成,但掃描速度過快會導致熔池不穩定。較低的掃描速度則可能增加熱累積,形成粗晶或不均勻組織。Kunce等生產高熵合金AlCoCrFeNi的薄壁樣品時發現激光掃描速度對合金的微觀組織形態有顯著影響。隨著掃描速度的增加,冷卻速率提高,晶粒尺寸減小。冷卻速度和樣品的平均尺寸隨掃描速度變化關系如圖3所示。掃描速度從2.5增加到40.0 mm/s時,平均晶粒尺寸從(108.3±32.4) μm減小到(30.6±9.2) μm。此外,掃描速度的變化還影響析出相的形態,在枝晶和枝晶間區域,析出物從細小球形(直徑小于100 nm)轉變為旋節狀(厚度小于100 nm)。這些結果表明,通過調節激光掃描速度,可以控制AlCoCrFeNi高熵合金的微觀組織,從而優化其性能。

(3)層厚和掃描間距:通過調整層厚和掃描間距,可以優化疊層質量,降低孔隙率,從而提高材料的機械性能。
現有研究中不少學者已通過調整高熵合金制備過程中的實驗參數進一步改善其性能:
Liu等在對AlxCoCrFeNi高熵合金的研究中,通過控制高熵合金元素比例和增材制造的預熱參數,發現均勻的固溶體相結構對于提高材料抗裂性能至關重要。在元素比優化的條件下,調控激光掃描路徑和掃描策略可以有效降低內部殘余應力,從而減少裂紋生成。通過優化熔池的動態平衡狀態,實現了晶粒結構的均勻化,證明了激光路徑的精細設計和參數調整對于制備高性能高熵合金的重要性。
Niu等研究了利用激光粉末床熔融技術(LPBF)制備高熵合金,并結合深冷處理以改善材料性能。通過調整激光功率、掃描速度和層厚度等關鍵參數,顯著減少了制備過程中微裂紋的產生,并實現了組織結構的細化。研究發現深冷處理可以誘發晶體中退火孿晶的形成,從而提高材料的強度與韌性平衡。這一實驗結果表明,細晶粒與高密度孿晶的協同作用是實現性能提升的重要機制。
Song等研究了不同激光功率和掃描速度對孔隙率和核平均取向偏差(KAM)的影響。圖4所示為激光粉末床熔融技術不同參數下的孔隙率,可以看出激光功率一定時,隨著掃描速率的增加,孔隙率顯著增加。當掃描速率一定時,激光功率的改變對孔隙率影響不大。激光功率和掃描速度對熔池穩定性與孔隙率的影響具有顯著的非線性特征。在適當范圍內,較高掃描速度有助于提高熔池的形狀穩定性與冷卻均勻性,從而減少孔隙率。KAM值可用于反映晶格失配的程度,靠近晶界的區域一般具有相對較高的KAM值,而晶粒內部區域的KAM值幾乎為零,相鄰晶粒之間的晶格失配可能導致嚴重的局部殘余應變。KAM可用于估計激光粉末床熔融技術樣品的位錯密度,不同激光粉末床熔融工藝參數下的KAM值如圖5所示,適當范圍內的激光功率和掃描速度提升了激光粉末床熔融過程中熔池的穩定性,減少了孔隙率,提高了致密性。通過優化工藝參數使得Co47.5Fe28.5Ni19Si3.4Al1.6高熵合金的拉伸屈服強度提升至417.0 MPa,延伸率可達33.9%。同時形成了獨特的位錯–析出網絡,增強了綜合性能,包括優異的軟磁性和力學性能。以上研究表明,適當的參數調節能顯著改善微觀結構的均勻性,從而提高力學性能和功能特性。因此,優化掃描速度需要考慮其非線性影響,并與激光功率等參數協同調控,以獲得最佳致密性。
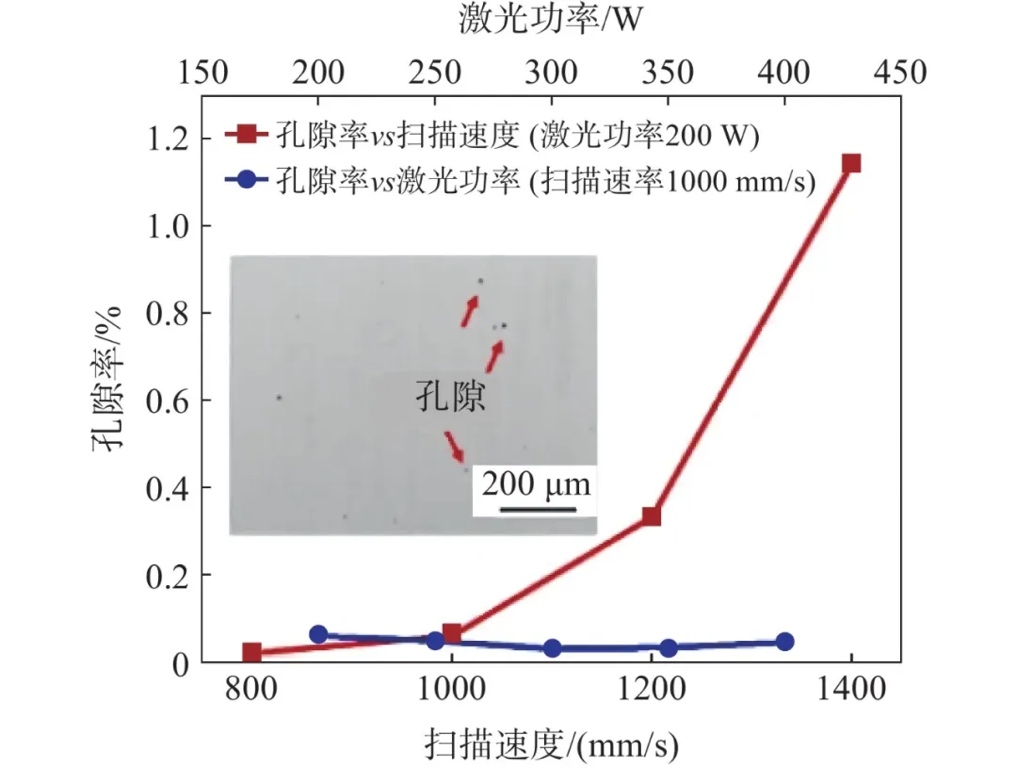
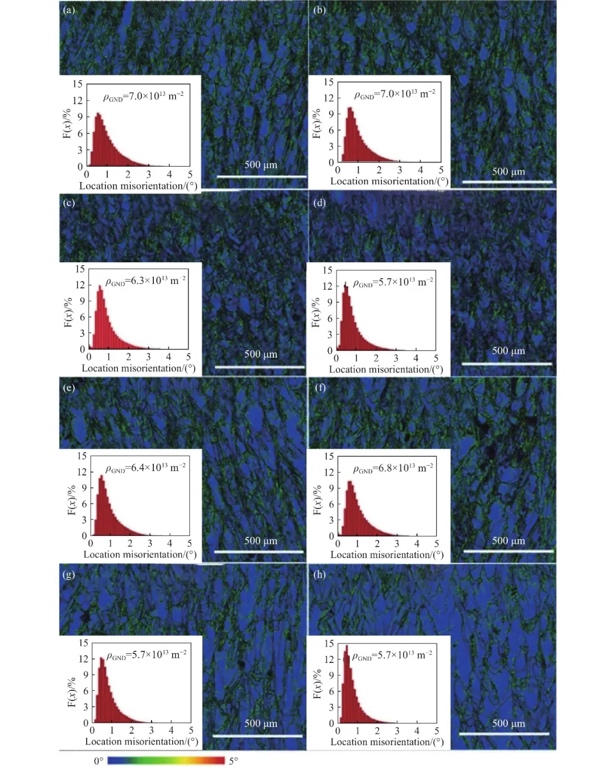
Ma等通過設計納米結構和利用多組元效應,制備的高熵合金實現了超越傳統金屬和異質納米結構金屬的強度–延展性組合,其屈服強度和拉伸應變關系如圖6所示。同時該研究通過調控增材制造過程中熱處理參數,發現異質性結構對高熵合金的強度和塑性具有明顯的協同作用。圖7通過總結和對比不同微觀結構高熵合金的性能,說明了異質性設計的關鍵作用。采用不同的冷卻速率和熱處理工藝,如深低溫處理和多次熱循環,成功制備了納米級析出物和高密度晶界位錯網絡。結果表明這些優化方法能夠顯著提升材料的強度,同時保持良好的塑性。圖8所示為相變誘導塑性(Transformation-induced plasticity,TRIP)效應和孿生誘導塑性(Twinning-induced plasticity,TWIP)效應對不同材料中屈服強度與均勻拉伸應變的影響,其中TRIP HEAs表現出優異的性能,說明通過相變和孿晶效應優化微觀結構的重要性。該研究進一步證明,通過引入異質性可以有效緩解增材制造中常見的裂紋問題,并在材料的性能設計中提供更大的靈活性,熱處理工藝和冷卻速率的精確控制是優化高熵合金力學性能的關鍵。


除了在實驗過程中優化調整制備高熵合金的工藝參數和條件外,對制得的高熵合金進行熱處理或后處理也能改善其性能。
熱等靜壓(HIP)是減少孔隙率的重要手段。研究表明,在1150 °C和150 MPa對增材制造的CrMnFeCoNi合金進行3 h熱等靜壓處理,可以顯著降低殘余應力并改善元素分布均勻性。但熱等靜壓可能導致相轉變和晶粒粗化,對性能產生負面影響。因此熱等靜壓工藝的選擇需要綜合考慮材料的微觀結構與性能需求。
深度低溫處理(DCT)通過快速冷卻和再加熱促進納米孿晶、堆垛層錯和位錯網絡的形成,進一步改善了材料的屈服強度和塑性。Li等研究發現循環深度低溫處理能夠顯著增加缺陷密度,實現相結構從FCC到HCP的轉變,優化了拉伸強度和延展性。Song等通過液氮快速冷卻和水浴加熱的方法進行深度低溫處理,增強了高熵合金的位錯密度和孿晶結構,使拉伸強度和延展性得到顯著提升,FCC到HCP轉變也更加均勻,提高了材料的綜合穩定性。證明深度低溫處理可以通過調控位錯密度與晶體結構轉換,優化高熵合金的力學性能。
激光沖擊強化(LSP)通過高能脈沖激光在材料表面引發沖擊波,產生梯度微觀結構和壓縮殘余應力,從而顯著提升材料的強度和延展性。對激光增材制造的CrMnFeCoNi合金進行激光沖擊強化處理后,其失效模式從混合延性–脆性失效轉變為純延性失效,同時提升背應力硬化效應,增強材料的塑性變形能力。
退火作為一種常見的熱處理工藝,可以通過降低位錯密度和優化析出相結構,改善材料的綜合性能。Zhu等將選擇性激光熔化技術制備的CrMnFeCoNi合金在900 °C退火1 h后,晶粒細化和析出相的增強效應使得高熵合金的強度和延展性顯著提升。此外,控制退火溫度和退火時間可誘導析出相均勻分布,實現力學性能的進一步優化。Song等對打印樣品在750 ℃下進行退火處理,形成了L12和B2型析出物,使得樣品的屈服強度提升至1201 MPa,極限強度達到1512 MPa,同時保持了15.1%的延展性,該實驗證明了退火誘導的析出強化機制及退火工藝生成的納米析出物對材料綜合性能的顯著貢獻。
近年來,上述技術的組合應用也為性能綜合提升提供了新的可能性。退火與激光沖擊強化工藝結合,可以顯著細化粗晶粒并形成變形孿晶,從而同時提高強度和延展性。基于深度低溫處理和循環深度低溫處理的創新方法,為進一步優化增材制造高熵合金的微觀組織與宏觀性能提供了廣闊的研究空間。
3.2 組織與性能關聯分析
實驗研究表明,高熵合金的性能與其微觀組織特征密切相關。晶粒的大小、形狀和取向直接影響材料的強度、延展性和疲勞性能。例如,細小晶粒通過阻礙位錯運動提升了材料強度,納米析出物的存在則進一步增強了強化效果。變形孿晶的生成不僅提升了材料的延展性,還對位錯滑移產生釘扎效應,從而改善硬度。
研究還揭示了析出相在強化機制中的作用。高密度碳化物納米析出物通過增強對位錯運動的抵抗力,大幅提高了材料的屈服強度。此外,某些合金體系在退火過程中形成了L12和L21雙重析出相,這種結構顯著提升了材料的拉伸強度和抗疲勞性能。
宏觀尺度上的異質性結構設計也證明了其在性能優化中的重要性。通過引入梯度殘余應力分布和復雜相結構,可以實現強度與延展性的良好平衡。微觀組織的精準調控,例如通過快速冷卻形成過飽和固溶體,以及通過多次熱處理引入多尺度結構,均可使高熵合金的綜合性能得到進一步優化。
Song等深入研究了高熵合金組織與性能方面存在的關系,得出以下結論:
(1)高熵合金的強度來源于固溶強化、晶界強化和析出強化。例如,快速冷卻導致的亞穩納米析出物(如金屬間化合物、碳化物等)顯著提高了高熵合金的硬度和屈服強度。同時,在LPBF條件下,高冷卻速率形成了細小的柱狀晶與胞狀亞晶,顯著提升材料的屈服強度。納米尺度的析出物(如Cr-rich析出物)在BCC相中形成,與FCC相協同作用,增強了材料的強度和延展性。
(2)高熵合金的塑性與韌性主要取決于其相結構,FCC相的滑移系較多,位錯易于運動,延展性優異;BCC相由于滑移系較少且有較高的剪切模量,塑性較低。通過雙相結構的設計(如FCC+BCC復合相),可有效改善強度–延展性平衡,FCC相的柔韌性與BCC相的硬度形成互補,使得材料在高強度下仍能保持較好的塑性。
(3)增材制造高熵合金中細小的柱狀晶和非平衡亞穩相提高了抗疲勞裂紋擴展能力,但孔隙率和熔池邊界缺陷會削弱疲勞壽命。
(4)FCC相在低溫下保持了較高的韌性,而BCC相在低溫下易發生脆–韌轉變。通過微合金化和熱處理工藝進行優化,可部分改善這一缺陷。對加工好的材料進行退火,能夠顯著改善材料性能。
Ma等通過實驗發現,晶粒大小、分布、析出物的均勻性以及位錯密度是決定高熵合金力學性能的主要因素。細小晶粒可以顯著提高材料的強度,而析出物的數量和分布對塑性起到了調控作用。同時,孿晶結構的引入不僅增強了材料的延展性,還能通過阻礙位錯運動提升硬度。Niu等研究發現高熵合金中非平衡組織(如柱狀晶和胞狀亞結構)可以通過快速冷卻過程得到顯著優化。這些結構提升了高熵合金的硬度和抗拉強度,但也可能因為殘余應力增加而導致裂紋敏感性上升。通過調控熱處理溫度和時間,可以誘導析出強化機制的發生,從而實現性能的進一步提升。研究表明,微觀組織與力學性能之間存在著高度耦合關系,材料的性能可以通過精準控制組織演變實現最優設計。
現有問題與未來展望
盡管目前已有很多有關高熵合金的研究,但高熵合金的發展與應用仍存在較多問題。首先,在增材制造過程中由于高熔點和低熔點元素的蒸發率差異,易出現成分偏析和微觀組織不均的現象。例如,在選擇性激光熔化和直接能量沉積工藝中,不同元素的凝固速度差異會導致元素分布不均勻,影響材料的力學性能和抗疲勞性能。其次,雖然快速冷卻和高溫梯度是增材制造的特點,但也導致了顯著的殘余應力和裂紋敏感性。尤其是在選擇性激光熔化工藝中,高能激光快速熔化和凝固金屬粉末,產生較大的熱應力,使得裂紋的形成和擴展成為制備過程中不可忽視的問題。盡管增材制造能夠通過快速冷卻形成非平衡組織(如細柱狀晶和納米析出物),但對微觀組織的精準控制仍存在挑戰。例如,組織的晶粒細化和取向調整需要對激光功率和掃描速度等參數進行高度優化,而這些參數間的交互作用尚未完全明晰,仍需要進行大量研究與測試。最后,高熵合金的性能優化需要在納米、微觀和宏觀尺度上同時實現,但增材制造技術通常只能在某一尺度上有顯著優勢。例如,快速冷卻有助于微觀組織的細化,但可能對宏觀力學性能(如抗疲勞和延展性)產生負面影響。以上方面還需要研究人員的不斷努力,不斷提升制造工藝。
未來研究人員可以聚焦于開發具有更好成分均勻性和流動性的高熵合金粉末。通過引入表面涂層或合金元素調控蒸發率,減少成分偏析;或者通過預熱基板、優化掃描路徑以及采取后處理(如熱等靜壓和深度低溫處理),減少裂紋敏感性和殘余應力。開發能夠自愈裂紋的高熵合金材料也是一個重要的發展方向。或者研究異質結構、梯度材料和多相復合材料的設計,通過不同區域的成分或組織變化實現強度、韌性和抗疲勞性能的平衡,同時滿足多功能需求。開發基于非傳統熱源的增材制造技術,例如超聲波增材制造(UAM)或電化學增材制造(EAM),也可以彌補當前增材制造技術的局限性。
將新興技術與制造工藝相結合是提升加工效果的重要途徑。例如,通過協同優化激光功率、掃描速度和掃描策略,可以實現對復雜工藝參數的智能化控制。近年來,機器學習(ML)和人工智能技術的引入,為選擇性激光熔化技術加工高熵合金的研究提供了新思路。Tan等采用機器學習技術可以預測通過選擇性激光熔化技術制得的高熵合金的顯微組織和力學性能,機器學習策略流程圖如圖9所示。通過優化材料描述符和機器學習模型,研究者們成功構建了一個模型,該模型在區分選擇性激光熔化技術加工高熵合金的面心立方、體心立方和雙相結構方面,準確率達到了81.58%。此外,還開發了預測拉伸性能的優化模型,對極限拉伸強度(UTS)和屈服強度(YS)預測的平均絕對百分比誤差(MAPE)分別為20.43%和20.25%,具有較高的可靠性。實驗表明,使用選擇性激光熔化技術制造的多種高熵合金,實際性能與預測結果具有良好的一致性。未來研究也可以更加關注增材制造過程中的多物理場模擬,以精準預測熔池行為和微觀組織演變。
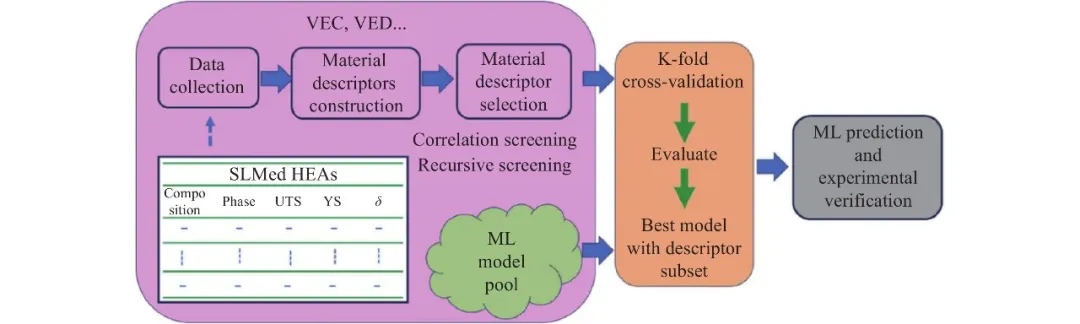
結束語
本文系統總結了增材制造技術在高熵合金領域的研究進展,并重點分析了不同增材制造技術的工藝特點及其在組織調控中的作用。增材制造技術中的高冷卻速率促進了細晶組織和納米析出物的形成,而工藝參數的優化(如激光功率、掃描速度)和后續熱處理(如退火、深冷處理)則是進一步提高高熵合金性能的重要手段。此外,通過深入探討組織結構與性能的關聯,揭示了FCC、BCC、雙相結構等對力學性能等多功能特性的關鍵影響機制。
盡管增材制造技術在高熵合金制備中取得了諸多成果,但仍存在裂紋控制、成分偏析和大尺寸部件制造等問題,需要展開深入研究。未來可能的發展方向包括:(1)開發適應工業應用的高效制備工藝;(2)利用人工智能優化工藝參數,實現精準調控;(3)探索新型高熵合金體系,結合多尺度模擬技術,推動理論與實驗的協同發展。隨著增材制造技術的不斷進步,高熵合金將在更廣泛的領域發揮其潛力,為先進材料科學與制造技術的融合提供新的動力。
參考文獻(略)
(責任編輯:admin)