韓國研究人員完成3D打印鈦罐-196°C耐低溫壓力測試,未發生結構故障
時間:2025-06-26 09:17 來源:南極熊 作者:admin 閱讀:次
2025年6月25日,由韓國產業技術研究院(KITECH)牽頭的聯合體(KITECH是一家隸屬于韓國的國家級應用研究中心)完成了全球首個用于航天的激光3D打印鈦合金壓力容器的。
研究團隊與韓國航空宇宙研究院(KARI)、KP Aero Industries、AM Solutions和漢陽大學合作,用Ti-6Al-4V合金制造了一個130升的球形儲罐,并在-196°C下加壓至330巴(比220巴的工作要求高出50%),且未發生結構故障。KITECH 的工程師采用激光絲定向能量沉積技術制造了兩個直徑 640 毫米的半球,利用高功率光束逐層熔化鈦絲原料。實時傳感器跟蹤焊道的幾何形狀和熱輸入,而刀具路徑算法則補償變形,使厚度保持在航空航天公差范圍內。經過熱處理和精密加工后,KP Aero 將兩個半球焊接在一起,經無損檢測確認沒有孔隙或未熔合缺陷。
韓國航天工業研究院首席研究員李赫博士說道:“這一成就證明,增材制造技術能夠滿足太空任務的極致性能要求,為航空航天部件制造開辟了新的可能性。”在韓國航天研究院設施的驗證運行中,應變計、熱電偶和視覺監控系統顯示,儲罐行為與有限元預測結果相符,證實了飛行硬件所需的設計裕度。
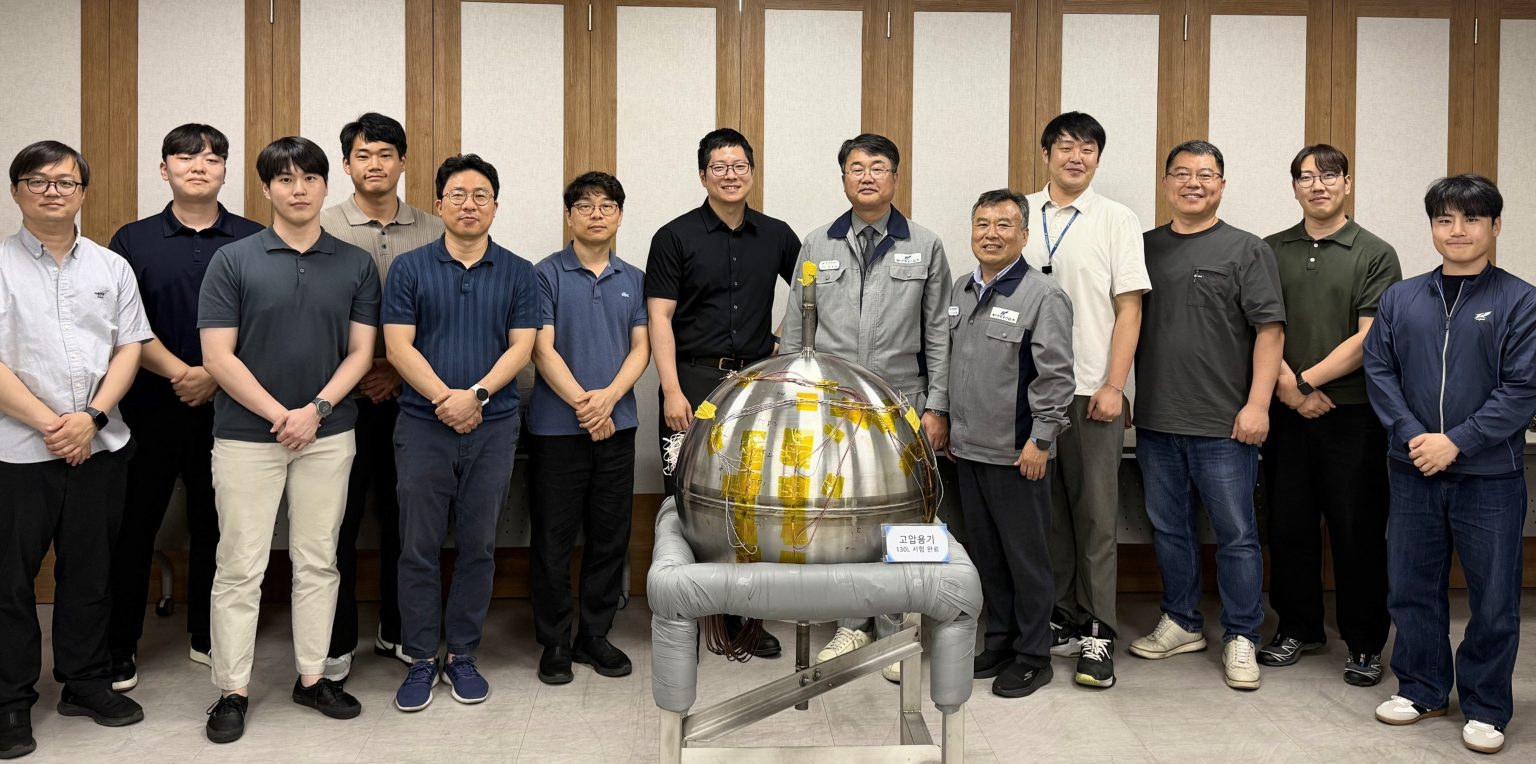
△來自韓國科技工業研究院 (KITECH)、韓國航天研究院 (KARI)、KP Aero Industries、AM Solutions 和漢陽大學的研究人員與 130 升鈦合金推進劑罐合影。圖片來自 KITECH。
多年來,增材制造技術一直有望實現更輕、更快速的推進劑儲箱生產,但由于工藝波動性和低溫脆化問題,人們對其信心不足。激光絲材沉積工藝無需鍛造模具和大量機械加工,從而縮短了交付周期并減少了材料浪費,但只有經過嚴格的測試才能證明在液氮溫度和運載火箭壓力下的可靠性。如今,這一障礙已被掃除,這提供了一個數據點,表明金屬3D打印工藝能夠滿足傳統上只有鍛造結構才能滿足的安全系數。研究小組計劃進行更多資格認證周期,并計劃與商業發射供應商合作,將3D打印技術應用于衛星、上面級推進劑貯箱和其他低溫子系統。韓國航天技術研究院(KITECH)成立于1989年,隸屬于韓國商工部,研究院表示將利用這些成果支持韓國更廣泛地推進國產航天硬件和數字化制造。
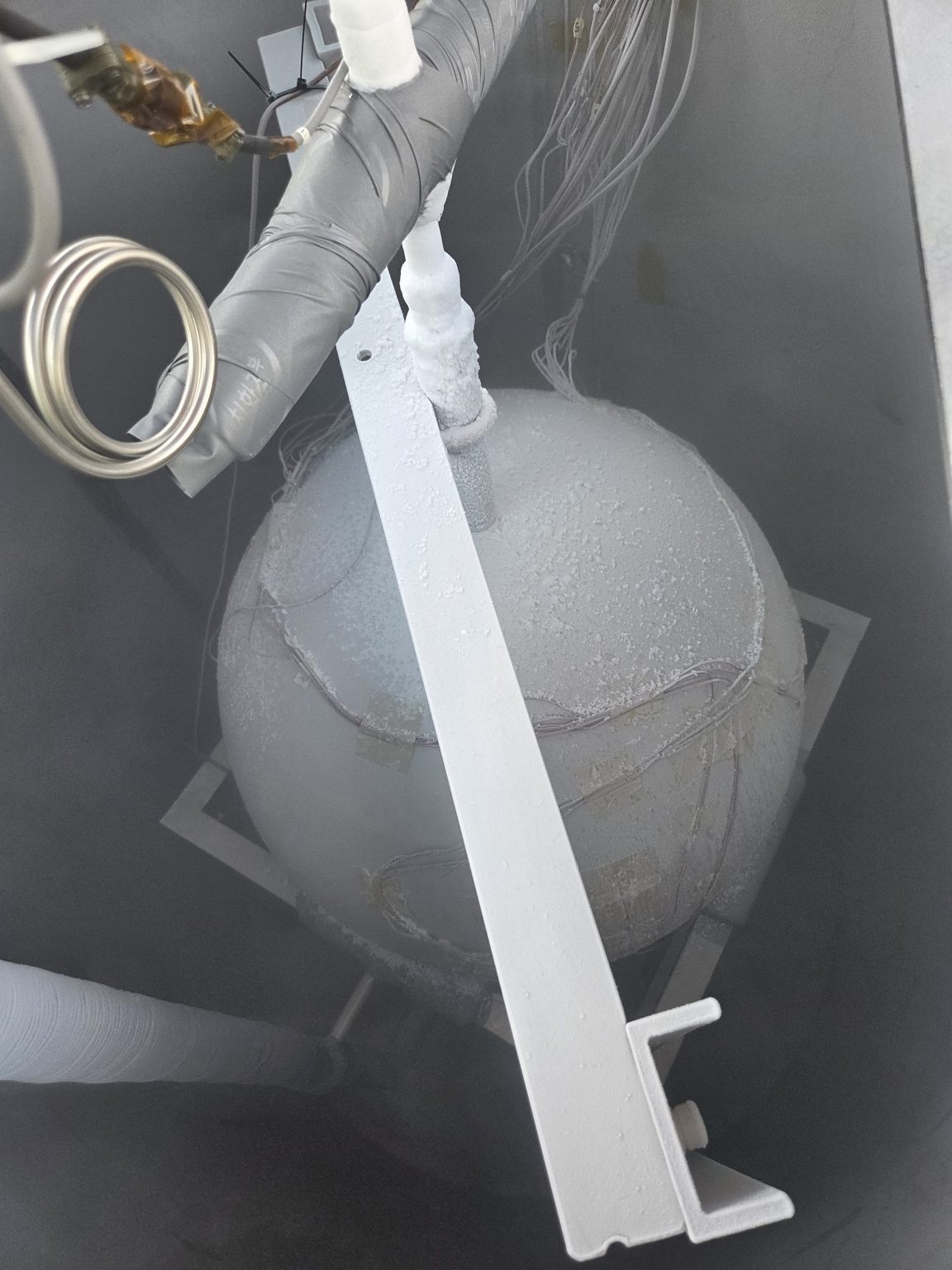
△在韓國核工業研究院測試設施的驗證過程中,3D打印鈦合金罐在-196°C下被加壓至330巴。圖片來自韓國核工業研究院。
韓國增材制造的發展
韓國近期加快了金屬增材制造在航空航天領域的應用。航天公司INNOSPACE成立了內部先進制造部門,利用專有的3D打印系統生產火箭發動機和關鍵部件。該部門運營著一條涵蓋設計、仿真、金屬打印、后處理和質量控制的全集成生產鏈,并成為韓國首家獲得ISO/ASTM 52941-20航空航天級增材制造系統認證的公司。研究團隊已完成HANBIT運載火箭13個部件的初步制造,包括氧化劑泵和高精度旋轉部件。
國防部門的平行努力也取得了進展。同年,韓國海軍陸戰隊后勤集團驗證了Meltio的線激光定向能量沉積 (DED) 工藝可用于移動金屬3D打印裝置。Meltio系統通過機械臂部署在集裝箱裝置內,可按需制造兩棲突擊車輛的停產或難以采購的零件。這是Meltio技術在亞洲的首次軍事應用,并得到了當地合作伙伴AM Solutions(低溫儲罐項目的合作者之一)的支持。
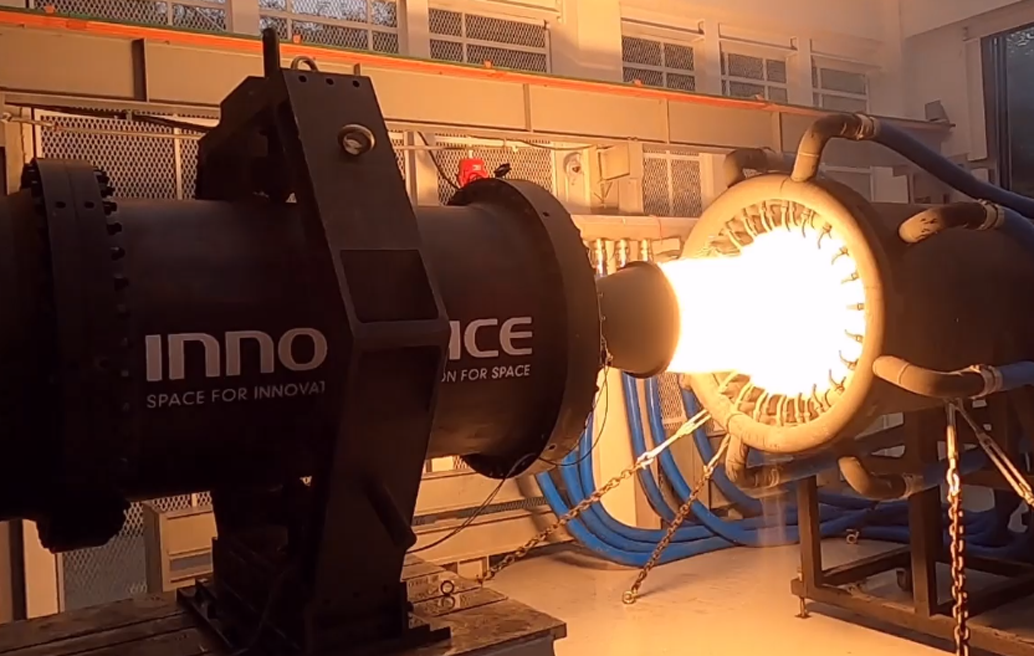
△地面燃燒測試中心。圖片來自 INNOSPACE。
(責任編輯:admin)
最新內容
熱點內容