粉末床熔融金屬增材制造中的缺陷和異常
時間:2023-01-06 11:03 來源:長三角G60激光聯盟 作者:admin 閱讀:次
金屬增材制造是一種顛覆性技術,正在徹底改變制造業。盡管該技術在直接制造具有復雜幾何形狀的金屬零件方面具有無與倫比的能力,但該技術的廣泛實現目前受到微觀結構缺陷和異常的限制,這可能會顯著降低產品的結構完整性和服務性能。準確檢測、表征和預測這些缺陷和異常對制造完全密集和無缺陷的構建具有重要而直接的影響。本文旨在闡明粉末床熔融增材制造過程中常見的缺陷/異常及其形成機制。它們可能來自原材料,加工條件和后處理。雖然激光焊接中的缺陷/異常已經被廣泛研究,但它們的形成和演變仍然不清楚。此外,粉末床熔融技術中存在粉末可能會產生新型缺陷,例如,孔隙率從粉末轉移到建筑物中。減輕缺陷的實用策略也通過對其形成的基本了解來解決。這種探索可以驗證和校準模型,并簡化過程鑒定,而無需昂貴的試錯實驗。
1. 簡介和背景
金屬增材制造
金屬增材制造(AM,也稱為3D打印)是一系列技術,由三個主要生產過程組成,即粉末床,粉末進料和送絲。這些工藝的不同之處在于其鋪展或分層材料的方式以及熔合或粘合原料的方式。與傳統制造相比,金屬增材制造具有許多卓越的能力,包括縮短設計到上市的周期,更低的能耗,以及將組件整合到具有復雜幾何形狀的單元零件中的能力。還有制造非標準微觀結構的能力,有可能定制局部性質。
在基于聚變的AM(例如,激光粉末床熔融)中,使用熱源(例如,激光)來熔合材料,并且該過程背后的基礎知識是關于熔化和凝固的。相比之下,使用高能量密度光束(如激光)的焊接冶金已經被廣泛研究了幾十年。因此,一個直觀的想法是從現有的知識體系中學習,并在理解金屬AM中微觀結構和缺陷的形成和演變時應用它。盡管它們的相似性如何,但值得注意的是,一些可焊接合金(例如,AA6061)不容易通過熔接基AM工藝加工,因為在AM加工過程中收縮應力和大凝固范圍的組合會產生開裂。因此,需要高溫預熱等技術解決方案。
對于許多材料而言,靜態機械性能主要由微觀結構特征決定,并且在內部空隙的存在下相對堅固,但材料的疲勞和斷裂行為會因缺陷的存在而顯著降低。材料空隙在零件加載時充當應力集中位點,有助于在循環加載期間加速裂紋成核和擴展,并限制AM在疲勞受限應用中的使用。正如Seifi等人所指出的,減少增材制造系統中的可變性是增材制造組件的認證和在工業中成功采用該技術的關鍵。雖然對于任何制造方法來說,完全消除加工缺陷是不可能的,但了解其來源是提高增材制造部件的可靠性和可重復性的重要一步。
本綜述旨在詳細總結金屬粉末床熔融AM缺陷的表征和緩解技術,以限制其發生。這里的金屬包括鎳基、鈦基、鋁基和鐵基合金。我們依次描述粉末床熔融AM工藝,表征工具(原位和非原位),粉末相關,工藝相關和加工后相關缺陷,緩解技術,可能的預測標準以及機械和腐蝕性能。我們進行本綜述的目的是確定已發表文獻中的差距和研究需求,從而提高我們對金屬AM工藝的理解并指導AM機器的操作。
1.2. 粉末床熔融AM技術的分類
粉末床熔融(PBF)技術目前在金屬增材制造中提供了最佳的再現性和尺寸精度,因此在工業界和學術界都得到了很好的研究。通常,PBF技術利用以下步驟來制造零件:(1)將指定厚度的金屬粉末層鋪展到機器的構建板上;(2)使用激光或電子束熱源選擇性地將粉末層內的所需區域熔化在一起;(3)構建板向下移動,并在構建板上鋪上一層新的粉末;(4)逐層重復此過程,直到零件完成。PBF工藝已用于各行各業的眾多應用,例如醫療(定制的骨科組件和來自鈦,不銹鋼和鈷鉻合金生物材料的植入物),航空航天和國防(燃料噴嘴,支架,渦輪葉片,發動機部件和結構構件)和能源(熱交換器和渦輪機翼型)。
根據ISO/ASTM52900標準[18]的規定,PBF被定義為一種增材制造工藝,其中熱能選擇性地熔合粉末床的區域。屬于這一類別的工藝包括電子束熔化(EBM),選擇性激光熔化/燒結(SLM / SLS),最近被描述為直接金屬激光熔化(DMLM)或直接金屬激光燒結(DMLS)。ASTM為增材制造技術定義了以下術語:
•用于直接激光沉積→激光束定向能量沉積(L-DED);
•用于選擇性激光熔化、激光粉末床熔融等→激光束粉末床熔融(L-PBF);
•用于電子束技術,如粉末進料或粉末床→分別為 E-DED 和 E-PBF。
1.2.1. 激光束粉末床熔融
L-PBF(又名選擇性激光熔化)使用激光作為逐層制造零件的主要工具。它能夠生產一系列金屬合金的零件,包括鋁,鈦,鐵和鎳基高溫合金。
圖1總結了L-PBF AM的分步過程方法。一旦整個部件被打印出來,多余的粉末就會被移除(并且經常被回收),然后從構建室中卸載構建板。由于打印部件熔合到構建板上,因此需要機械拆卸。在移除之前,零件通常留在構建板上并進行應力消除熱處理,以最大限度地減少殘余應力,消除翹曲并保持尺寸精度。
L-PBF技術填補了需要快速原型制作或小批量生產的行業的利基市場。該工藝固有的增材性質允許打印復雜的晶格結構(圖2a)和具有復雜內部幾何形狀的部件,如GE燃料噴嘴(圖2b)。此外,它允許零件加固和幾何優化,以減輕重量,例如座椅支架(圖2c)。
金屬零件的L-PBF近年來已基本發展。除了越來越多的商用機器外,還進行了大量研究以改進該技術。主要挑戰之一,特別是在疲勞是一個問題的應用中,是構建內部形成的缺陷。了解制造過程和缺陷形成是構建高質量零件的關鍵。
通常,缺陷可以通過三種特定方式產生或轉移到成品零件上,即通過:(1)從原料粉末轉移,(2)熔化過程中的激光 - 粉末 - 金屬相互作用,以及(3)后處理。總體而言,在LPBF中觀察到四種不同類型的缺陷,即:熔合孔隙率不足,鎖孔孔隙率,球化和氣體孔隙率。為了限制金屬增材制造過程中的缺陷產生,必須通過適當選擇加工參數來考慮和控制孔隙形成或轉移的所有三種機制。其中,激光-粉末-金屬相互作用是金屬AM加工過程中最常見的孔隙率轉移手段,其中通常可以觀察到諸如“鎖孔”和“無融合”(LOF)孔隙率等缺陷。
更詳細地說,熔池之間是否有足夠的重疊來確保所有點至少熔化一次,從而確定熔融孔隙度邊界的缺乏。LOF孔隙率最近也被證明是由于噴射的顆粒/飛濺物與激光和熔池的相互作用而形成的。在激光掃描過程中,大的飛濺物可能無法完全熔化,因此成為潛在的孔隙生成位點。相反,鎖孔孔隙度邊界對應于深鎖孔中的不穩定性,導致孔隙被擠壓。第三個邊界(稱為“串珠”邊界)由流體流動模式和熔池毛細管不穩定性的組合決定,并且是LPBF AM系統中保持精度(例如,同時增加速度和功率)的同時提高生產率的限制因素。全密度可以量化為具有>99.9%體積密度的樣品,但應該注意的是,仍然存在較大的缺陷。其目的是優化加工參數,減少LPBF AM材料中不需要的缺陷,并最終證明在由缺陷含量定義的工藝窗口中操作LPBF機器是可行的。
關于工藝參數對微觀結構、孔隙度水平和缺陷形成的影響的研究很多。有影響力的工藝參數包括(1)激光相關參數(例如,激光功率、光斑尺寸、脈沖持續時間和脈沖頻率),(2)掃描相關參數(例如,掃描速度或速度、掃描間距或出雛、掃描旋轉和掃描圖案),(3)粉末相關參數(例如,粉末形態、粒度和分布、層厚度、加樣和材料特性)和(4)宏觀參數(例如,粉末床溫度及其均勻性、氣體流量、氣體類型、吊具桿類型)。除了P-V-H-L處理組合外,掃描策略(圖3)在PBF工藝中的缺陷形成中起著至關重要的作用。掃描策略影響傳熱、粉末熔體形成和凝固速率,影響缺陷的類型、位置和分布以及晶粒形態。因此,優化工藝參數、熱源功率、掃描速度和策略以最大限度地減少工藝引起的孔隙率至關重要。
在激光粉末床熔融過程中以及隨后的粉末擴散過程中,由許多粉末特性控制,激光選擇性地掃描粉末層的表面,以按照相應層中的STL輸入文件熔化和熔化金屬粉末。復雜的激光物質相互作用導致許多現象,這些現象可能導致最終部件的缺陷。常見缺陷包括球化/珠狀、無熔合、鎖孔孔隙率、熔融金屬或粉末顆粒飛濺物噴出、周圍基材剝蝕或微觀結構缺陷。許多研究都集中在可視化和分析此類異常的實驗方法上。然而,在其形成中起主要作用的一個重要方面是激光與物質的相互作用。
選擇性激光熔化可以從松散的粉末中制造出不僅具有與傳統制造的組件相似的物理形狀,而且還具有相似的性能。此外,SLM可以生產復雜的零件,如果用傳統技術制造,則需要一系列制造過程,消耗多余的材料(即浪費),時間和精力。在某些情況下,甚至可以使用SLM制造任何傳統制造方法都無法實現的零件。SLM的方法是選擇性地掃描粉末床,從而熔化粉末以逐層構建組件。在SLM中,組件構建在底板上,激光束穿過x-y平面中的每個層。在每層之后降低活塞,以允許后續粉末層沉積。該過程連續重復,直到部件完成。SLM過程消耗的時間可分為主時間和輔助時間。主要時間是熔化粉末層所需的時間,而輔助時間是基底降低和粉末沉積。
1. 簡介和背景
金屬增材制造
金屬增材制造(AM,也稱為3D打印)是一系列技術,由三個主要生產過程組成,即粉末床,粉末進料和送絲。這些工藝的不同之處在于其鋪展或分層材料的方式以及熔合或粘合原料的方式。與傳統制造相比,金屬增材制造具有許多卓越的能力,包括縮短設計到上市的周期,更低的能耗,以及將組件整合到具有復雜幾何形狀的單元零件中的能力。還有制造非標準微觀結構的能力,有可能定制局部性質。
在基于聚變的AM(例如,激光粉末床熔融)中,使用熱源(例如,激光)來熔合材料,并且該過程背后的基礎知識是關于熔化和凝固的。相比之下,使用高能量密度光束(如激光)的焊接冶金已經被廣泛研究了幾十年。因此,一個直觀的想法是從現有的知識體系中學習,并在理解金屬AM中微觀結構和缺陷的形成和演變時應用它。盡管它們的相似性如何,但值得注意的是,一些可焊接合金(例如,AA6061)不容易通過熔接基AM工藝加工,因為在AM加工過程中收縮應力和大凝固范圍的組合會產生開裂。因此,需要高溫預熱等技術解決方案。
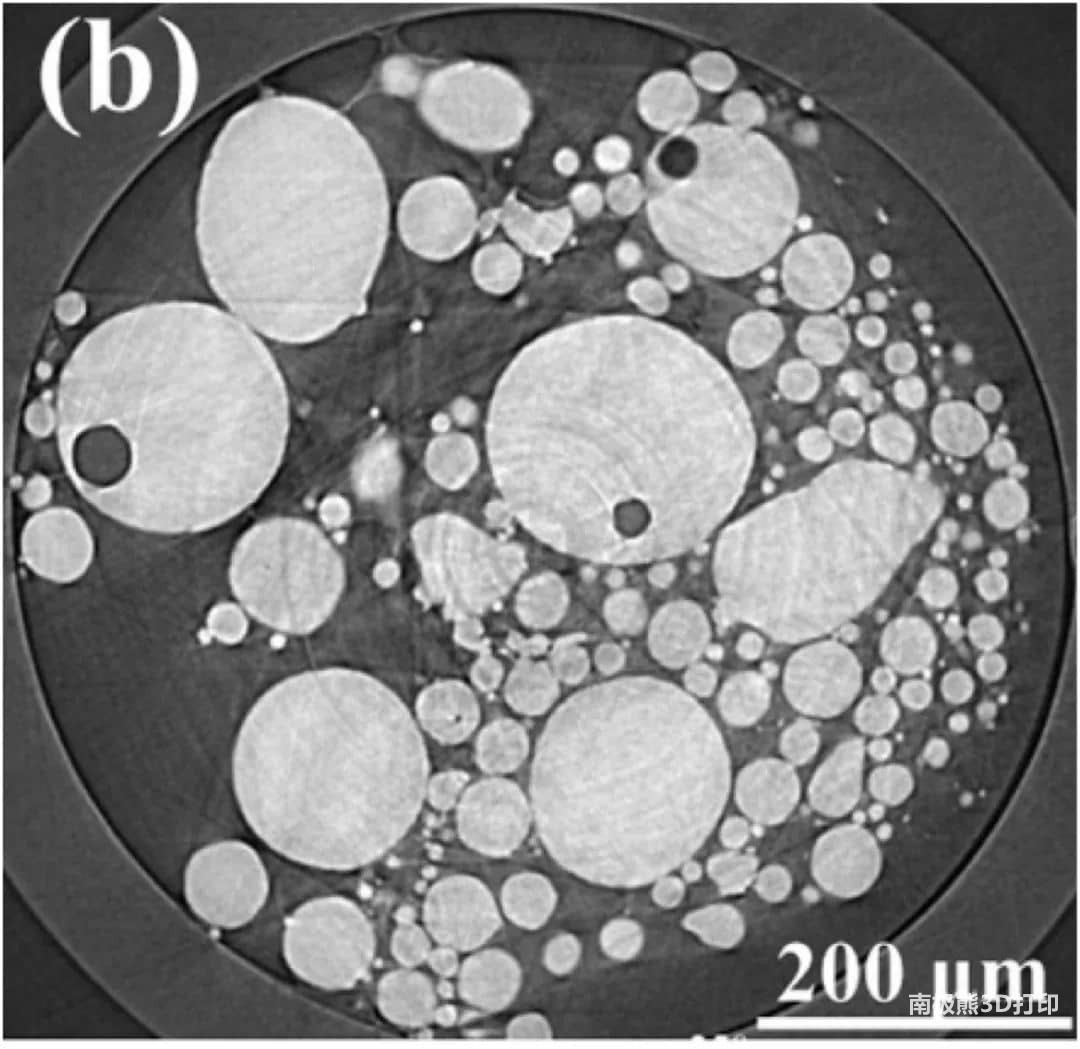
Ti-6Al-4V粉末的X射線計算機斷層掃描顯示原料內捕獲的氣體孔隙率。
對于許多材料而言,靜態機械性能主要由微觀結構特征決定,并且在內部空隙的存在下相對堅固,但材料的疲勞和斷裂行為會因缺陷的存在而顯著降低。材料空隙在零件加載時充當應力集中位點,有助于在循環加載期間加速裂紋成核和擴展,并限制AM在疲勞受限應用中的使用。正如Seifi等人所指出的,減少增材制造系統中的可變性是增材制造組件的認證和在工業中成功采用該技術的關鍵。雖然對于任何制造方法來說,完全消除加工缺陷是不可能的,但了解其來源是提高增材制造部件的可靠性和可重復性的重要一步。
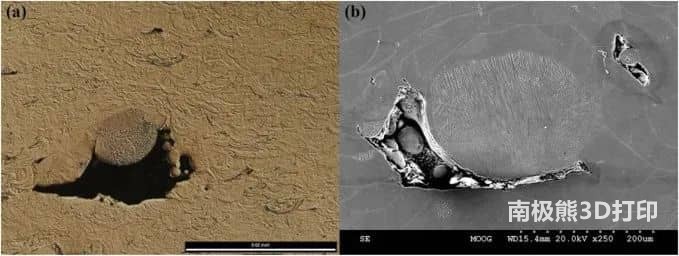
具有優化加工參數的增材CoCrMo合金中存在的無熔合缺陷的例子。
本綜述旨在詳細總結金屬粉末床熔融AM缺陷的表征和緩解技術,以限制其發生。這里的金屬包括鎳基、鈦基、鋁基和鐵基合金。我們依次描述粉末床熔融AM工藝,表征工具(原位和非原位),粉末相關,工藝相關和加工后相關缺陷,緩解技術,可能的預測標準以及機械和腐蝕性能。我們進行本綜述的目的是確定已發表文獻中的差距和研究需求,從而提高我們對金屬AM工藝的理解并指導AM機器的操作。
1.2. 粉末床熔融AM技術的分類
粉末床熔融(PBF)技術目前在金屬增材制造中提供了最佳的再現性和尺寸精度,因此在工業界和學術界都得到了很好的研究。通常,PBF技術利用以下步驟來制造零件:(1)將指定厚度的金屬粉末層鋪展到機器的構建板上;(2)使用激光或電子束熱源選擇性地將粉末層內的所需區域熔化在一起;(3)構建板向下移動,并在構建板上鋪上一層新的粉末;(4)逐層重復此過程,直到零件完成。PBF工藝已用于各行各業的眾多應用,例如醫療(定制的骨科組件和來自鈦,不銹鋼和鈷鉻合金生物材料的植入物),航空航天和國防(燃料噴嘴,支架,渦輪葉片,發動機部件和結構構件)和能源(熱交換器和渦輪機翼型)。

用于構造用于機器學習的coupons的構建板的配置。
根據ISO/ASTM52900標準[18]的規定,PBF被定義為一種增材制造工藝,其中熱能選擇性地熔合粉末床的區域。屬于這一類別的工藝包括電子束熔化(EBM),選擇性激光熔化/燒結(SLM / SLS),最近被描述為直接金屬激光熔化(DMLM)或直接金屬激光燒結(DMLS)。ASTM為增材制造技術定義了以下術語:
•用于直接激光沉積→激光束定向能量沉積(L-DED);
•用于選擇性激光熔化、激光粉末床熔融等→激光束粉末床熔融(L-PBF);
•用于電子束技術,如粉末進料或粉末床→分別為 E-DED 和 E-PBF。
1.2.1. 激光束粉末床熔融
L-PBF(又名選擇性激光熔化)使用激光作為逐層制造零件的主要工具。它能夠生產一系列金屬合金的零件,包括鋁,鈦,鐵和鎳基高溫合金。
圖1總結了L-PBF AM的分步過程方法。一旦整個部件被打印出來,多余的粉末就會被移除(并且經常被回收),然后從構建室中卸載構建板。由于打印部件熔合到構建板上,因此需要機械拆卸。在移除之前,零件通常留在構建板上并進行應力消除熱處理,以最大限度地減少殘余應力,消除翹曲并保持尺寸精度。
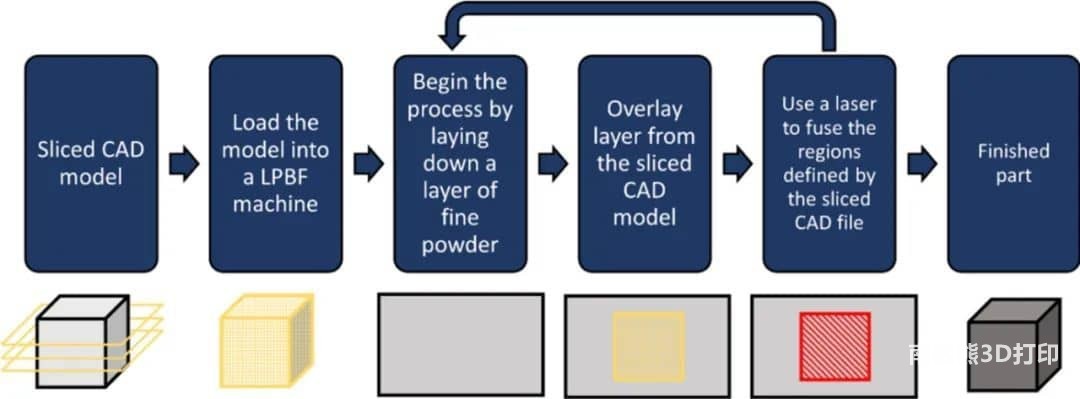
圖 1 L-PBF 計算機的一般構建方法。矩形灰色圖紙表示L-PBF工藝過程中的粉末床。
L-PBF技術填補了需要快速原型制作或小批量生產的行業的利基市場。該工藝固有的增材性質允許打印復雜的晶格結構(圖2a)和具有復雜內部幾何形狀的部件,如GE燃料噴嘴(圖2b)。此外,它允許零件加固和幾何優化,以減輕重量,例如座椅支架(圖2c)。
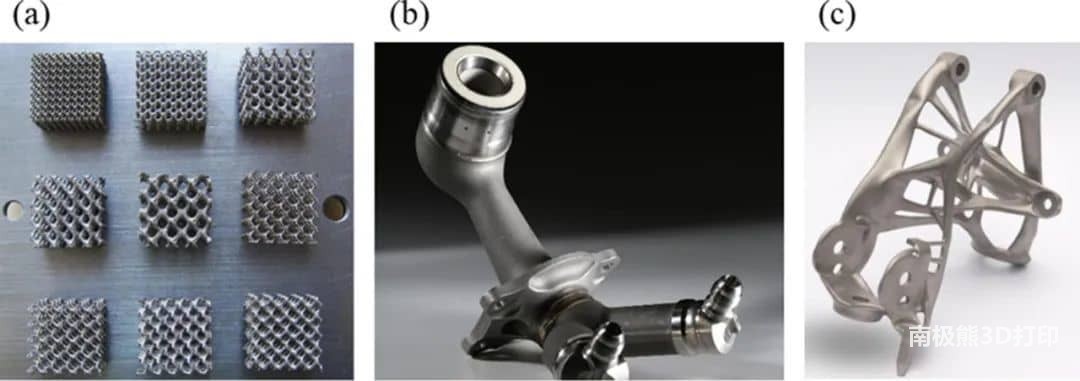
金屬零件的L-PBF近年來已基本發展。除了越來越多的商用機器外,還進行了大量研究以改進該技術。主要挑戰之一,特別是在疲勞是一個問題的應用中,是構建內部形成的缺陷。了解制造過程和缺陷形成是構建高質量零件的關鍵。
通常,缺陷可以通過三種特定方式產生或轉移到成品零件上,即通過:(1)從原料粉末轉移,(2)熔化過程中的激光 - 粉末 - 金屬相互作用,以及(3)后處理。總體而言,在LPBF中觀察到四種不同類型的缺陷,即:熔合孔隙率不足,鎖孔孔隙率,球化和氣體孔隙率。為了限制金屬增材制造過程中的缺陷產生,必須通過適當選擇加工參數來考慮和控制孔隙形成或轉移的所有三種機制。其中,激光-粉末-金屬相互作用是金屬AM加工過程中最常見的孔隙率轉移手段,其中通常可以觀察到諸如“鎖孔”和“無融合”(LOF)孔隙率等缺陷。
更詳細地說,熔池之間是否有足夠的重疊來確保所有點至少熔化一次,從而確定熔融孔隙度邊界的缺乏。LOF孔隙率最近也被證明是由于噴射的顆粒/飛濺物與激光和熔池的相互作用而形成的。在激光掃描過程中,大的飛濺物可能無法完全熔化,因此成為潛在的孔隙生成位點。相反,鎖孔孔隙度邊界對應于深鎖孔中的不穩定性,導致孔隙被擠壓。第三個邊界(稱為“串珠”邊界)由流體流動模式和熔池毛細管不穩定性的組合決定,并且是LPBF AM系統中保持精度(例如,同時增加速度和功率)的同時提高生產率的限制因素。全密度可以量化為具有>99.9%體積密度的樣品,但應該注意的是,仍然存在較大的缺陷。其目的是優化加工參數,減少LPBF AM材料中不需要的缺陷,并最終證明在由缺陷含量定義的工藝窗口中操作LPBF機器是可行的。
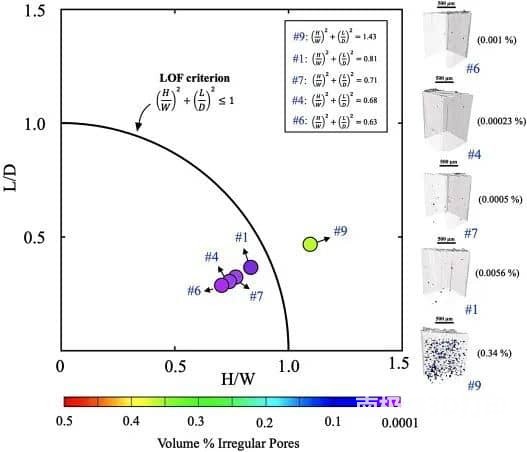
用于確定LOF孔隙率邊界的樣品根據LOF準則以及相應的缺陷密度繪制。
關于工藝參數對微觀結構、孔隙度水平和缺陷形成的影響的研究很多。有影響力的工藝參數包括(1)激光相關參數(例如,激光功率、光斑尺寸、脈沖持續時間和脈沖頻率),(2)掃描相關參數(例如,掃描速度或速度、掃描間距或出雛、掃描旋轉和掃描圖案),(3)粉末相關參數(例如,粉末形態、粒度和分布、層厚度、加樣和材料特性)和(4)宏觀參數(例如,粉末床溫度及其均勻性、氣體流量、氣體類型、吊具桿類型)。除了P-V-H-L處理組合外,掃描策略(圖3)在PBF工藝中的缺陷形成中起著至關重要的作用。掃描策略影響傳熱、粉末熔體形成和凝固速率,影響缺陷的類型、位置和分布以及晶粒形態。因此,優化工藝參數、熱源功率、掃描速度和策略以最大限度地減少工藝引起的孔隙率至關重要。
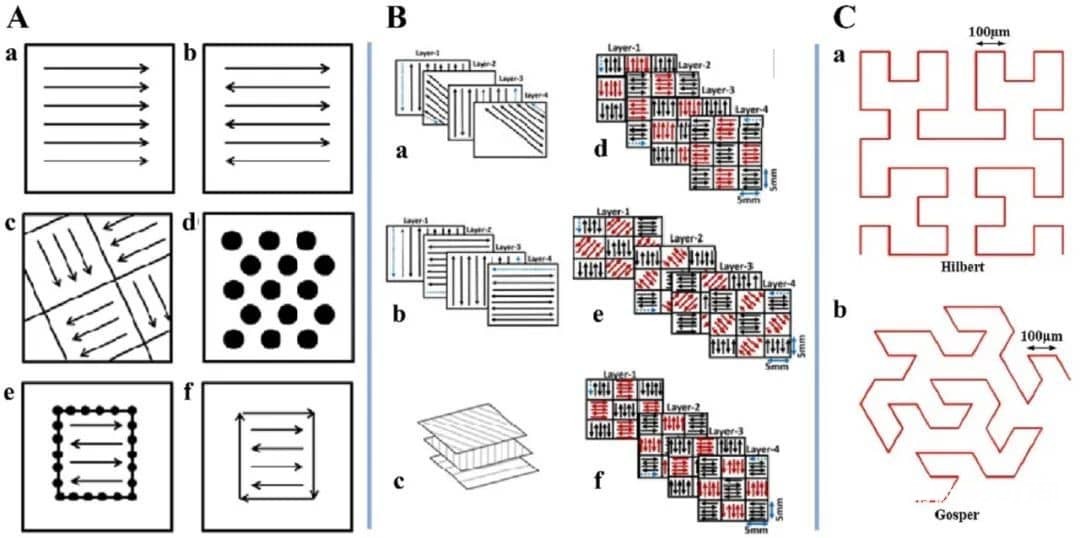
圖 3 (A)L-PBF過程中使用的不同掃描策略。(B)示出掃描模式的示意圖。(C)(a)Hilbert和(b)Gosper的分形掃描策略示例。
在激光粉末床熔融過程中以及隨后的粉末擴散過程中,由許多粉末特性控制,激光選擇性地掃描粉末層的表面,以按照相應層中的STL輸入文件熔化和熔化金屬粉末。復雜的激光物質相互作用導致許多現象,這些現象可能導致最終部件的缺陷。常見缺陷包括球化/珠狀、無熔合、鎖孔孔隙率、熔融金屬或粉末顆粒飛濺物噴出、周圍基材剝蝕或微觀結構缺陷。許多研究都集中在可視化和分析此類異常的實驗方法上。然而,在其形成中起主要作用的一個重要方面是激光與物質的相互作用。
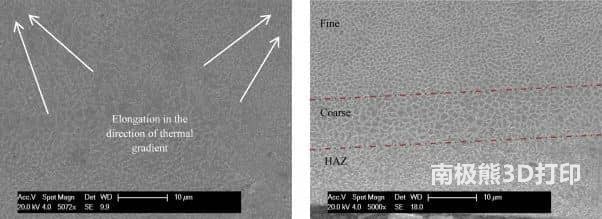
熔池的微觀結構顯示了晶粒取向和形態。
選擇性激光熔化可以從松散的粉末中制造出不僅具有與傳統制造的組件相似的物理形狀,而且還具有相似的性能。此外,SLM可以生產復雜的零件,如果用傳統技術制造,則需要一系列制造過程,消耗多余的材料(即浪費),時間和精力。在某些情況下,甚至可以使用SLM制造任何傳統制造方法都無法實現的零件。SLM的方法是選擇性地掃描粉末床,從而熔化粉末以逐層構建組件。在SLM中,組件構建在底板上,激光束穿過x-y平面中的每個層。在每層之后降低活塞,以允許后續粉末層沉積。該過程連續重復,直到部件完成。SLM過程消耗的時間可分為主時間和輔助時間。主要時間是熔化粉末層所需的時間,而輔助時間是基底降低和粉末沉積。
(責任編輯:admin)
最新內容
熱點內容