你覺得電弧增材不就是焊接嗎?
時間:2022-06-23 13:55 來源:格智學院 作者:admin 閱讀:次
電弧增材不就是焊接嗎?相信這個靈魂問題,絕大多數接觸過電弧增材的朋友,都問過或者被問過。的確,無論從工藝原理或者裝備構成上,電弧增材都和焊接有著太多相同或相似之處,因而有此一問并不讓人意外。那么,電弧增材究竟與焊接是什么關系,又有著哪些異同呢?希望這篇文章可以給大家一個答案。
電弧增材是焊接嗎?
要回答這個問題,我們就要先了解焊接的定義,然后再依據定義來判斷電弧增材是否符合。
根據焊接的定義,電弧增材完全可以理解為采用電弧作為熱源,對材料進行加熱,用金屬絲材作為填充材料,使同種或異種材料達到原子間結合從而形成工件的一種加工方法。
顯而易見,電弧增材無疑就是一種焊接技術。然而,我們不妨順著這個思路再進一步。從定義的角度來說,金屬增材制造的各種技術路線,無論是成熟度更高的激光粉末床熔融增材技術,還是后起之秀的激光能量沉積,電弧增材,等離子熔絲增材,電子束熔絲增材等,似乎也都符合焊接的定義。而事實上,如果我們將常見的焊接方法和增材工藝技術路線進行對比,我們就不難發現,二者之間驚人的相似。
焊接方法總體上可以分為三大類:熔焊、釬焊、壓力焊。其中熔焊包括:電弧焊、激光焊、電子束焊、等離子弧焊等,壓力焊包括:電阻焊、攪拌摩擦焊、冷噴焊接、超聲波焊接等。
而我們常見的金屬增材技術則包括:電弧增材、激光粉末床熔融,激光定向能量沉積,電子束熔絲增材,等離子增材,也包括近來逐漸受到關注的攪拌摩擦增材、冷噴增材等等。
圖片來源:AMPower
到這里,結論已經呼之欲出。不僅僅電弧增材是焊接技術,絕大多數金屬增材技術都與焊接技術同根同源。
這個結論讓人覺得意料之外卻又在情理之中,因為焊接技術與增材技術從來都不是兩個互相排斥或是互相包含的概念,它們是從兩個完全不同的角度對技術進行定義和分類的。因此,一項技術方法既是焊接又是增材也是完全可能的。然而這個結論似乎并不能解答大家真正的疑問,因為比起電弧增材是不是焊接,其實大家更想問的是:作為一種焊接技術,我們為什么要把電弧增材定義為一種增材技術,而不是就叫它電弧焊呢?
這個問題背后,可能反映的是大家的一個認知誤區。因為往往我們提到金屬增材制造或者金屬3D打印,大家首先會想到的是激光粉末床熔融(SLM)技術,甚至有人會覺得SLM是增材制造,而電弧增材不是。當然這也情有可原,因為SLM技術確實是目前被認為技術成熟度和工業化程度最高的金屬增材技術。然而受限于效率、成本和質量,SLM技術更適用于小型精細的金屬零件增材,而電弧增材自由的成型環境對零件尺寸幾乎無限制,成型效率可達每小時幾公斤,更適合中大型到超大型復雜金屬構件的制造,隨著近年來技術成熟度和工業化程度逐步達到了工業化應用的水平,逐漸被越來越多的人關注。
圖片來源:AMPower
因此我們要回答上面的問題,首先就需要拋開“金屬3D打印=SLM技術”的刻板印象。然后我們通過了解增材制造以及電弧增材的定義,來尋找答案。
增材制造定義:以三維模型數據為基礎,通過材料堆積的方式制造零件或實物的工藝。
從增材制造的定義,我們可以看到三個關鍵的要素:
第一,是原型制造,描述了增材制造的用途,是用于零件或實物的原型制造、快速成型;
第二,是模型驅動,定義了增材制造一定是一種數字化技術;
第三,是逐層堆積,說明了增材制造自下而上、從無到有的過程。
這三個要素,恰恰體現了電弧增材與焊接之間的不同。
電弧增材制造技術(Wire Arc Additive Manufacture,WAAM)是一種采用電弧或等離子弧作為熱源將金屬絲材熔化,在程序或軟件控制下采用逐層熔覆原理,根據三維數字模型由線-面-體制造出接近產品形狀和尺寸要求的三維金屬坯件的先進數字化制造技術。
差異一:原型制造
電弧增材是從無到有直接進行原型制造、快速成型的過程。而一般來講,焊接的應用場景包括工件的連接和表面改性,都是在已有的零件上進行加工的手段。因此從應用場景上來說,電弧增材與焊接就是不同的。而不同的應用場景,就意味著不同的目標和要求。我們以和增材更為接近的堆焊為例。
堆焊作為材料表面改性的一種經濟而快速的工藝方法,可以提高產品和設備的性能、延長使用壽命、降低成本,因此越來越多地應用于各個工業部門零件的制造和修復中。堆焊技術是表面工程中一個很重要的分支,它是將具有一定使用性能的合金材料借助一定的熱源手段熔敷在母體材料的表面,以賦予母材特殊使用性能或使零件恢復原有形狀尺寸的工藝方法。因為它是在普通材質的基礎上制備出需要的耐磨、耐熱以及耐腐蝕等特種性能的堆焊層的,所以在節約能源、節省材料、環境保護等方面展示了巨大的經濟效益。
電弧增材制造技術成型的零件由全焊縫金屬構成,化學成分均勻、致密度高,在逐層堆積過程中,零件會經過多次加熱,經歷多次淬火和正火,可以消除大型鑄件中存在的不易淬透、宏觀偏析、強度和韌性的各向異性等問題。另一方面,電弧增材制造無需模具,工序少工藝鏈短,整體制造周期短,自由的成型環境對零件尺寸幾乎無限制,成型效率可達每小時幾公斤,適合中大型到超大型復雜金屬構件的制造。
差異二:模型驅動
由于電弧增材是用于零件的快速成型的,因此不管是通過CAD軟件自主設計亦或是通過視覺逆向重構生成,電弧增材制造的工作流程起點都一定是零件的三維數模。而對于焊接來說,則并沒有這一項要求。具體來說,焊接過程要完成的是“點”或“線”的連接或是“面”的覆蓋,而電弧增材要完成的是“體”的堆積,而這個“體”就是零件的三維數模。
模型驅動的差異,衍生出的是工藝編程方式的截然不同。即便是機器人焊接或堆焊,由于路徑復雜程度低,大多數時候編程都可以通過手工示教或配合簡單的軌跡偏移即可完成。然而電弧增材,需要首先將目標工件的三維模型通過軟件在垂直于水平方向上或者是在曲面上進行2D分解,每個分解層對應著實際的沉積層,由執行機構帶動金屬熔池沿著通過軟件規劃好的由數萬個甚至更多“空間點”組成的復雜空間軌跡,逐層沉積最終形成實體零件。如此復雜的空間軌跡,自然無法通過傳統焊接的編程方式實現,而必須依靠專業的CAM軟件。這也是為什么,軟件是電弧增材一項至關重要的技術分支。更多關于軟件的重要性,大家可以查閱上一篇文章,里面有更詳細的講解,這里就不再展開。
差異三:逐層堆積
上面我們說到了,電弧增材是要完成零件三維“體”的堆積,就需要沿著復雜的空間軌跡將材料逐層堆積。而逐層堆積的過程,帶來的絕不僅僅是軌跡編程上的差異。
電弧增材完成零件通常需要增材數百甚至數千層,這就對工藝質量的穩定性,過程缺陷的即時識別與修復的要求都提升了數個量級,因為一旦增材過程中出現缺陷,又未能及時識別和修復,就會導致整個產品的報廢,造成無法估量的損失。因此為保障增材質量,除了對裝備的穩定性要求更高之外,增材過程中通常需要采用各種過程監控手段,如工藝參數監控、形貌監控、熔池監控等等,再通過智能化軟件輔助對過程缺陷進行識別和修復。
與此同時,不同的質量要求,意味著焊接領域相對成熟的各項標準、規范、體系,僅供參考,不能拿來主義的應用于電弧增材。事實上電弧增材制造目前可供參考的質量標準寥寥,比如《GB/T 39253-2020增材制造 金屬材料定向能量沉積工藝規范》以及《GB/T 39254-2020增材制造 金屬制件機械性能評價通則》,然而落到各行各業的生產實踐中,適合于電弧增材的工藝規范或是檢測標準幾乎空白,從而使得工藝認證變得困難重重。因此標準體系的建立和完善可以說是整個電弧增材行業目前最關注的,甚至可以說是影響著電弧增材技術得到更廣泛應用的核心痛點。然而標準化之路漫漫,仍然需要更大的投入和更廣泛的參與,更需要經過實踐漫長的檢驗,只能說,吾將上下而求索吧。
傳統的新生
相信到這里,電弧增材與焊接之間的關系大家應該已經了然。它絕不是簡單的新瓶裝舊酒,而是一項傳承了三千年的傳統技術,復合了更多學科和技術領域,蛻變后的新生。但如果我們的眼光再長遠些,焊接技術也在不斷向著智能化、數字化的方向發展,而電弧增材技術也會不斷成熟和完善,在不遠的將來,彼此之間的界限會不會越來越模糊,融合甚至孵化出新的可能呢?
讓我們拭目以待。
推動行業發展需要低使用門檻的軟件和專業技術人才
任何新興制造技術的發展,都需要裝備、軟件、材料、工藝、人才五大核心要素協同發展,缺一不可。
對電弧增材技術來說,其工藝本身與有著悠久歷史的焊接工藝同根同源,因此巨大的機器人焊接應用市場存量對應的裝備、工藝、材料經驗儲備都應該可以成為電弧增材技術發展的土壤。然而現實情況是,時至今日,電弧增材技術的應用依然局限在少數場景,歸其原因木桶的短板在于早期軟件和人才兩個要素的缺失,制約了行業的發展。
相信隨著專用CAM軟件的出現和發展,對專業技術人才的要求門檻也隨之不斷被降低,用戶可以越來越專注于工藝和產品的開發,從而不斷將電弧增材技術的潛力充分發掘出來。
電弧增材是焊接嗎?
要回答這個問題,我們就要先了解焊接的定義,然后再依據定義來判斷電弧增材是否符合。
-
焊接的定義:通過加熱或加壓,或兩者并用,并且用或不用填充材料,使同種或異種工件達到原子間結合的一種加工方法。
根據焊接的定義,電弧增材完全可以理解為采用電弧作為熱源,對材料進行加熱,用金屬絲材作為填充材料,使同種或異種材料達到原子間結合從而形成工件的一種加工方法。
顯而易見,電弧增材無疑就是一種焊接技術。然而,我們不妨順著這個思路再進一步。從定義的角度來說,金屬增材制造的各種技術路線,無論是成熟度更高的激光粉末床熔融增材技術,還是后起之秀的激光能量沉積,電弧增材,等離子熔絲增材,電子束熔絲增材等,似乎也都符合焊接的定義。而事實上,如果我們將常見的焊接方法和增材工藝技術路線進行對比,我們就不難發現,二者之間驚人的相似。
焊接方法總體上可以分為三大類:熔焊、釬焊、壓力焊。其中熔焊包括:電弧焊、激光焊、電子束焊、等離子弧焊等,壓力焊包括:電阻焊、攪拌摩擦焊、冷噴焊接、超聲波焊接等。
而我們常見的金屬增材技術則包括:電弧增材、激光粉末床熔融,激光定向能量沉積,電子束熔絲增材,等離子增材,也包括近來逐漸受到關注的攪拌摩擦增材、冷噴增材等等。
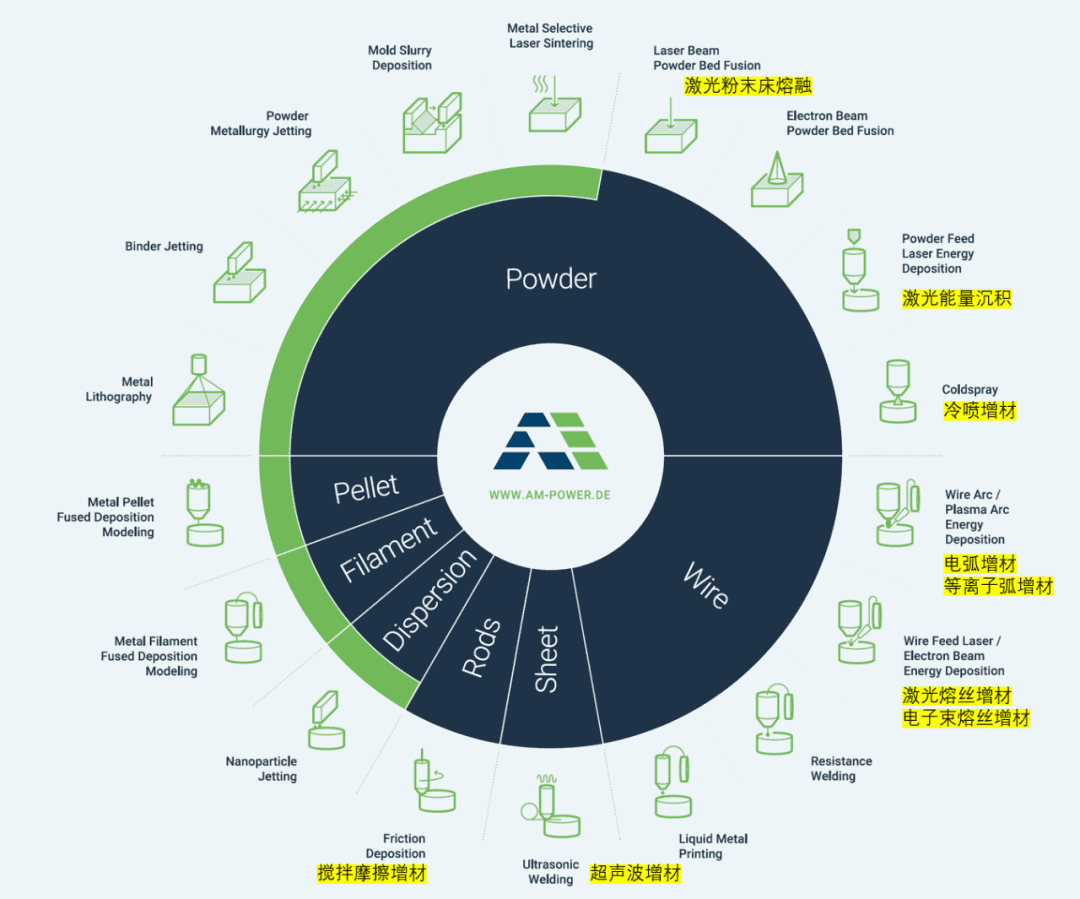
圖片來源:AMPower
到這里,結論已經呼之欲出。不僅僅電弧增材是焊接技術,絕大多數金屬增材技術都與焊接技術同根同源。
這個結論讓人覺得意料之外卻又在情理之中,因為焊接技術與增材技術從來都不是兩個互相排斥或是互相包含的概念,它們是從兩個完全不同的角度對技術進行定義和分類的。因此,一項技術方法既是焊接又是增材也是完全可能的。然而這個結論似乎并不能解答大家真正的疑問,因為比起電弧增材是不是焊接,其實大家更想問的是:作為一種焊接技術,我們為什么要把電弧增材定義為一種增材技術,而不是就叫它電弧焊呢?
這個問題背后,可能反映的是大家的一個認知誤區。因為往往我們提到金屬增材制造或者金屬3D打印,大家首先會想到的是激光粉末床熔融(SLM)技術,甚至有人會覺得SLM是增材制造,而電弧增材不是。當然這也情有可原,因為SLM技術確實是目前被認為技術成熟度和工業化程度最高的金屬增材技術。然而受限于效率、成本和質量,SLM技術更適用于小型精細的金屬零件增材,而電弧增材自由的成型環境對零件尺寸幾乎無限制,成型效率可達每小時幾公斤,更適合中大型到超大型復雜金屬構件的制造,隨著近年來技術成熟度和工業化程度逐步達到了工業化應用的水平,逐漸被越來越多的人關注。
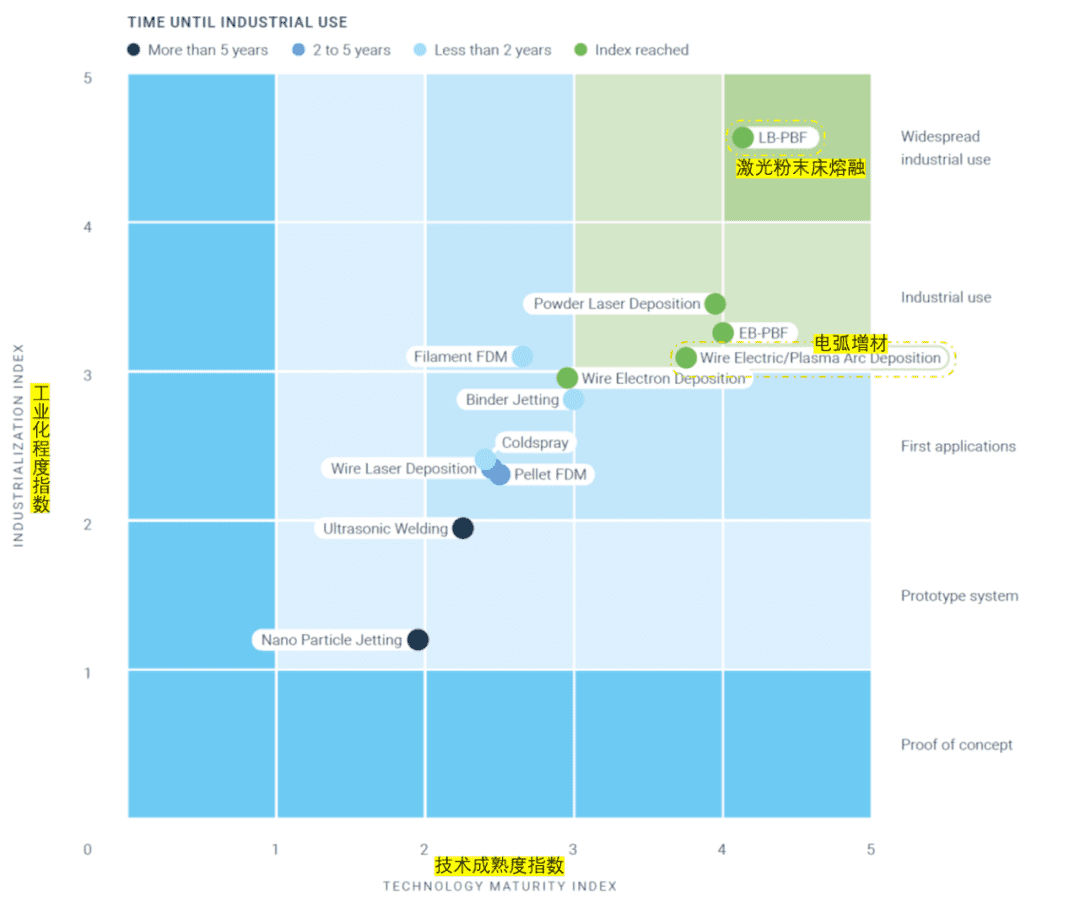
圖片來源:AMPower
增材制造定義:以三維模型數據為基礎,通過材料堆積的方式制造零件或實物的工藝。
從增材制造的定義,我們可以看到三個關鍵的要素:
第一,是原型制造,描述了增材制造的用途,是用于零件或實物的原型制造、快速成型;
第二,是模型驅動,定義了增材制造一定是一種數字化技術;
第三,是逐層堆積,說明了增材制造自下而上、從無到有的過程。
這三個要素,恰恰體現了電弧增材與焊接之間的不同。
電弧增材制造技術(Wire Arc Additive Manufacture,WAAM)是一種采用電弧或等離子弧作為熱源將金屬絲材熔化,在程序或軟件控制下采用逐層熔覆原理,根據三維數字模型由線-面-體制造出接近產品形狀和尺寸要求的三維金屬坯件的先進數字化制造技術。
差異一:原型制造
電弧增材是從無到有直接進行原型制造、快速成型的過程。而一般來講,焊接的應用場景包括工件的連接和表面改性,都是在已有的零件上進行加工的手段。因此從應用場景上來說,電弧增材與焊接就是不同的。而不同的應用場景,就意味著不同的目標和要求。我們以和增材更為接近的堆焊為例。
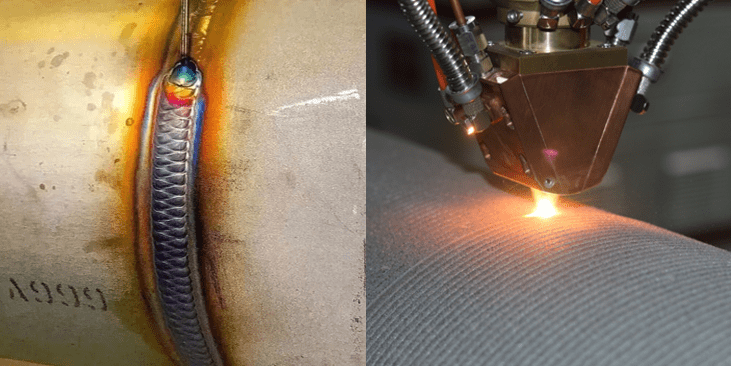
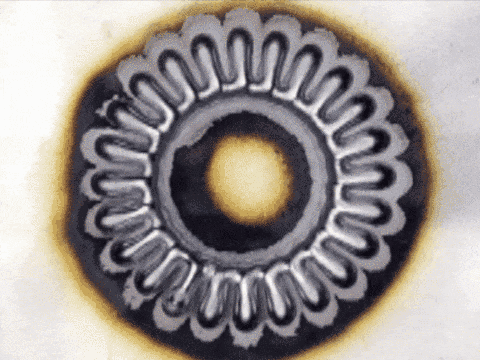
電弧增材制造技術成型的零件由全焊縫金屬構成,化學成分均勻、致密度高,在逐層堆積過程中,零件會經過多次加熱,經歷多次淬火和正火,可以消除大型鑄件中存在的不易淬透、宏觀偏析、強度和韌性的各向異性等問題。另一方面,電弧增材制造無需模具,工序少工藝鏈短,整體制造周期短,自由的成型環境對零件尺寸幾乎無限制,成型效率可達每小時幾公斤,適合中大型到超大型復雜金屬構件的制造。
差異二:模型驅動
由于電弧增材是用于零件的快速成型的,因此不管是通過CAD軟件自主設計亦或是通過視覺逆向重構生成,電弧增材制造的工作流程起點都一定是零件的三維數模。而對于焊接來說,則并沒有這一項要求。具體來說,焊接過程要完成的是“點”或“線”的連接或是“面”的覆蓋,而電弧增材要完成的是“體”的堆積,而這個“體”就是零件的三維數模。
模型驅動的差異,衍生出的是工藝編程方式的截然不同。即便是機器人焊接或堆焊,由于路徑復雜程度低,大多數時候編程都可以通過手工示教或配合簡單的軌跡偏移即可完成。然而電弧增材,需要首先將目標工件的三維模型通過軟件在垂直于水平方向上或者是在曲面上進行2D分解,每個分解層對應著實際的沉積層,由執行機構帶動金屬熔池沿著通過軟件規劃好的由數萬個甚至更多“空間點”組成的復雜空間軌跡,逐層沉積最終形成實體零件。如此復雜的空間軌跡,自然無法通過傳統焊接的編程方式實現,而必須依靠專業的CAM軟件。這也是為什么,軟件是電弧增材一項至關重要的技術分支。更多關于軟件的重要性,大家可以查閱上一篇文章,里面有更詳細的講解,這里就不再展開。
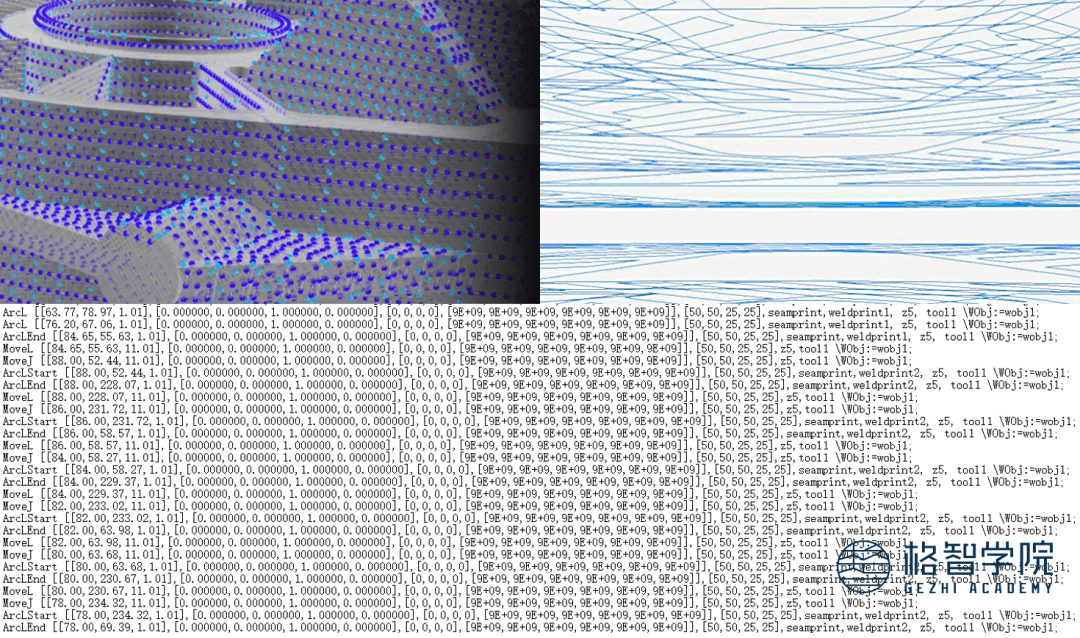
差異三:逐層堆積
上面我們說到了,電弧增材是要完成零件三維“體”的堆積,就需要沿著復雜的空間軌跡將材料逐層堆積。而逐層堆積的過程,帶來的絕不僅僅是軌跡編程上的差異。
電弧增材完成零件通常需要增材數百甚至數千層,這就對工藝質量的穩定性,過程缺陷的即時識別與修復的要求都提升了數個量級,因為一旦增材過程中出現缺陷,又未能及時識別和修復,就會導致整個產品的報廢,造成無法估量的損失。因此為保障增材質量,除了對裝備的穩定性要求更高之外,增材過程中通常需要采用各種過程監控手段,如工藝參數監控、形貌監控、熔池監控等等,再通過智能化軟件輔助對過程缺陷進行識別和修復。
與此同時,不同的質量要求,意味著焊接領域相對成熟的各項標準、規范、體系,僅供參考,不能拿來主義的應用于電弧增材。事實上電弧增材制造目前可供參考的質量標準寥寥,比如《GB/T 39253-2020增材制造 金屬材料定向能量沉積工藝規范》以及《GB/T 39254-2020增材制造 金屬制件機械性能評價通則》,然而落到各行各業的生產實踐中,適合于電弧增材的工藝規范或是檢測標準幾乎空白,從而使得工藝認證變得困難重重。因此標準體系的建立和完善可以說是整個電弧增材行業目前最關注的,甚至可以說是影響著電弧增材技術得到更廣泛應用的核心痛點。然而標準化之路漫漫,仍然需要更大的投入和更廣泛的參與,更需要經過實踐漫長的檢驗,只能說,吾將上下而求索吧。
傳統的新生
相信到這里,電弧增材與焊接之間的關系大家應該已經了然。它絕不是簡單的新瓶裝舊酒,而是一項傳承了三千年的傳統技術,復合了更多學科和技術領域,蛻變后的新生。但如果我們的眼光再長遠些,焊接技術也在不斷向著智能化、數字化的方向發展,而電弧增材技術也會不斷成熟和完善,在不遠的將來,彼此之間的界限會不會越來越模糊,融合甚至孵化出新的可能呢?
讓我們拭目以待。
推動行業發展需要低使用門檻的軟件和專業技術人才
任何新興制造技術的發展,都需要裝備、軟件、材料、工藝、人才五大核心要素協同發展,缺一不可。
對電弧增材技術來說,其工藝本身與有著悠久歷史的焊接工藝同根同源,因此巨大的機器人焊接應用市場存量對應的裝備、工藝、材料經驗儲備都應該可以成為電弧增材技術發展的土壤。然而現實情況是,時至今日,電弧增材技術的應用依然局限在少數場景,歸其原因木桶的短板在于早期軟件和人才兩個要素的缺失,制約了行業的發展。
相信隨著專用CAM軟件的出現和發展,對專業技術人才的要求門檻也隨之不斷被降低,用戶可以越來越專注于工藝和產品的開發,從而不斷將電弧增材技術的潛力充分發掘出來。
(責任編輯:admin)
最新內容
熱點內容