增材制造發動機燃燒室流道多余物X射線成像檢出能力研究
時間:2024-10-11 08:41 來源:特種鑄造及有色合金2024年第44卷 作者:admin 閱讀:次
燃燒室是高馬赫數超燃沖壓發動機中技術難度最大的部件之一,其內部有復雜的燃料流道,一般采用激光選區熔化(Selective Laser
Melting, SLM)技術制造,材料為 GH3625
高溫合金。由于增材制造工藝復雜,燃燒室成形后容易產生孔隙、裂紋、未熔粉末顆粒、熔合不良等內部缺陷,流道內還可能存在多余物,影響燃燒室使用性能。此外,燃燒室高溫工作時筒壁還可能變形導致壁厚變化。
【研究亮點】
采用CR和CT技術對燃燒室模擬件內部流道的多余物缺陷進行檢測,研究了X射線成像方法在增材制造件內部流道多余物檢測中的能力。結果表明,CR技術可檢測到最小尺寸為0.15mm的凸出立方體多余物,而顯微CT技術可檢測到最小尺寸為0.08mm的凸出立方體多余物。
【全文導讀】
南昌航空大學無損檢測技術教育部重點實驗室聯合中國航發沈陽黎明航空發動機有限責任公司研究團隊在2024年第44卷第9期《特種鑄造及有色合金》期刊上發表了題為“增材制造流道多余物X射線成像檢出能力研究”的文章,作者采用激光選區熔化工藝增材制造了含復雜流道的燃燒室模擬件,流道內部預制了不同尺寸的凸出立方體多余物,并放置一組標準尺寸金屬絲模擬線形多余物。采用計算機射線照相(Computed radiology, CR)和顯微計算機層析成像(Computed tomography, CT)對試樣進行檢測,研究X射線成像方法對增材制件內部流道多余物的檢測能力,并采用顯微CT對流道壁厚進行分析與評估。結果表明,CR可檢出最小設計尺寸為0.15 mm的凸出立方體多余物和最小絲徑為0.1 mm的線形多余物;顯微CT可檢出最小設計尺寸為0.08 mm的凸出立方體多余物和最小絲徑為0.1 mm的線形多余物。顯微CT尺寸測量結果顯示,線形多余物測量尺寸與標準尺寸一致,凸出立方體多余物測量尺寸普遍大于設計尺寸,最大絕對誤差不超過50 μm。通過顯微CT壁厚分析發現,寬段流道均勻性良好。
1 試驗材料與方法
1.1 試驗材料
以GH3625粉末為原材料,采用自主設計的S310型激光選區熔化增材制造系統制備內部流道試樣,模擬超燃沖壓發動機燃燒室流道結構。表1為GH3625合金的化學成分,圖1為增材制造內部流道試樣CAD設計剖面圖與實物圖。試樣尺寸:外徑為80mm,壁厚為5mm,高為100mm;內部分為寬窄兩段不同尺寸的流道,窄段流道為2mm×1.5mm×50mm,寬段流道為3 mm×2mm×50mm;窄段每條流道內部預制10個凸出立方體多余物,尺寸分別為0.2、0.2、0.15、0.15、0.1、0.1、0.1、0.08、0.08和0.08mm,編號依次為1~10;寬段流道內部放置7根鎳標準絲型像質計(HB7684-2000)模擬線形多余物,絲徑分別為0.4、0.32、0.25、 0.20、0.16、0.125 和 0.1 mm,絲號分別對應10~16。
1.2 透照分析與試驗
圖2為流道增材制件CT透照布置示意圖。當焦距為765mm檢測時,X射線對窄段流道最小和最大透照厚度分別為7mm和35mm,寬段流道最小和最大透照厚度分別為6mm和31mm,兩種情況下最大透照厚度均約為最小透照厚度的5倍。針對上述情況,采用小焦點射線機進行CR檢測,可有效檢測出其內部缺陷;采用顯微CT檢測流道多余物并進行尺寸測量。
1.2.1 X射線CR試驗
采用ISOVOLT320Titan E射線機 ,焦點尺寸為0.4mm×0.4mm,CR掃描儀采用CRx25P,激光焦點為12.5μm,配套超高分辨率IPU成像板。采用源在外單壁透照,試驗焦距為900mm,管電壓為130kV,管電流為6mA,曝光時間為120s,鎳絲像質計放置在寬流道源測表面。
1.2.2 顯微CT試驗
采用YXLON FF85顯微CT成像系統,其中微焦點射線源為Microfocus tube 225kV,最大管電壓為225kV,焦點尺寸最小為6μm;平板探測器為VAREX 4343HE型非晶硅平板探測器,其閃爍體材料為碘化銫,探測器單元尺寸為139μm×139μm,成像矩陣為3072×3072,A/D位數為16 bit。CT掃描試驗參數:源到試樣旋轉中心距離為165mm,源到探測器距離為765mm,管電壓為220kV,管電流為360μA,單張投影圖像積分時間為2.31s,在360°范圍內共獲得3059張投影圖像,成像分辨率為30μm。
2 試驗結果與分析
2.1 CR結果與分析
對GH3625高溫合金SLM增材制造流道試樣進行CR試驗,結果見圖3,其中圖3a箭頭處為識別出的預制凸出立方體多余物缺陷,每個流道均能檢出4個立方體多余物,箭頭1~4是尺寸分別為0.2、0.2、0.15和0.15mm的凸出立方體多余物。從檢測靈敏度方面,圖3b中可識別像質計16號絲,滿足GB/T 26642-2022的A級要求。從線形多余物檢出能力方面,可檢出的最小線形多余物為第16號絲,絲徑為0.1mm。可以看出,CR試驗能夠檢出最小設計尺寸為0.15mm的凸出立方體多余物和最小絲徑為0.1 mm的線形多余物,但受檢測靈敏度的影響,設計尺寸≤0.1 mm的凸出立方體多余物容易漏檢。
2.2 CT結果與分析
根據顯微CT重建圖像,可在不同切片圖像上觀察缺陷及流道內部結構,有利于多余物缺陷的定位和定量,同時可對流道壁厚進行分析。
2.2.1 多余物檢測
圖4為窄段流道多余物切片圖像分析結果,圖4b中箭頭處為凸出立方體多余物。可以看出,設計尺寸為0.08~0.20mm,所有預制立方體多余物均被檢出。
為了進一步分析顯微CT對立方體多余物缺陷檢出能力,選取圖4a中4個流道進行多余物尺寸分析,對其凸出方向的最大距離進行測量。表2為4個流道內部1~10號凸出立方體多余物設計尺寸、4個流道處測量尺寸、平均測量尺寸及絕對誤差。可以看出,凸出立方體多余物實測尺寸普遍大于設計尺寸,1~10號立方體多余物的絕對誤差在20~50μm范圍內,CT 最小可測量的立方體多余物尺寸為0.1mm。
【研究亮點】
采用CR和CT技術對燃燒室模擬件內部流道的多余物缺陷進行檢測,研究了X射線成像方法在增材制造件內部流道多余物檢測中的能力。結果表明,CR技術可檢測到最小尺寸為0.15mm的凸出立方體多余物,而顯微CT技術可檢測到最小尺寸為0.08mm的凸出立方體多余物。
【全文導讀】
南昌航空大學無損檢測技術教育部重點實驗室聯合中國航發沈陽黎明航空發動機有限責任公司研究團隊在2024年第44卷第9期《特種鑄造及有色合金》期刊上發表了題為“增材制造流道多余物X射線成像檢出能力研究”的文章,作者采用激光選區熔化工藝增材制造了含復雜流道的燃燒室模擬件,流道內部預制了不同尺寸的凸出立方體多余物,并放置一組標準尺寸金屬絲模擬線形多余物。采用計算機射線照相(Computed radiology, CR)和顯微計算機層析成像(Computed tomography, CT)對試樣進行檢測,研究X射線成像方法對增材制件內部流道多余物的檢測能力,并采用顯微CT對流道壁厚進行分析與評估。結果表明,CR可檢出最小設計尺寸為0.15 mm的凸出立方體多余物和最小絲徑為0.1 mm的線形多余物;顯微CT可檢出最小設計尺寸為0.08 mm的凸出立方體多余物和最小絲徑為0.1 mm的線形多余物。顯微CT尺寸測量結果顯示,線形多余物測量尺寸與標準尺寸一致,凸出立方體多余物測量尺寸普遍大于設計尺寸,最大絕對誤差不超過50 μm。通過顯微CT壁厚分析發現,寬段流道均勻性良好。
1 試驗材料與方法
1.1 試驗材料
以GH3625粉末為原材料,采用自主設計的S310型激光選區熔化增材制造系統制備內部流道試樣,模擬超燃沖壓發動機燃燒室流道結構。表1為GH3625合金的化學成分,圖1為增材制造內部流道試樣CAD設計剖面圖與實物圖。試樣尺寸:外徑為80mm,壁厚為5mm,高為100mm;內部分為寬窄兩段不同尺寸的流道,窄段流道為2mm×1.5mm×50mm,寬段流道為3 mm×2mm×50mm;窄段每條流道內部預制10個凸出立方體多余物,尺寸分別為0.2、0.2、0.15、0.15、0.1、0.1、0.1、0.08、0.08和0.08mm,編號依次為1~10;寬段流道內部放置7根鎳標準絲型像質計(HB7684-2000)模擬線形多余物,絲徑分別為0.4、0.32、0.25、 0.20、0.16、0.125 和 0.1 mm,絲號分別對應10~16。

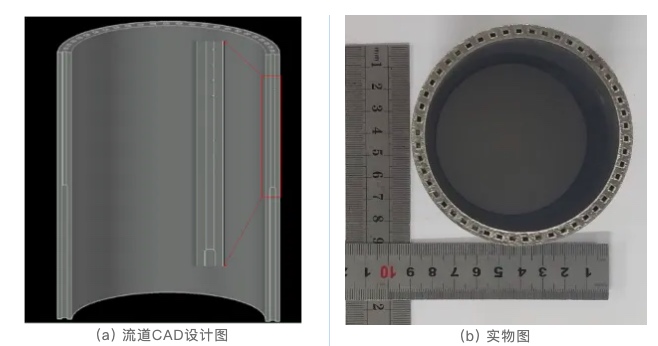
圖1 流道試樣設計圖與實物圖
1.2 透照分析與試驗
圖2為流道增材制件CT透照布置示意圖。當焦距為765mm檢測時,X射線對窄段流道最小和最大透照厚度分別為7mm和35mm,寬段流道最小和最大透照厚度分別為6mm和31mm,兩種情況下最大透照厚度均約為最小透照厚度的5倍。針對上述情況,采用小焦點射線機進行CR檢測,可有效檢測出其內部缺陷;采用顯微CT檢測流道多余物并進行尺寸測量。
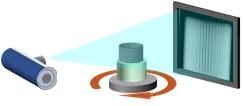
圖2 流道增材制件CT掃描布置示意圖
1.2.1 X射線CR試驗
采用ISOVOLT320Titan E射線機 ,焦點尺寸為0.4mm×0.4mm,CR掃描儀采用CRx25P,激光焦點為12.5μm,配套超高分辨率IPU成像板。采用源在外單壁透照,試驗焦距為900mm,管電壓為130kV,管電流為6mA,曝光時間為120s,鎳絲像質計放置在寬流道源測表面。
1.2.2 顯微CT試驗
采用YXLON FF85顯微CT成像系統,其中微焦點射線源為Microfocus tube 225kV,最大管電壓為225kV,焦點尺寸最小為6μm;平板探測器為VAREX 4343HE型非晶硅平板探測器,其閃爍體材料為碘化銫,探測器單元尺寸為139μm×139μm,成像矩陣為3072×3072,A/D位數為16 bit。CT掃描試驗參數:源到試樣旋轉中心距離為165mm,源到探測器距離為765mm,管電壓為220kV,管電流為360μA,單張投影圖像積分時間為2.31s,在360°范圍內共獲得3059張投影圖像,成像分辨率為30μm。
2 試驗結果與分析
2.1 CR結果與分析
對GH3625高溫合金SLM增材制造流道試樣進行CR試驗,結果見圖3,其中圖3a箭頭處為識別出的預制凸出立方體多余物缺陷,每個流道均能檢出4個立方體多余物,箭頭1~4是尺寸分別為0.2、0.2、0.15和0.15mm的凸出立方體多余物。從檢測靈敏度方面,圖3b中可識別像質計16號絲,滿足GB/T 26642-2022的A級要求。從線形多余物檢出能力方面,可檢出的最小線形多余物為第16號絲,絲徑為0.1mm。可以看出,CR試驗能夠檢出最小設計尺寸為0.15mm的凸出立方體多余物和最小絲徑為0.1 mm的線形多余物,但受檢測靈敏度的影響,設計尺寸≤0.1 mm的凸出立方體多余物容易漏檢。
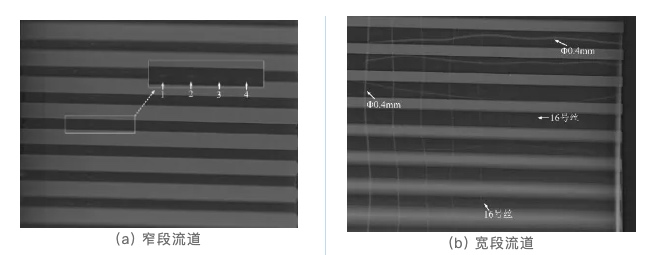
圖3 流道多余物CR圖像
2.2 CT結果與分析
根據顯微CT重建圖像,可在不同切片圖像上觀察缺陷及流道內部結構,有利于多余物缺陷的定位和定量,同時可對流道壁厚進行分析。
2.2.1 多余物檢測
圖4為窄段流道多余物切片圖像分析結果,圖4b中箭頭處為凸出立方體多余物。可以看出,設計尺寸為0.08~0.20mm,所有預制立方體多余物均被檢出。
為了進一步分析顯微CT對立方體多余物缺陷檢出能力,選取圖4a中4個流道進行多余物尺寸分析,對其凸出方向的最大距離進行測量。表2為4個流道內部1~10號凸出立方體多余物設計尺寸、4個流道處測量尺寸、平均測量尺寸及絕對誤差。可以看出,凸出立方體多余物實測尺寸普遍大于設計尺寸,1~10號立方體多余物的絕對誤差在20~50μm范圍內,CT 最小可測量的立方體多余物尺寸為0.1mm。
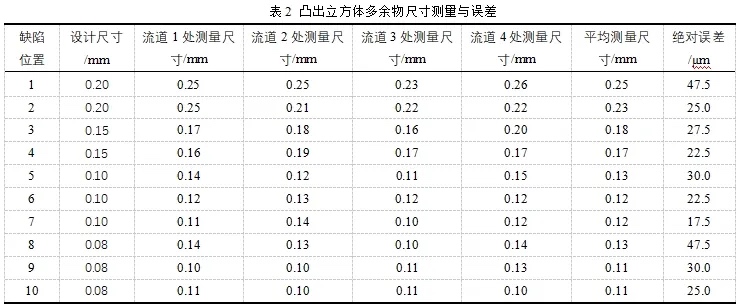
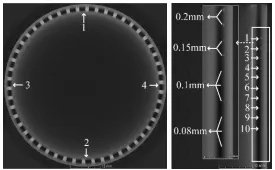
(a) Z軸切片圖像 (b) 含凸出立方體多余物Y軸切片圖像
圖4 窄段流道多余物切片圖像分析
(責任編輯:admin)
最新內容
熱點內容