粉末床熔融金屬增材制造中的缺陷和異常(3)
時間:2023-01-06 11:03 來源:長三角G60激光聯盟 作者:admin 閱讀:次
導讀:本文旨在闡明粉末床熔融增材制造過程中常見的缺陷/異常及其形成機制。本文為第二部分。
1.4.缺陷分類
1.4.1.一般顯微結構缺陷和異常
一般來說,缺陷可以通過三種具體方式產生或轉移到成品零件上,主要是通過:(1)從原料粉末轉移到粉末相關缺陷,(2)熔化過程中的激光-粉末-金屬相互作用,也稱為加工相關缺陷,以及(3)由于熱處理導致的加工后相關缺陷(圖6)。此外,設備、建造準備和零件設計也會影響AM零件中缺陷的形成。金屬增材制造中常見的缺陷類型包括各種類型的氣孔,如未熔合、匙孔、球化和滯留氣體。其他缺陷類型包括表面粗糙度、殘余應力和金屬AM工藝快速凝固導致的變形(翹曲)。為了限制金屬AM內缺陷的產生,必須通過適當選擇材料、工藝和后處理設置來考慮和控制缺陷形成和轉移的機制。

圖6 粉末床熔合增材制造中的缺陷/異常形成機制分為三大類:(1)粉末相關缺陷,(2)加工相關缺陷,以及(3)加工后相關缺陷。
粉末相關缺陷。通常,粉末的形態、流動性、平均尺寸和粒度分布、表面污染等特性會影響最終產品的質量和性能。在基于熔融的AM工藝中,粉末特性直接受到粉末生產技術的影響,如水和氣體霧化、等離子霧化、等離子旋轉電極工藝等。使用球形粉末可以獲得更高的表觀密度、更高的堆積密度、更好的粉末流動性和光滑的表面光潔度,然而,球形粉末的生產成本較高。當PBF中使用的細粉(<5μm)比例過高時,可能會發生粉末結塊,從而對粉末堆積密度、粉末流動性和最終零件密度產生負面影響。L-PBF中使用的典型粒度范圍為15–45μm,而E-PBF中則使用45–110μm的粗粉粒。
處理相關缺陷。許多研究已經研究了加工參數,如功率、掃描速度、層厚、填充間距和掃描策略對不同缺陷形成的影響,主要是氣孔和孔洞。更詳細地說,熔合孔隙邊界的缺乏可以通過熔池之間是否有足夠的重疊來確定,以確保所有點至少熔化一次。相比之下,匙孔孔隙度邊界對應于深匙孔中的不穩定性,從而導致匙孔收縮。第三個邊界(稱為“串珠”邊界)由流體流動模式和熔池毛細不穩定性的組合決定,是提高生產速度的限制因素,同時保持L-PBF AM系統的精度(例如,同時提高速度和功率)。整體LOF、匙孔和堆焊氣孔邊界定義了一個有效的工藝窗口,用于生產名義上全密度的零件。全密度可量化為體積密度>99.9%的樣品,但應注意,在處理窗口內仍可能存在較大缺陷(圖7)。
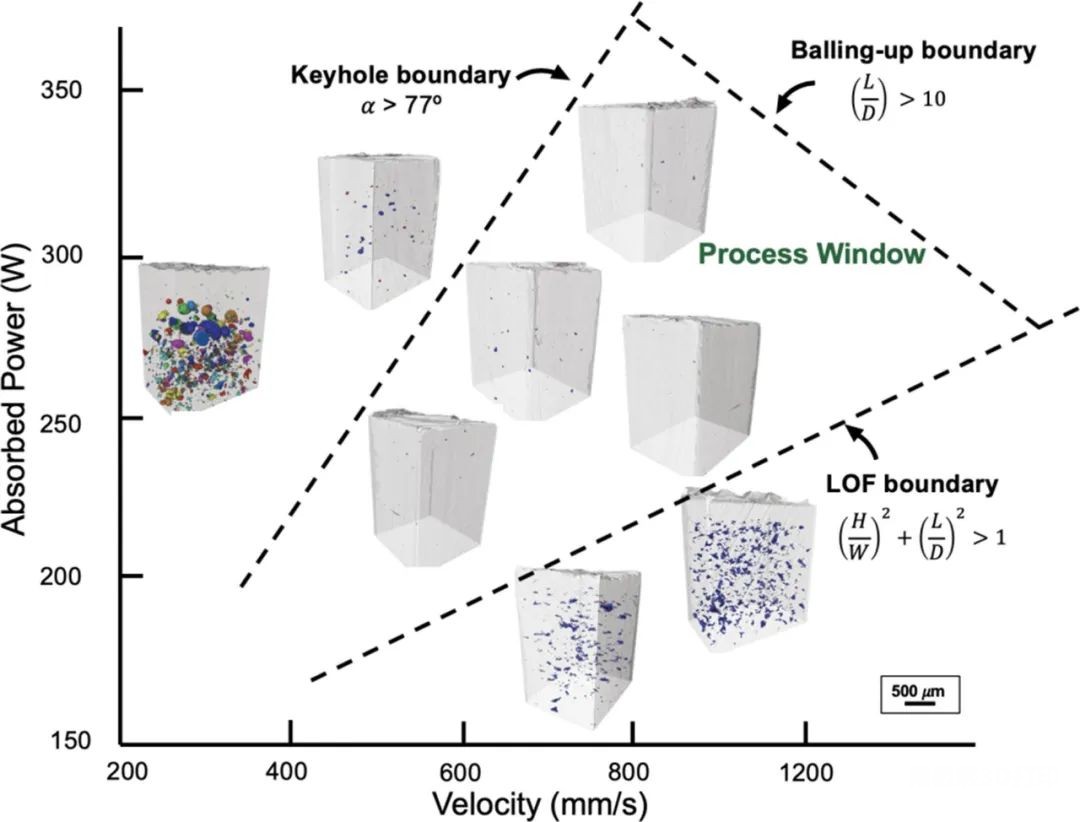
圖7 L-PBF金屬AM中的缺陷形態在功率速度(P-V)加工參數空間內遵循可預測的趨勢。
如下圖(a)和(b)所示,將3.2毫米厚的皮板真空夾在鋁基上,同時將擠壓的型材縱梁垂直放置并保持良好接觸到位。合金中鋰元素的存在增加了表面氧化膜的生長速度,這是焊接過程中孔隙率形成的主要原因。因此,在焊接前需要格外注意準備表面。用砂紙研磨表皮材料的表面以除去氧化層。已經發現AA2196上的氧化層含有較高的氫含量,因此將縱梁AA2196的表面研磨到至少0.2毫米。表面處理后縱梁的最終厚度為1.6 mm,采用直徑為0.8 mm的AA4047填充線。
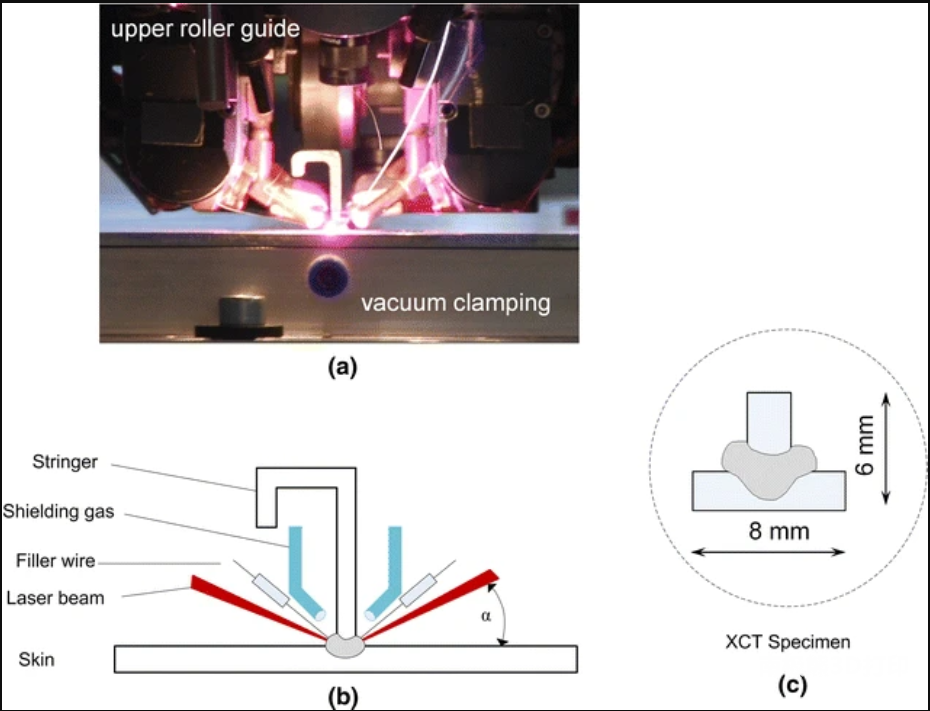
激光焊接蒙皮縱梁工藝和X射線CT樣品的配置。
其他缺陷,如開裂、變形和超高邊緣,在打印和打印圖案期間會受到熱歷史的影響,可以通過選擇適當的掃描策略和部件設計來控制這些缺陷。
(責任編輯:admin)
最新內容
熱點內容