深度:復合式增材制造技術研究現狀及發展(2)
時間:2022-10-12 10:20 來源:深度:復合式增材制造技術研究現 作者:admin 閱讀:次
3 增等材復合制造技術
3.1 研究現狀
增減材復合制造能夠有效提高制件成形精度和表面質量,但對制件顯觀組織和宏觀性能的調控效果并不顯著。基于軋制、鍛造、噴丸技術的增等材復合制造技術,在增材過程中或后處理階段,通過引入機械力能場作用于增材層,植入一定深度的塑性變形,改善增材層晶粒形態、顯微組織和應力狀態,可以實現對制件宏觀力學性能的有效控制。
與軋制結合的增等材復合制造是研究最廣泛的復合式增材制造技術。軋制能產生大塑性變形,使增材層內部缺陷被焊合,獲得組織致密、晶粒細化的增材組織,且增材層表面質量較高,后續加工余量較小。現階段存在兩種工藝方法:一是軋制與增材交叉協同的層間冷軋;二是軋制對增材同步跟隨的隨焊熱軋。兩種工藝方法當前均處于實驗研究階段,相關實驗設備均由增材部分和具有特征功能的軋制部分組成,工作時需要大型壓力設備(多為氣壓或液壓設備)產生高達數十千牛的恒定軋制力[15],促使增材層發生連續均勻的塑性變形。
文獻[16-17]采用層間冷軋工藝(原理如圖6所示),分別對低碳鋼、純鉭增材制件進行逐層軋制處理,通過層間冷軋在沉積層上形成了一層具有一定深度的塑性變形層,變形層在后續沉積層反復熱循環作用下發生再結晶,沉積層晶粒發生細化,得到了隨機織構的各向同性材料組織(圖7);文獻[18]開發了一種新型異形軋輥(圖8),該軋輥對具有寬壁和交叉特征的增材層晶粒細化效果顯著;文獻[19-22]對Ti-6Al-4V鈦合金開展了類似的研究,除了上述結論之外,還發現低塑性應變下β晶組織細化和織構產生的原因可能是,變形層在快速重復加熱時隨β晶的長大產生了退火孿晶,如圖9所示。
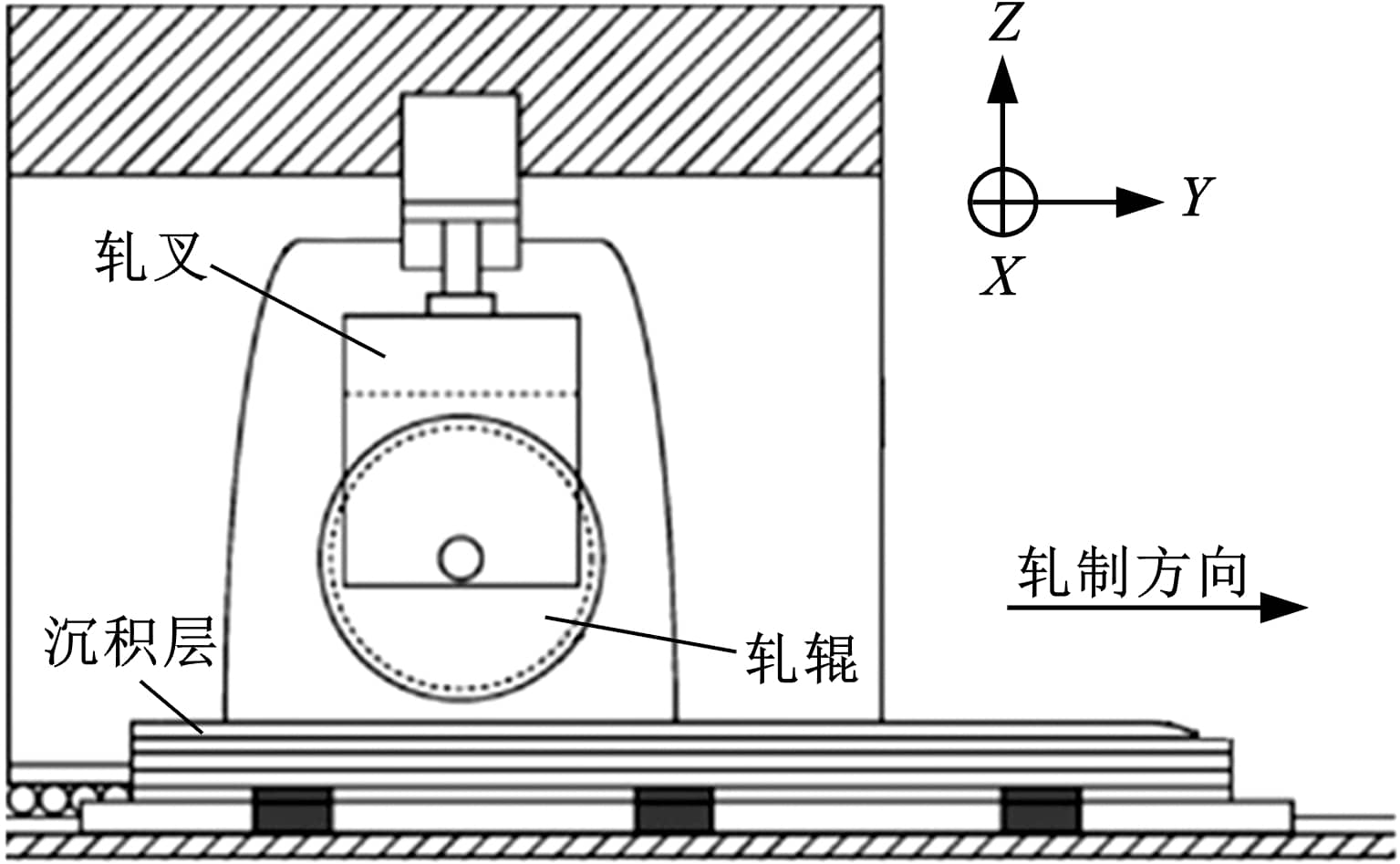
圖6 層間冷軋工藝原理圖[16]
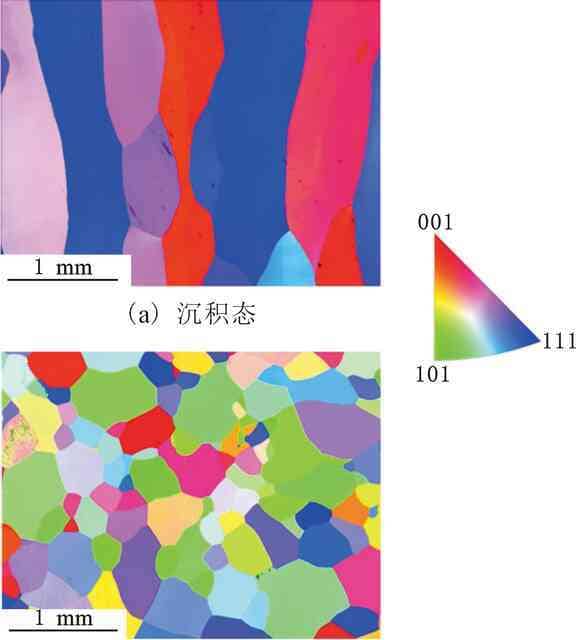
(b)層間冷軋工藝
圖7 沉積態與層間冷軋工藝晶粒形態及取向[17]
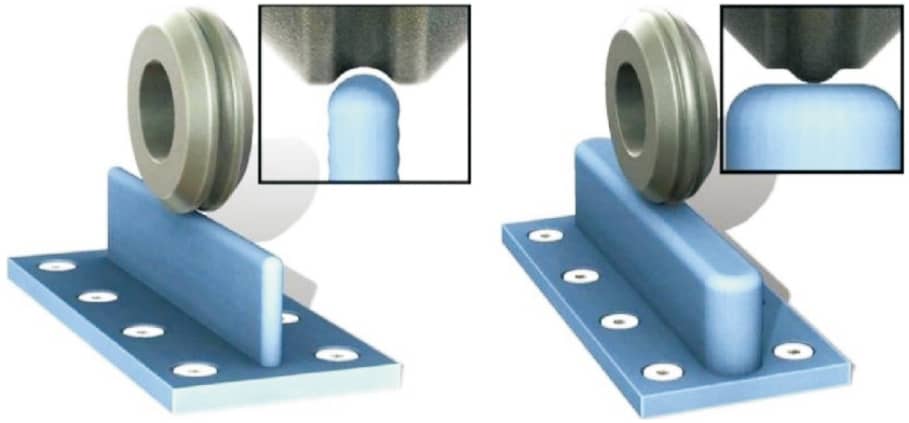
(a)薄壁用軋輥 (b)寬壁和交叉特征用軋輥
圖8 新型異形軋輥[18]
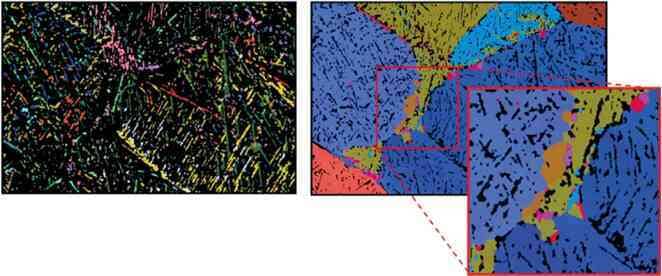
圖9 Ti-6Al-4V β晶的長大產生退火孿晶界[19]
文獻[23-25]采用層間冷軋工藝處理鋁合金增材制件,發現層間冷軋工藝可使增材層內部微小氣孔發生閉合,組織更加致密,強度大幅提高,而塑性卻未受損。層間冷軋對增材層的強化機制,除了形變強化、細晶強化之外,合金元素還在塑性變形驅動下發生固溶強化。文獻[26]也發現軋制塑性變形能促進合金元素固溶于增材基體,基體隨時間發生自然時效使得強度和硬度大幅提高。除此之外,還發現側向冷軋對鋁合金增材層殘余應力的控制效果較垂向冷軋更好,能夠有效地控制殘余變形。
ZHANG等[27-28]開發了一種基于新型微軋輥的同步跟隨復合增材制造技術(HDMR),微軋輥跟隨熔池對增材層進行同步熱軋(圖10),軋制介入的溫度可通過調節軋輥對焊槍的跟隨距離來改變,通過在奧氏體未再結晶溫度區控軋提高了材料結晶度,獲得了平均晶粒尺寸為7 μm的細晶組織,制件各力學指標大幅提高(圖11)。
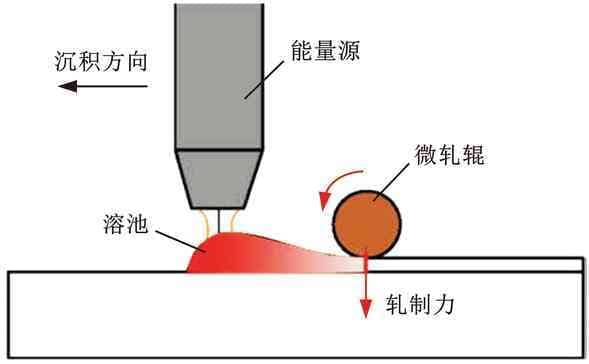
圖10 HDMR原理圖[27]
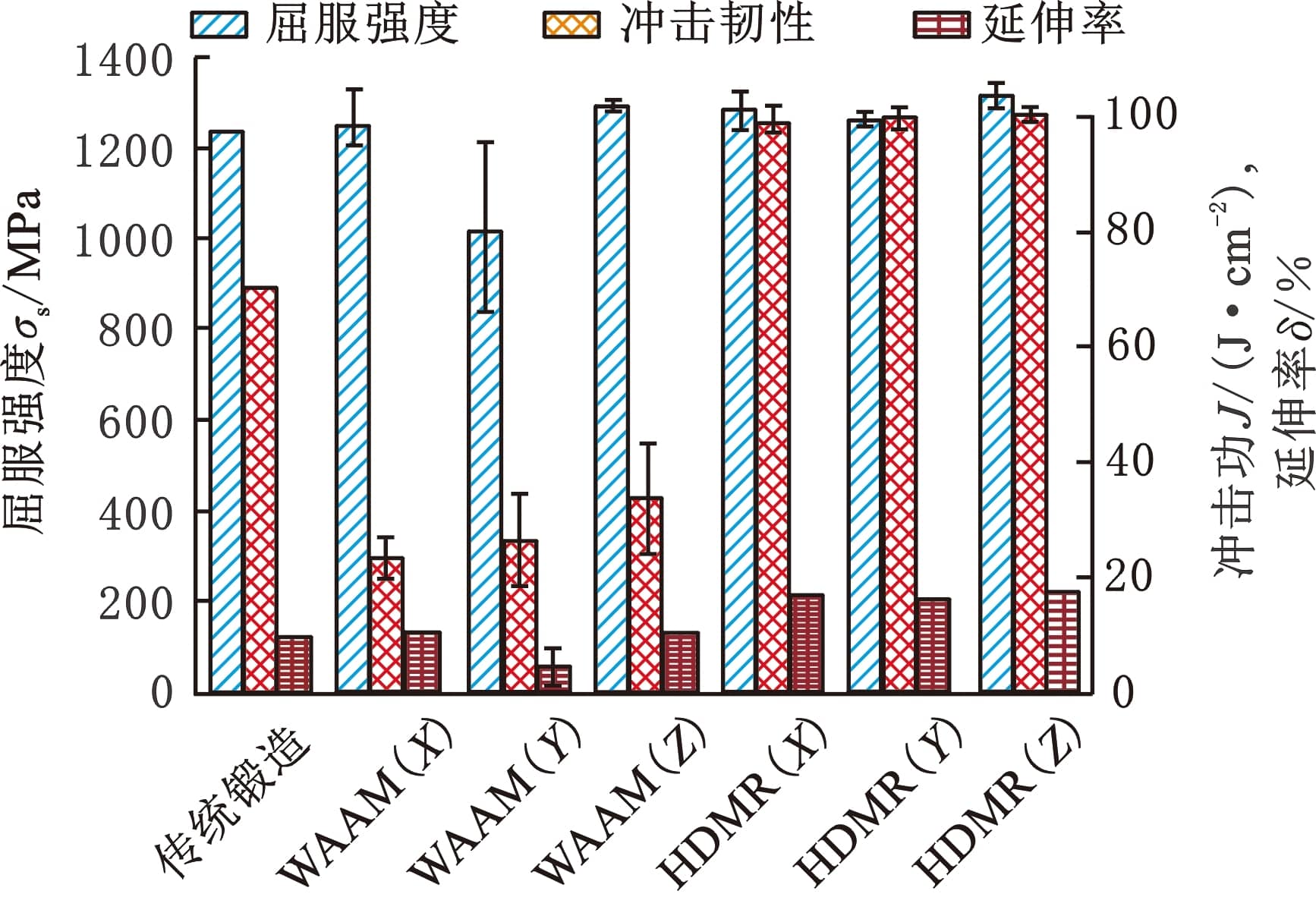
圖11 隨焊熱軋工藝下增材層各向力學性能[28]
與鍛造技術結合的增等材復合制造將效率高、組織性能優異的鍛造成形與高柔性的增材制造進行復合,發揮兩者優勢,可實現復雜結構和高性能制件的近凈成形。當前存在兩種復合類型,即與模鍛成形整體鍛造復合型和與機械錘擊局部鍛造復合型。
與模鍛成形整體鍛造結合的增等材復合制造多為工序分離式。MEINERS等[29]在預成形的鍛件上通過粉末激光金屬沉積(P-LMD)和電弧增材(WAAM)兩種AM技術成功添加了新的結構特征(圖12),既保證了制造效率又提高了制造柔性,對比傳統鍛造,材料利用率提高了50%。
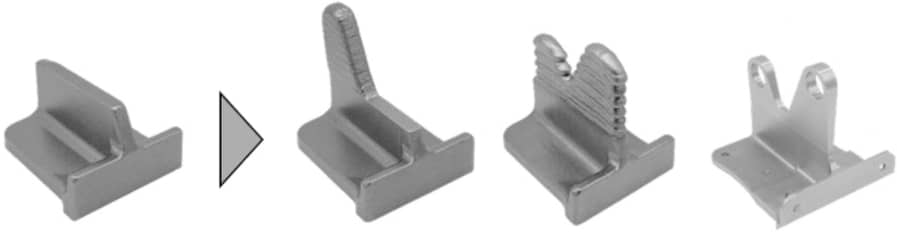
圖12 預成形T形截面鍛件通過P-LMD和WAAM增加特征加強筋[29]
BAMBACH等[30]在Ti-6Al-4V預成形的鍛件上進行WAAM制造,對WAAM制件進行熱鍛成形,分別研究了兩種復合制造工藝下顯觀組織、力學性能演化規律,結果表明增材區與鍛造區界面冶金結合良好,鍵合區拉伸性能可達到鍛造要求,延展性略低于鍛件,但較鑄件要高;MA等[31]對Ti-6Al-4V鍛造和增材鍵合區顯觀組織和力學性能的研究發現,鍵合區因形成二次強化相而整體強度較基體要好,該結論與文獻[30]結論一致。同時,還發現對WAAM制件進行熱鍛和后續熱處理后,制件強度、延伸率等力學性能指標均出現了較大程度的提高,整體性能與鍛件相當(圖13)。
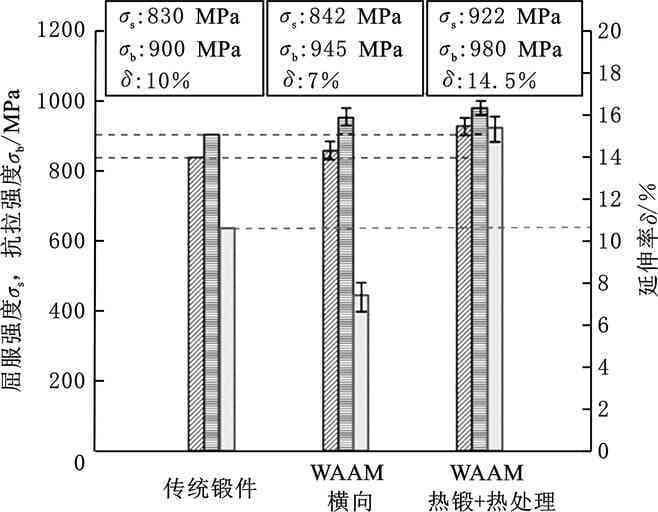
圖13 WAAM制件熱鍛+熱處理工藝與沉積態、傳統鍛件力學性能對比[30]
文獻[32-33]研究了不同激光增材工藝和熱鍛成形工藝對不銹鋼成形件顯觀組織和力學性能的影響,增材后進行高溫熱鍛,制件孔隙率明顯降低,致密度可達99%以上,晶粒尺寸大幅減小,晶粒細化程度超7倍(圖14),增材層力學性能顯著提高。

(a)沉積態 (b)900 ℃變形量5% (c)1040 ℃變形量5% (d)900 ℃變形量30% (e)1040 ℃變形量30%

圖14 不同增材與熱鍛工藝下增材層晶粒形態變化[33]
與機械錘擊局部鍛造結合的增等材復合制造,當前研究報道較少,均采用交叉協同的方式與高效、低廉的電弧增材制造進行復合。錘擊錘頭尺寸較小,與工件的接觸方式為點接觸或微型球面接觸,相比于軋制工藝的線接觸或柱面接觸,具有更高的自由度,加工時受工件形狀的限制較小。另外,錘擊對工件的作用為非連續性多次間斷沖擊,作用力為瞬間沖擊力,作用時間極短,瞬間接觸力較大,通過多道次小塑性變形積累,最終可使增材層產生較大的塑性變形,無需大型設備提供高達數十千牛的持續靜壓力,能夠和承載能力有限的工業機器人結合獲得更高的加工自由度,可滿足復雜形狀零件的加工,但現階段錘擊變形量難以實現精確控制,成形精度較軋制復合式增材制造要低。
HÖNNIGE等[15,34-35]采用六自由度ABB工業機器人運載高精度氣動錘擊設備構成其錘擊組件,采用層間冷錘工藝在Ti-6Al-4V增材層表層植入微量塑性變形,伴隨后續沉積層熱循環獲得了大于塑性變形深度的細晶區,力學性能有所提高(圖15);XIONG等[36]采用相似的方式,利用多自由度安川機器人手臂運載改良的電動錘擊裝置(圖16),通過對兩機器人進行協同控制,控制錘頭與焊槍的工作位姿,可實現微形錘頭對焊槍的同步近距離跟隨,在接近材料再結晶溫度時進行隨動低頻錘擊,使增材層表層發生一定程度的塑性變形,產生高密度位錯,在增材層表層形成一定比例的亞結構,平均晶粒尺寸減小,增材層整體強度得到了較大程度的提高;FANG等[37]采用三自由度運載機構運載氣動錘擊裝置(圖17),對2319鋁合金增材層在焊后冷卻至50 ℃時進行層間錘擊,增材層晶粒細化明顯,相較于沉積態,晶粒尺寸減小至其1/10(圖18),伴隨著高密度的位錯,增材層力學性能大幅度提高;權國政等[38]采用的錘擊組件由大型龍門機器人(原理與文獻[37]類似)運載氣動錘擊設備構成,該運載機器人體形大,承載能力強,穩定性好,但也存在著運動自由度較少,易與焊槍發生近距離干涉等問題。所采用的錘擊設備為工程用氣鎬,成本低廉,沖擊力大,但錘擊運動難以準確控制,成形精度較低。該研究通過仿真與實驗結合的方式發現,焊后錘擊對消除焊接內應力效果顯著。
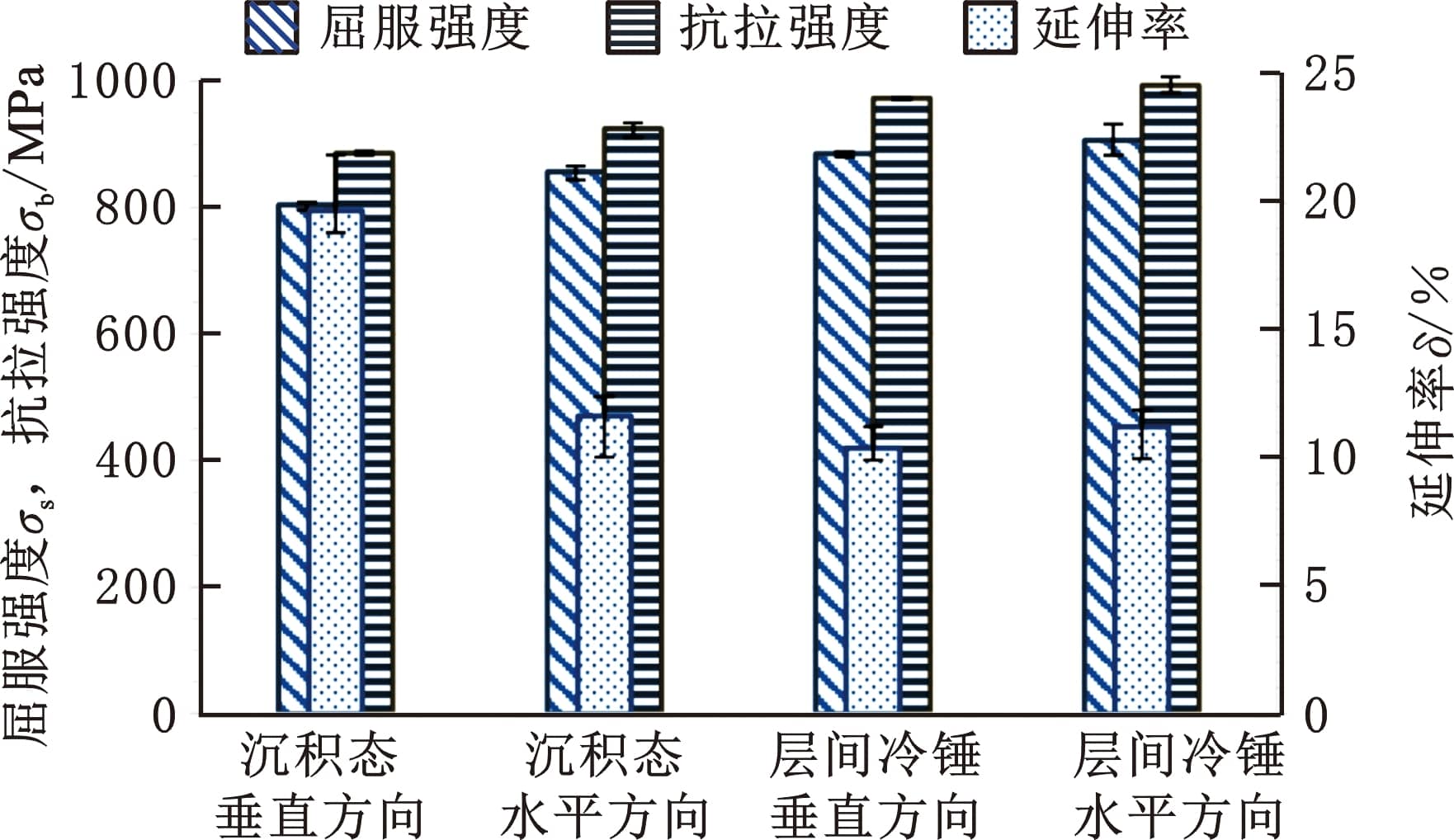
圖15 層間冷錘工藝與沉積態力學性能對比[34]
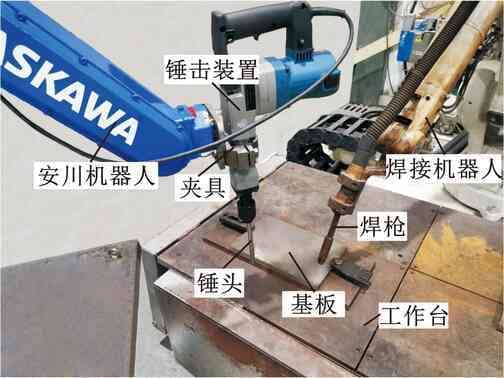
圖16 機器人手臂運載電動錘擊裝置[36]
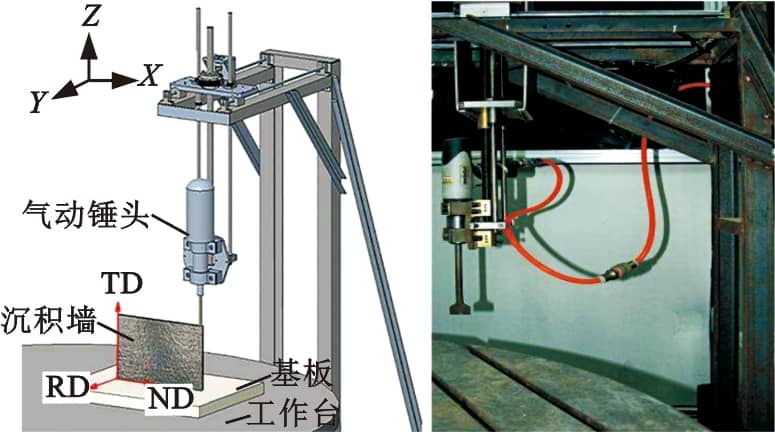
圖17 三自由度機械錘擊組件[37]
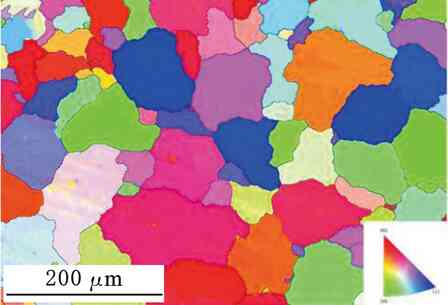
(a)沉積態
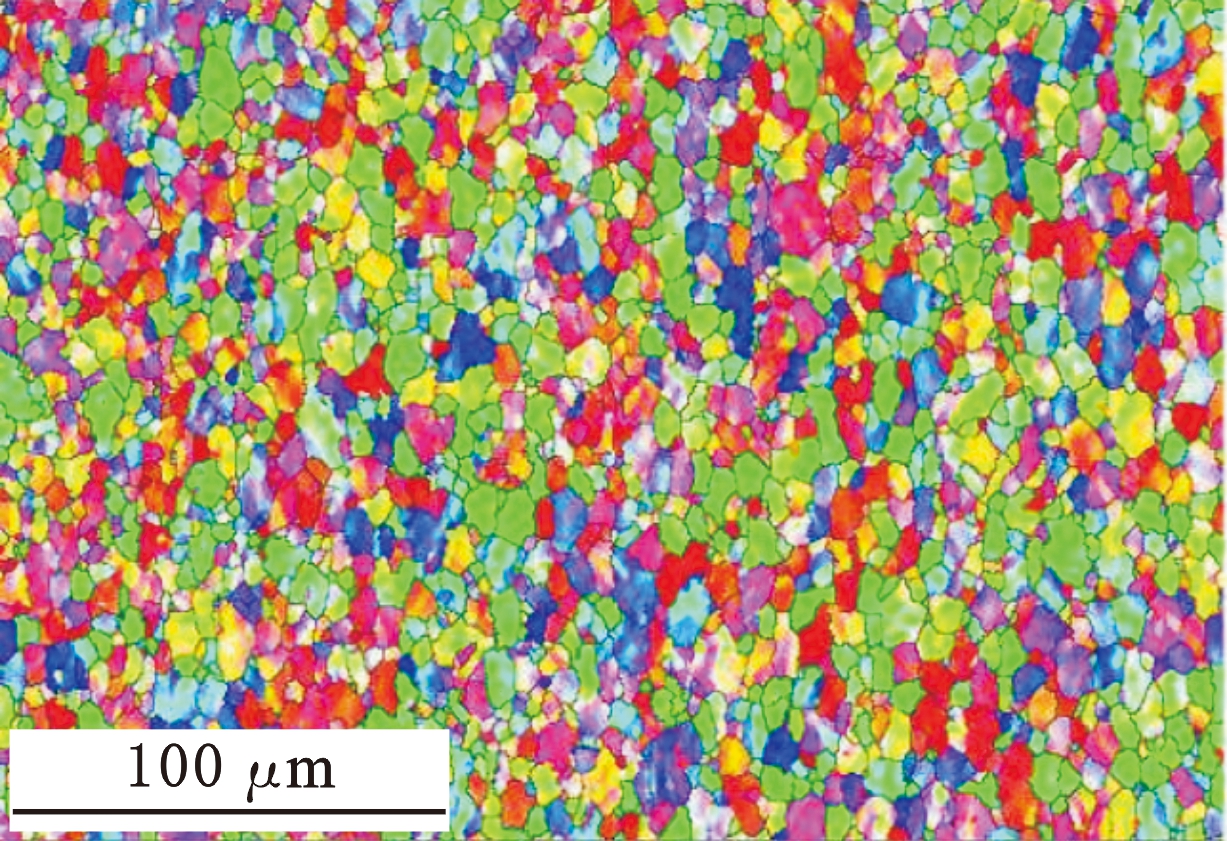
(b)層間冷錘工藝
圖18 沉積態與層間冷錘工藝晶粒形態[37]
Fig.18 Grain morphologies of as-deposited and inter-layer cold hammering[37]
(責任編輯:admin)
最新內容
熱點內容