仿生3D打印實現"軟硬通吃" - UT-Austin Zachariah A. Page教授團隊
自然界中,硬材料和軟材料常常被巧妙組合,形成既堅固又柔韌的復雜結構,這也是科學家試圖用3D打印技術仿生的方向。然而,目前多材料3D打印還面臨不少難題,比如打印速度慢、材料性能不穩定、硬軟材料之間界面脆弱等。灰度光固化和多色光固化是兩種常見方案,前者通過控制光強調節局部硬度,雖然強度差異大,但軟性區域易殘留未反應單體,影響穩定性;后者通過不同顏色光驅動不同化學反應,能精準控制材料組合,但普遍存在打印速度慢、材料強度不足、界面易脆化的問題。因此,想要實現打印速度快、硬軟強度差異大、力學性能可調、結構穩定的高性能多材料3D打印,仍需要在材料配方和打印工藝上進一步創新(圖1a)。
據此,美國德克薩斯大學奧斯汀分校(UT-Austin)Zachariah A. Page教授團隊通過設計一種混合環氧-丙烯酸酯樹脂,結合波長選擇性光引發體系,實現了多材料數字光處理(DLP)3D打印。該樹脂在紫外光(365 nm)下固化形成高強度(69 MPa)硬質材料,在紫光(405 nm)下形成高彈性(260%應變)軟質材料,兩者界面通過共價鍵結合,解決了傳統多材料打印的界面分離問題。通過灰度多色投影技術,成功打印了仿生膝關節、硬彈簧軟圓柱等結構,并驗證了在可拉伸電子器件中的應用潛力。
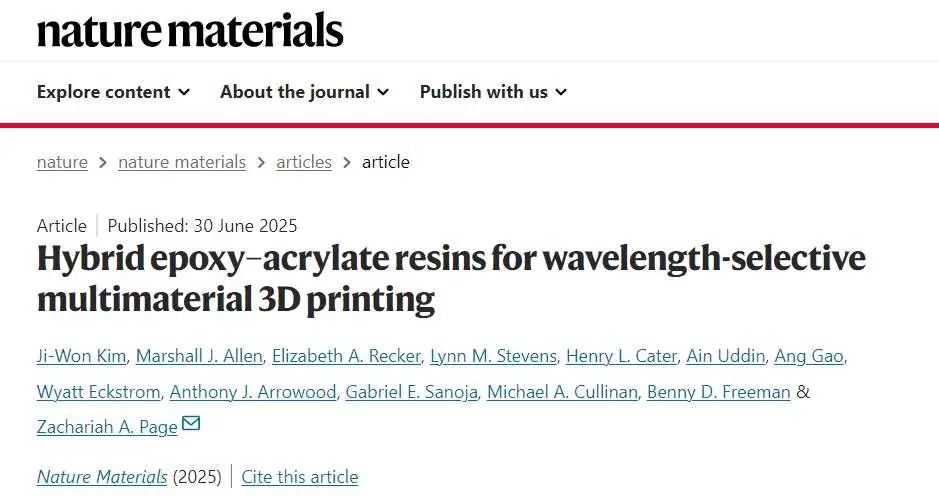
2025年6月30日,相關工作以“ Hybrid epoxy–acrylate resins for wavelength-selective multimaterial 3D printing ” 為題發表在Nature Materials上。
展示傳統方法(圖1a) ,其一為灰度打印,用丙烯酸樹脂時低光區殘留大量未反應單體(溶膠分數高),如 Qi 等用灰度 DLP 實現 ΔE~30,000 倍但溶膠分數達 90 wt%;其二為多色打印,混合環氧 - 丙烯酸樹脂需后固化且單體去除致收縮,如 Schwartz 等方法 ΔE 僅 7.5 倍,打印速度≤0.10 mm/min。(圖 1b) 為本文方法,采用雜化環氧 - 丙烯酸酯樹脂,通過波長選擇性光固化,實現高打印速率、功能團間共價鍵合,且機械性能差異大、溶膠分數低。列舉多材料 3D 打印結構關鍵示例及代表性力學性能(圖1c),本文材料在 ΔE(~3000 倍)、σmax(~69 MPa)、εf(>250%)、彈性恢復(≥90%)等方面性能突出,顯著優于參考文獻中的結果,展現了該方法的先進性。
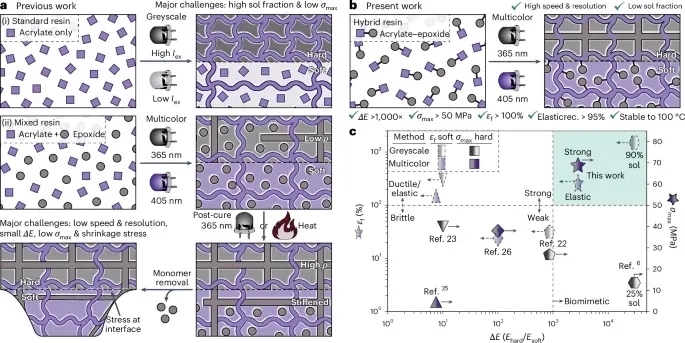
開發了一種混合丙烯酸酯-環氧單體ECA((3,4-環氧環己基)甲基丙烯酸酯),通過波長選擇性光固化,實現多材料3D打印(圖2a)。ECA結合了環氧基高反應性和丙烯酸酯的良好加工性,能通過紫外光和可見光分別驅動不同化學反應,增強硬軟材料界面結合。為優化光敏體系,篩選了多種光酸發生劑和光引發劑,最終選用BAPO作為紫光引發劑,THS與新開發的MeOTX作為高選擇性的紫外光助敏劑(圖2b),大幅提升了紫外區環氧固化速率。通過紅外實時光譜監測,團隊優化了樹脂配方,加入HEA和TEGDA調整粘度和機械性能,在365/405nm光源下,混合樹脂能在幾秒內快速固化(圖2c、2d),滿足DLP 3D打印對速度和力學性能的需求。

利用多色DLP 3D打印機,測試了一系列混合樹脂體系,結合不同配比的ECA、HEA、TEGDA等組分(圖3a)。通過調控紫外(365 nm)和紫光(405 nm)投影強度,打印速度可達0.25–1.5 mm/min,分辨率高達25 μm。機械性能測試表明,紫外固化樣品表現為高強度、剛性塑料(彈性模量1700 MPa),而紫光固化樣品柔軟可拉伸,彈性模量僅0.6 MPa,最大拉伸率達260%。進一步的拉伸、壓縮和循環測試顯示,軟材料具有優異的彈性恢復性,循環拉伸100次后仍保持>99%形變恢復,性能甚至優于天然橡膠(圖3b、3c)。熱性能測試表明,軟、硬材料均具良好的熱穩定性,分解溫度高于330℃,軟材料的玻璃轉變溫度(Tg)為18℃,硬材料為140℃,并具備較好的可調性和能量吸收潛力(圖3d)。
通過顏色對比、拉伸測試和納米壓痕,系統評估了多材料3D打印結構的分辨率和力學性能。結果表明,交替打印的硬和軟材料線條在光學顯微鏡下可清晰分辨至0.25mm(圖4a)。進一步拉伸測試顯示,1:1硬軟比例下,樣品在不同排列方向上與理論模型吻合良好,1mm線寬時實驗彈性模量分別為956MPa(E∥)和2.2MPa(E⊥)(圖4b)。但當線寬減小至0.1mm時,由于紫外光“過固化”效應,模量升高并趨近硬材料水平。通過納米壓痕測試,詳細描繪了軟硬材料界面的梯度變化,發現橫向梯度范圍約200µm,豎直方向上硬材料直接打印在軟材料上時,梯度范圍擴大至250µm,主要因光散射、酸擴散及環氧樹脂放熱固化影響(圖4c)。為模擬自然界如膝蓋、牙齒、烏賊喙等結構中的不同梯度界面,開發了多色灰度DLP打印方法,通過調整UV和紫光的照射強度比例,實現了微米到厘米級的力學梯度可控過渡(圖4d),材料彈性模量跨度達1000倍。這種技術為高精度、多功能的仿生多材料結構制造提供了重要途徑。
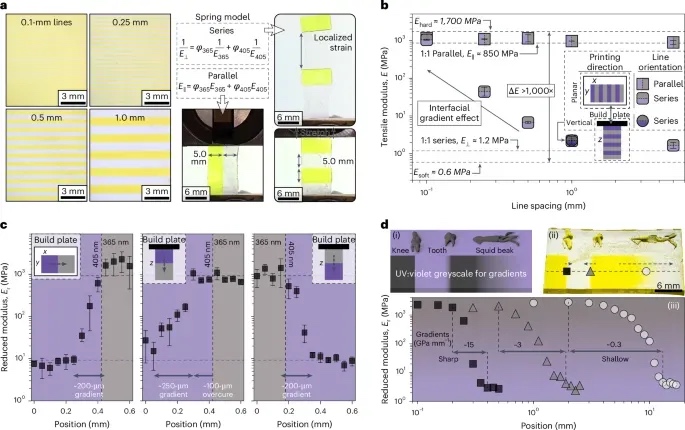
(圖5a) 展示硬彈簧嵌入軟圓柱的結構,螺距從 4 mm 減小至 2 mm 時,50 N 壓縮載荷下應變從 28% 降至 8%,而純軟圓柱應變 44%,純硬彈簧僅 1–2 N 即壓縮 65%,證明通過結構設計調控阻尼。3D 打印膝關節模型(圖5b),股骨、髕骨、脛骨由紫外固化硬材料制成,軟韌帶直徑 0.6 mm,可單向彎曲并彈性恢復,展現仿生運動能力。
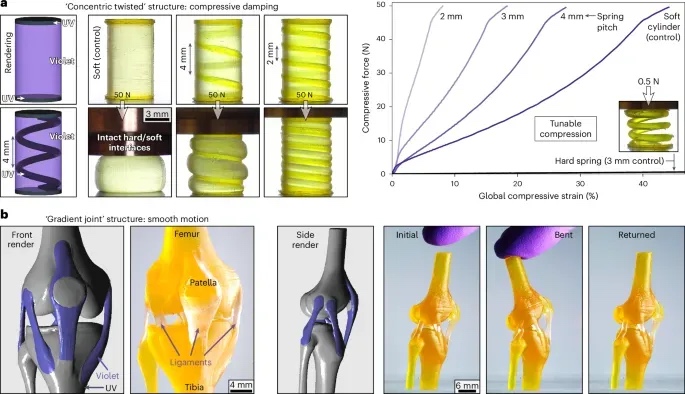
為了驗證該多材料3D打印系統在可拉伸電子器件中的應用潛力,設計了具備超高剛度對比度(ΔE超過1000倍)和高彈性的多材料結構(圖6)。通過有限元分析(FEA)和數字圖像相關技術(DIC),他們測試了中心嵌有不同剛度材料(約1、10、100和1000MPa)的標準拉伸樣條,在整體30%拉伸下的局部應變情況(圖6a)。結果表明,隨著嵌入材料剛度的提高,局部應變顯著降低,FEA預測分別為約4%、0.5%和0.05%,實驗數據與之基本吻合(圖6b,c)。尤其在1000倍剛度對比度下,局部變形遠低于硅材料的斷裂閾值(0.5%),這對于保護可穿戴電子器件非常重要。進一步,作者在不同剛度插入區域表面鍍上金層,并連接LED燈,進行拉伸測試(圖6d)。結果顯示,低剛度(1×)樣品在30%拉伸下斷裂,LED熄滅,而高剛度(1000×)樣品保持完好,LED正常工作。中間剛度(10×和100×)樣品的電阻隨拉伸變化也明顯減小,表明電子穩定性提升。
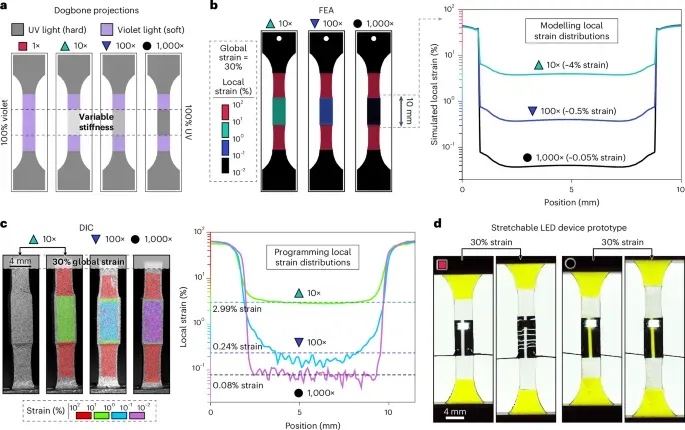
綜上,展示了一種快速、高分辨率、波長選擇性的3D打印方法,可用于制造具有極大力學差異的多材料結構,成功實現了仿生模型與可拉伸電子器件。通過設計高效的環氧-丙烯酸混合樹脂和光引發體系,研究人員實現了高達1.5mm/min的打印速度和約200微米的打印精度,制造出的多材料結構兼具約3000倍的剛度對比度(ΔE)、69MPa的強度、250%以上的拉伸性、90%以上的彈性恢復率以及良好的耐紫外與耐高溫(>100°C)性能。同時,利用多色灰度投影技術,打印出的軟硬過渡界面可精確控制在0.2至10mm范圍內,模擬了自然界中的結構過渡。這一打印技術在軟體機器人、密封件、假肢、可穿戴健康設備以及教育科研中的生物模型等方面具有廣闊應用前景。
原文鏈接https://doi.org/10.1038/s41563-025-02249-z
(責任編輯:admin)