深度:復合式增材制造技術研究現狀及發展
時間:2022-10-12 10:20 來源:深度:復合式增材制造技術研究現 作者:admin 閱讀:次
作者:熊曉晨1,2,3 秦訓鵬1,2,3 華 林1,2,3 胡澤啟1,2,3 紀飛龍1,2,3(1.武漢理工大學現代汽車零部件技術湖北省重點實驗室,2.武漢理工大學汽車零部件技術湖北省協同創新中心, 3.武漢理工大學汽車工程學院)
摘要:形性問題制約金屬增材制造技術的發展與應用,復合式增材制造在解決制件形性問題方面效果顯著。高度概括了復合式增材制造技術分類方式與主體類別;簡要總結了增減材復合制造在制件成形精度和表面質量控制方面的研究進展和技術發展狀況;重點評述了增等材復合制造技術類別、成形原理、制造特征和關鍵問題,以及在制件顯微組織、應力狀態、宏觀性能調控方面的研究現狀和主體結論;系統介紹了超聲、電磁、激光三類特種輔助能場對增材熔池流動、結晶、固態相變的作用機制,以及特種能場作用下,增材層顯微組織狀態、力學性能、成形精度的演化規律;展望了復合式增材制造技術未來的發展趨勢。
金屬增材制造(additive manufacturing,AM)通過對三維數字化模型進行分層切片、逐層疊加,能夠實現復雜形狀、曲面型腔、梯度功能零部件的近凈成形,結合拓撲優化技術,具有無模制造高柔性、短流程、高效率、低成本的特點,目前在航空航天、國防軍工、汽車制造等領域得到廣泛應用。
金屬增材制造過程為多物理場耦合的短時強非平衡冶金過程,增材層顯微組織以尺寸粗大的柱狀晶為主,成形制件內易形成氣孔、夾渣、隔層、裂紋等冶金缺陷,嚴重影響其服役性能[1-5]。同時,增材制造過程中,基體強約束下微熔池快速凝固、非平衡固態相變、沉積層周期性急冷急熱、外部強烈機械約束,使制件內存在復雜的凝縮應力、組織應力、熱應力和機械應力,易造成變形與開裂,成形精度難以有效控制[3-6]。如何實現金屬構件的高性能、高精度增材成形制造是長期以來業界重點研究和解決的問題。
將基于不同原理的制造方法與增材制造技術進行復合,形成兼具兩者優勢的“AM+”復合式增材制造技術,可以有效提高制件的成形精度和性能。復合式增材制造通過引入力、超聲、電磁、激光等輔助能場,作用于增材制造過程和后處理階段,實現對增材制件從顯觀組織、介/宏觀缺陷到宏觀形性的多尺度調控,獲得性能優異、成形精度高的增材制件,是金屬增材制造當前正快速發展的重要方向,也是當前最受學術界關注的先進制造技術之一,中國科學技術協會將“特種能場輔助制造的科學原理”列為2020年十大前沿科學問題之一。
1 復合式增材制造分類
按外加輔助制造方法加工原理分類,復合式增材制造技術可分為三大類:一是與切削加工材料“去除”原理相結合的增減材復合制造技術;二是與軋制、鍛造、噴丸“等量”制造原理相結合的增等材復合制造技術;三是與超聲、電磁、激光等特種能場相結合的特種能場輔助增材制造技術。三大類技術中,外加輔助制造與增材制造存在工序分離式、交叉協同式和同步跟隨式三種復合形式。
2 增減材復合制造技術
2.1 研究現狀
金屬增材制造在零件成形精度和表面質量控制方面存在較大的局限性,難以實現零件的直接高精成形。而基于材料“去除”原理的切削加工在零件成形精度和表面質量控制方面表現優異,且穩定性好。因此,將增材制造與切削加工進行復合,形成增減材復合制造技術,既可以發揮增材制造易構形、易自動化控制、成形效率高、材料利用率高的優勢,又可以利用切削加工成形精度高、表面質量好的特點,可實現金屬零件高效、高精、高性能成形制造。
1994年,MERZ等[7]將熔融沉積成形與數控加工技術進行集成,首次實現了增材、減材制造技術復合,成功制造了用于智能制造系統的308不銹鋼構件,制件成形精度和表面質量大幅度提高。隨后國內外諸多研究機構將不同原理的增材制造技術與銑削加工技術進行復合,開展了從工藝設計、軟件開發到設備研發等多方面的研究工作,成功開發了商品化的增減材復合式制造系統[8-14]。國外以德國德馬吉開發的 LASERTEC65-3D復合加工中心(圖1a)為代表,國內以北京機電院機床有限公司開發的XKR40-Hybrid增減材復合機床為代表(圖1b),采用增減材復合式制造系統成功試制了各類金屬零部件(圖2),零件成形精度和表面質量均得到大幅提高。
增材、減材制造復合的形式有交叉協同式和工序分離式兩種。對于交叉協同式,增材、減材交替進行,能有效減小成形過程中累積的誤差,有利于提高零件的成形精度[11],但熱態下加工,刀具存在軟化傾向,導致磨損加劇,壽命縮短。同時,對于成形精度要求較高的零件,熱態下進行切削加工,動態熱力耦合過程中,工件存在動態變形,需通過后續精加工才能保證零件最終成形精度。工序分離式則是在增材近凈成形的毛坯上進行小余量的切削加工,以得到滿足精度要求的制件。因沉積過程熱積累較大,故冷卻至穩態耗時長,整體成形效率較低。但冷態下切削加工,一次性成形精度較高。圖3所示為等離子沉積與銑削復合成形的金屬花瓶[14],增材、減材協同交叉,成形制件表面粗造度可達2.32 μm,成形精度較高;圖4所示為選擇性激光熔化(SLM)與銑削復合成形的工業模具[13],增材、減材協同交叉,成形模具幾何尺寸精度和表面質量較好,相對密度高達99.2%;圖5所示為電弧增材(WAAM)與銑削復合成形的工業模具[11],增材、減材工序分離,先通過增材獲得近凈成形的毛胚,后經小余量的銑削加工達到零件最終成形精度,相比于傳統數控加工,時間縮短42%,成本降低28%。
2.2 關鍵問題
關于增減材復合制造技術發展與應用,需重點解決以下關鍵問題:①不同增材及銑削復合工藝下,增材層顯觀組織、宏觀形性多尺度演化規律;②增材、減材復合過程中顯觀組織及宏觀形性的協同調控;③增材、減材過程中,動態變形影響下制件成形精度和表面質量的控制;④不同切削介入時機、頻率下制件的成形效率和成形精度的平衡;⑤無冷卻液,高溫、高殘余應力制造過程中刀具的軟化、黏連、磨損和延壽。
摘要:形性問題制約金屬增材制造技術的發展與應用,復合式增材制造在解決制件形性問題方面效果顯著。高度概括了復合式增材制造技術分類方式與主體類別;簡要總結了增減材復合制造在制件成形精度和表面質量控制方面的研究進展和技術發展狀況;重點評述了增等材復合制造技術類別、成形原理、制造特征和關鍵問題,以及在制件顯微組織、應力狀態、宏觀性能調控方面的研究現狀和主體結論;系統介紹了超聲、電磁、激光三類特種輔助能場對增材熔池流動、結晶、固態相變的作用機制,以及特種能場作用下,增材層顯微組織狀態、力學性能、成形精度的演化規律;展望了復合式增材制造技術未來的發展趨勢。
金屬增材制造(additive manufacturing,AM)通過對三維數字化模型進行分層切片、逐層疊加,能夠實現復雜形狀、曲面型腔、梯度功能零部件的近凈成形,結合拓撲優化技術,具有無模制造高柔性、短流程、高效率、低成本的特點,目前在航空航天、國防軍工、汽車制造等領域得到廣泛應用。
金屬增材制造過程為多物理場耦合的短時強非平衡冶金過程,增材層顯微組織以尺寸粗大的柱狀晶為主,成形制件內易形成氣孔、夾渣、隔層、裂紋等冶金缺陷,嚴重影響其服役性能[1-5]。同時,增材制造過程中,基體強約束下微熔池快速凝固、非平衡固態相變、沉積層周期性急冷急熱、外部強烈機械約束,使制件內存在復雜的凝縮應力、組織應力、熱應力和機械應力,易造成變形與開裂,成形精度難以有效控制[3-6]。如何實現金屬構件的高性能、高精度增材成形制造是長期以來業界重點研究和解決的問題。
將基于不同原理的制造方法與增材制造技術進行復合,形成兼具兩者優勢的“AM+”復合式增材制造技術,可以有效提高制件的成形精度和性能。復合式增材制造通過引入力、超聲、電磁、激光等輔助能場,作用于增材制造過程和后處理階段,實現對增材制件從顯觀組織、介/宏觀缺陷到宏觀形性的多尺度調控,獲得性能優異、成形精度高的增材制件,是金屬增材制造當前正快速發展的重要方向,也是當前最受學術界關注的先進制造技術之一,中國科學技術協會將“特種能場輔助制造的科學原理”列為2020年十大前沿科學問題之一。
1 復合式增材制造分類
按外加輔助制造方法加工原理分類,復合式增材制造技術可分為三大類:一是與切削加工材料“去除”原理相結合的增減材復合制造技術;二是與軋制、鍛造、噴丸“等量”制造原理相結合的增等材復合制造技術;三是與超聲、電磁、激光等特種能場相結合的特種能場輔助增材制造技術。三大類技術中,外加輔助制造與增材制造存在工序分離式、交叉協同式和同步跟隨式三種復合形式。
2 增減材復合制造技術
2.1 研究現狀
金屬增材制造在零件成形精度和表面質量控制方面存在較大的局限性,難以實現零件的直接高精成形。而基于材料“去除”原理的切削加工在零件成形精度和表面質量控制方面表現優異,且穩定性好。因此,將增材制造與切削加工進行復合,形成增減材復合制造技術,既可以發揮增材制造易構形、易自動化控制、成形效率高、材料利用率高的優勢,又可以利用切削加工成形精度高、表面質量好的特點,可實現金屬零件高效、高精、高性能成形制造。
1994年,MERZ等[7]將熔融沉積成形與數控加工技術進行集成,首次實現了增材、減材制造技術復合,成功制造了用于智能制造系統的308不銹鋼構件,制件成形精度和表面質量大幅度提高。隨后國內外諸多研究機構將不同原理的增材制造技術與銑削加工技術進行復合,開展了從工藝設計、軟件開發到設備研發等多方面的研究工作,成功開發了商品化的增減材復合式制造系統[8-14]。國外以德國德馬吉開發的 LASERTEC65-3D復合加工中心(圖1a)為代表,國內以北京機電院機床有限公司開發的XKR40-Hybrid增減材復合機床為代表(圖1b),采用增減材復合式制造系統成功試制了各類金屬零部件(圖2),零件成形精度和表面質量均得到大幅提高。
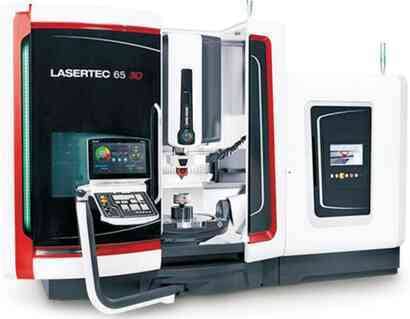
(a)德馬吉LASERTEC65-3D復合加工中心
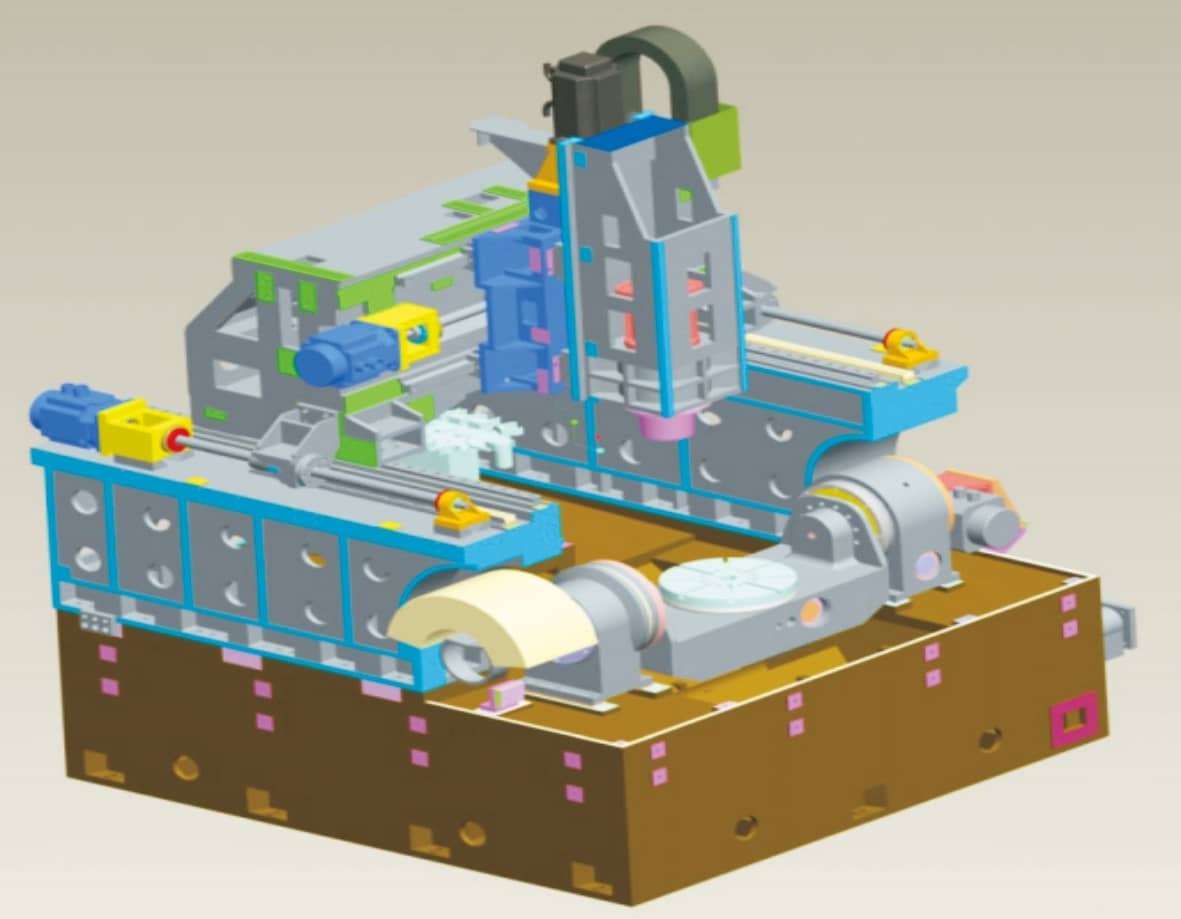
(b)北京機電院XKR40-Hybrid增減材復合機床
圖1 增減材復合加工機床
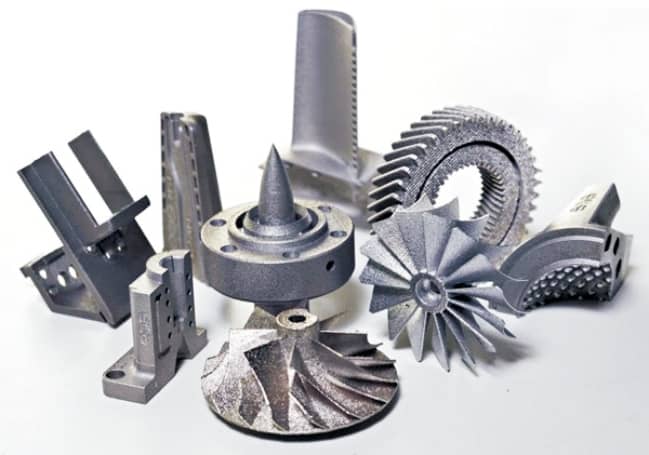
圖2 德馬吉LASERTEC65-3D加工的各類金屬零件
增材、減材制造復合的形式有交叉協同式和工序分離式兩種。對于交叉協同式,增材、減材交替進行,能有效減小成形過程中累積的誤差,有利于提高零件的成形精度[11],但熱態下加工,刀具存在軟化傾向,導致磨損加劇,壽命縮短。同時,對于成形精度要求較高的零件,熱態下進行切削加工,動態熱力耦合過程中,工件存在動態變形,需通過后續精加工才能保證零件最終成形精度。工序分離式則是在增材近凈成形的毛坯上進行小余量的切削加工,以得到滿足精度要求的制件。因沉積過程熱積累較大,故冷卻至穩態耗時長,整體成形效率較低。但冷態下切削加工,一次性成形精度較高。圖3所示為等離子沉積與銑削復合成形的金屬花瓶[14],增材、減材協同交叉,成形制件表面粗造度可達2.32 μm,成形精度較高;圖4所示為選擇性激光熔化(SLM)與銑削復合成形的工業模具[13],增材、減材協同交叉,成形模具幾何尺寸精度和表面質量較好,相對密度高達99.2%;圖5所示為電弧增材(WAAM)與銑削復合成形的工業模具[11],增材、減材工序分離,先通過增材獲得近凈成形的毛胚,后經小余量的銑削加工達到零件最終成形精度,相比于傳統數控加工,時間縮短42%,成本降低28%。
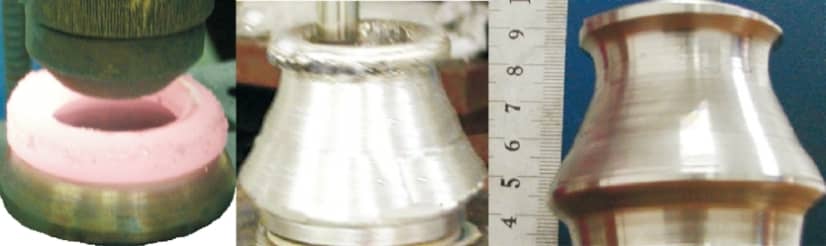
圖3 等離子沉積與銑削復合成形的金屬花瓶[14]
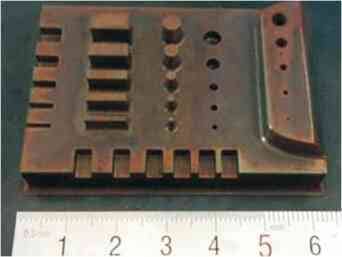
圖4 SLM與銑削復合成形的工業模具[13]
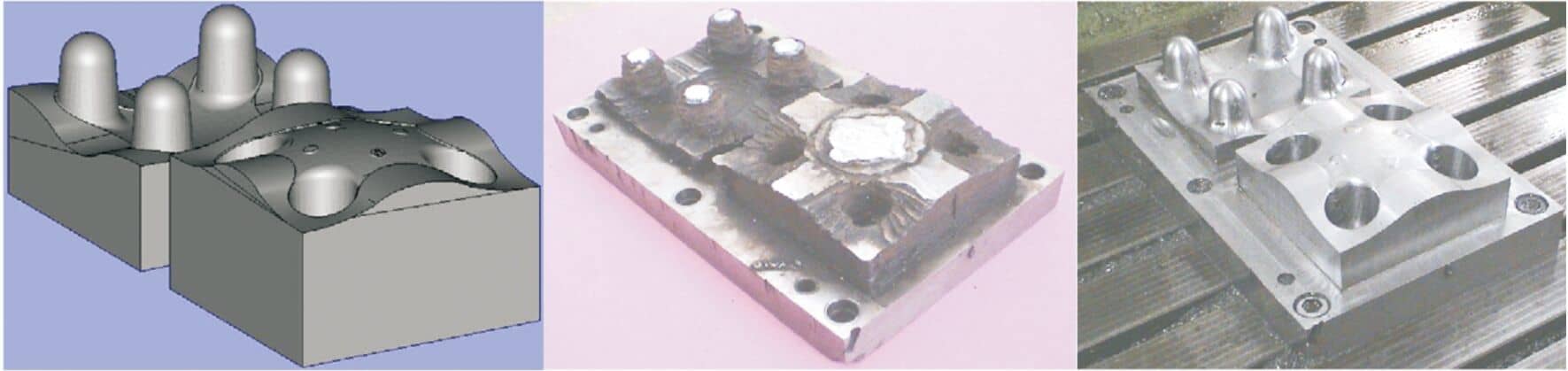
圖5 WAAM與銑削復合成形的工業模具[11]
2.2 關鍵問題
關于增減材復合制造技術發展與應用,需重點解決以下關鍵問題:①不同增材及銑削復合工藝下,增材層顯觀組織、宏觀形性多尺度演化規律;②增材、減材復合過程中顯觀組織及宏觀形性的協同調控;③增材、減材過程中,動態變形影響下制件成形精度和表面質量的控制;④不同切削介入時機、頻率下制件的成形效率和成形精度的平衡;⑤無冷卻液,高溫、高殘余應力制造過程中刀具的軟化、黏連、磨損和延壽。
(責任編輯:admin)
最新內容
熱點內容