粉末床熔融金屬增材制造中的缺陷和異常(2)
時間:2023-01-06 11:03 來源:長三角G60激光聯盟 作者:admin 閱讀:次
1.2.2. 電子束粉末床熔化
E-PBF使用電子束作為熱源,選擇性地燒結/熔化粉末。該工藝能夠制造出近乎完全致密的金屬零件,其機械性能可與傳統制造的零件相媲美,例如鑄件或成型件。因此,E-PBF部件可以在許多應用中用作承重結構。商業化的 E-PBF 系統的操作經過優化,可最大限度地減少缺陷,就像在 L-PBF 中一樣。然而,這些系統為過程修改提供了較少的自由度,并且缺乏對功率和掃描速度等的直接控制。
E-PBF系統有三個主要組件:電子輸送,粉末擴散系統和構建室。顧名思義,E-PBF和L-PBF之間的主要區別在于熱源。E-PBF工藝使用電子槍作為熱源,其位于粉末床的正上方(圖5)。電子是通過加熱燈絲產生的,燈絲可以是鎢絲或六硼化鑭LaB6陰極。然后,電子被施加的電壓加速,由一系列電磁透鏡聚焦和引導。與激光光學相比,E-PBF工藝中的電磁透鏡可以無慣性地移動電子束。結果,電子束的峰值掃描速度可以達到102m/s,明顯快于激光器的速度,激光器的速度被掃描光學元件限制在幾米/秒。
E-PBF工藝通常在預熱步驟后具有兩種熔化模式,如圖4所示。剖面線是填充體積區域的熔化模式,并使用光束沿著平行掃描路徑來回掃描,由預定義的剖面線間距距離分隔。之后,輪廓勾勒出每個橫截面的邊緣,并提高表面光潔度。可以更改的一些常見參數包括光束電流,焦點偏移(控制光斑大小)圖案填充間距距離等。
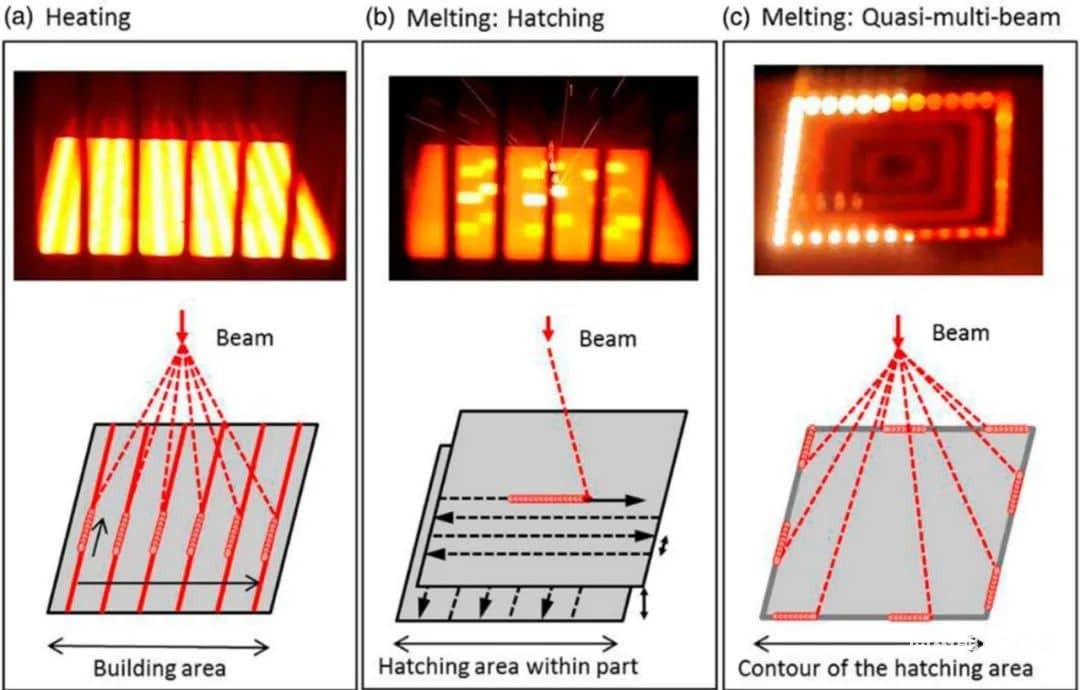
圖 4 E-PBF工藝中三種熔融模式的實際圖像和示意圖。
E-PBF機器中的另一個關鍵模塊是粉末擴散系統,其基本目標是在熔化步驟之前將粉末從儲液罐輸送到構建板上均勻的層上。在Arcam E-PBF系統中,兩個料斗和一個耙子被協調以完成上述任務。標準 E-PBF 粒徑范圍為 45–106 μm,比 L-PBF 中使用的原料更粗糙。較粗的粉末減少了吸煙,因為顆粒質量更大,這意味著需要更多的動能來噴射任何給定的顆粒。此外,由于在E-PBF工藝中,工藝分辨率(即熔池尺寸)通常較粗糙,因此不需要使用更細的粉末。當然,使用較粗的粉末更具成本效益,因為標準霧化技術產生的粒徑范圍比AM中使用的顆粒范圍更廣。
由于球形、特定粒徑范圍和化學純度的要求,目前市場上用于SLM和EBM工藝的Ti粉末主要通過氣體霧化(GA)或等離子體旋轉電極工藝(PREP)生產,兩者的運營成本都很高。此外,一些增材制造設備供應商為其特定機器提供自己的專有粉末套件。因此,對于大多數AM操作和應用,粉末和成品零件的成本很高。對于Ti AM的更廣泛應用,需要適用于AM的具有成本效益的球形Ti粉末。
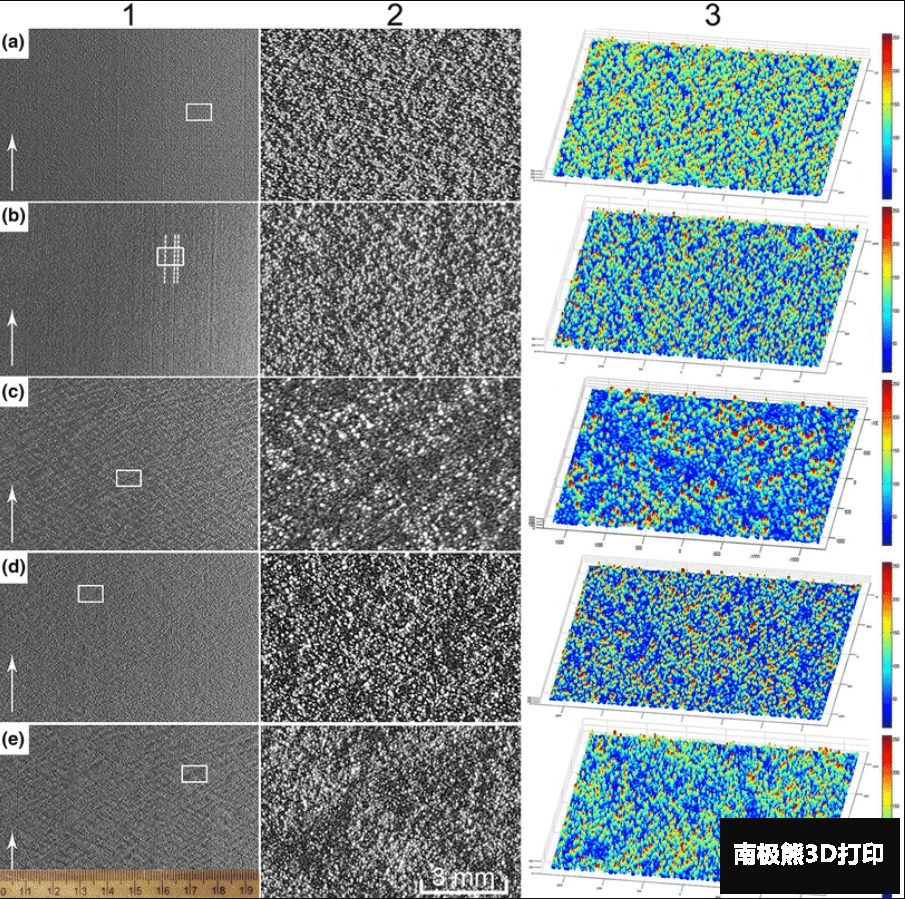
UPB系統中收集的不同粉末的宏觀表面輪廓:Arcam Ti-6Al-4V(a)原始粉末和(b)用過的粉末,經PMT處理的新型Ti粉末(c)45–106μm,(d)75–106|μm和(e)45–75μm。
同樣,懸垂需要支撐結構,就像在L-PBF過程中一樣,但用途不同。與后一種工藝不同,E-PBF中使用的高預熱可能儲存的殘余應力很少。然而,總是有可能在未熔化的粉末包圍的懸垂物中積聚熱量,這些粉末具有較低的導熱性。局部過熱會導致熔池尺寸過大,并與預期的構建條件(和尺寸)發生偏差。E-PBF中的支撐結構用于為從懸垂物中提取熱量提供固體通道。
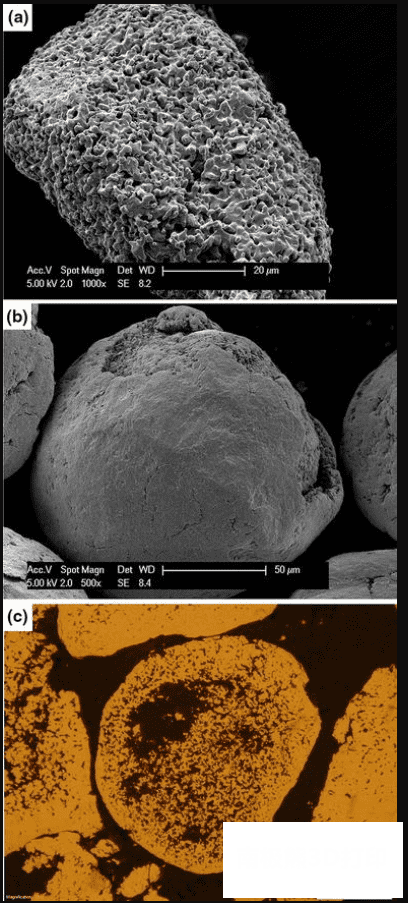
顯示新型Ti粉末表面特征的掃描電鏡圖像(a)在PMT處理30分鐘之前和(b)之后和(c)以及(c)PMT處理的粉末顆粒橫截面的光學顯微照片
1.3. 熔化模式
基于粉末的增材制造(AM)利用移動的能量源(例如,電子束或激光)以逐層方式選擇性地熔化金屬粉末,以構建所需的3D(3D)結構。下圖顯示了從有限元模型獲得的溫度等值線和熔池邊界。FE計算的熱結果可以進一步計算熔池尺寸,凝固速率和溫度梯度,從而可以預測凝固微觀結構。
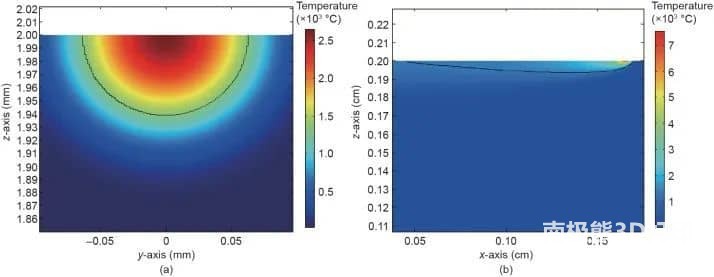
(a)有限元模型溫度輪廓(°C)和熔池邊界(黑線表示)的橫截面圖(y–z);(b)有限元模型溫度輪廓(°C)和熔池邊界(黑線表示)的縱向視圖(x–z)。模擬激光功率為200 W,掃描速度為960 mm·s−1,吸收率為0.5。
在一些研究中已經報道了測量溫度和模擬之間的直接比較。Peyre等人構建了一個由20層組成的薄壁,其中三個熱電偶放置在基板上。通過溫度測量驗證了熱預測,顯示了熱量積聚(來自連續層)對熔池尺寸的影響。Denlinger等人使用數值模型來估計包含38層的塊狀幾何形狀的熱歷史,以便與Inconel 718粉末床融合期間的原位溫度測量進行比較。預測的溫度與測量結果吻合良好。
圖5顯示了假設的高斯激光束在傳導和鎖孔模式下的激光能量吸收之間的比較。除純傳導模式外,激光與液態金屬相互作用,粉末熔化成熔池前部的液體。此外,散焦(在L-PBF中)或焦點偏移(在E-PBF中)會影響打印模式和孔隙形成,即散射激光會降低功率密度,這有助于避免不穩定的鎖孔和孔隙形成。
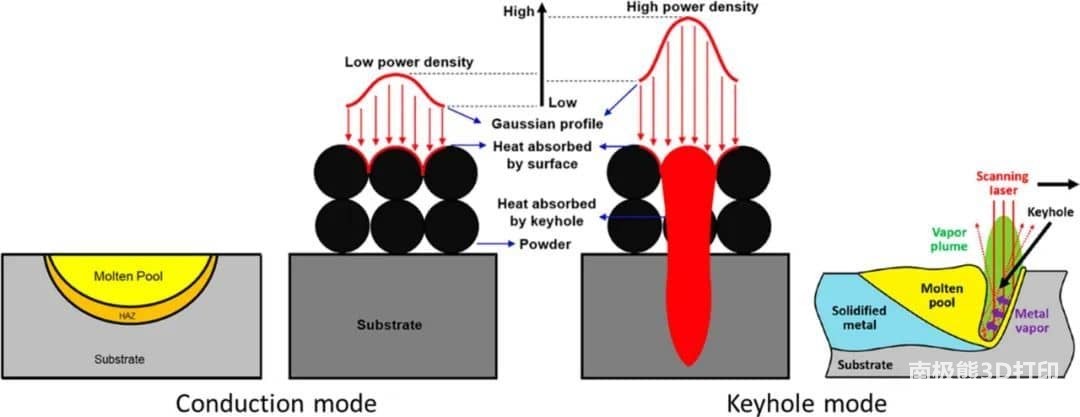
圖5 初始時刻激光在傳導模式和鎖孔模式下的能量吸收示意圖。假定激光具有高斯分布。在傳導模式下,激光能量被上表面吸收,而在鎖孔模式下,激光能量主要被吸收在蒸汽腔的內表面。
1.3.1.傳導模式
傳導模式通常與熔池有關,其中汽腔及其相關影響可忽略不計。傳導模式通常會產生半圓形熔池或長寬比較小的熔池,如圖5所示。基板中的能量密度足夠低,以至于基板溫度不會升高到沸點以上,因此不會形成汽腔。Bag等人采用了僅傳導傳熱模式的假設,他們使用自適應體積源成功地對點焊進行了建模。在他們的研究中,熔池都顯示出與導電模式焊接相關的特征,近似半圓形。在另一種方法中,Russo等人將傳導模式焊接描述為熔池運動或擴展(去聚焦)熱源不會干擾熱分布。
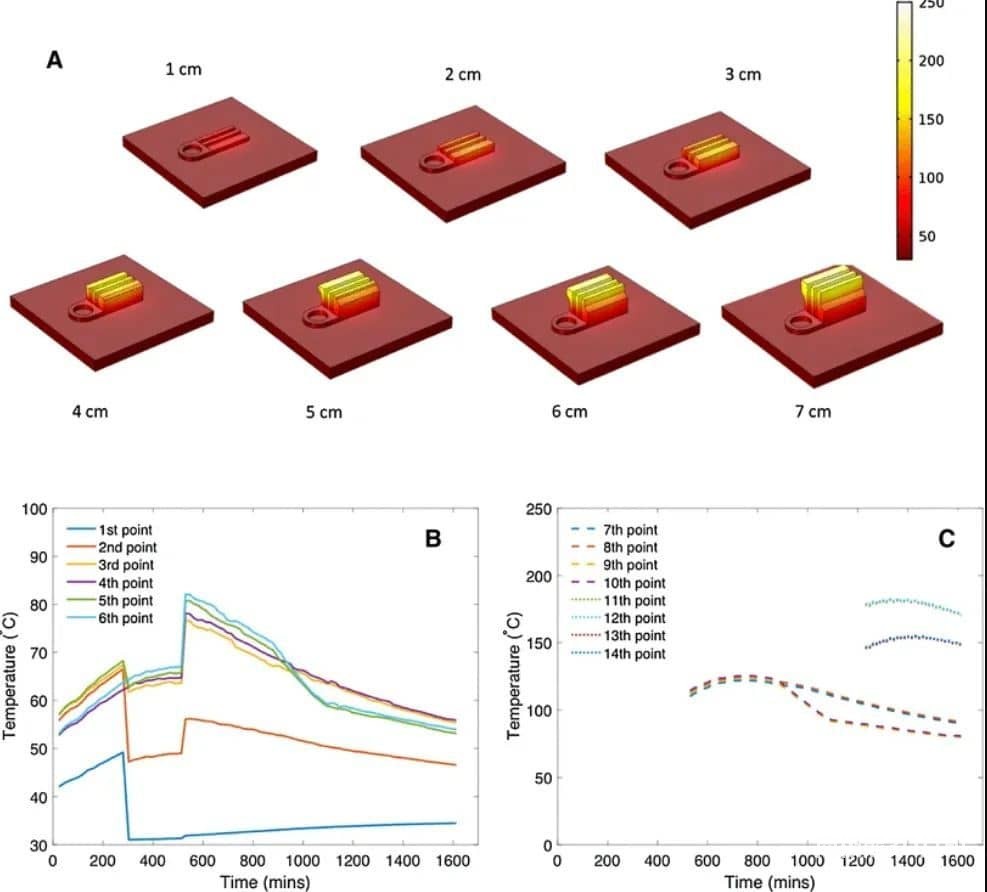
a顯示從數值模型獲得的熱演化的三維溫度等值線圖;感興趣點的b和c溫度。溫度顯示在下一粉末層沉積之前。
上圖a顯示了當上表面溫度相對均勻時,下一粉末層沉積前的層溫度。圖a還表明,由于建造過程中的熱量積累,建造的高層具有局部較高的基礎溫度。預計室溫的最大溫升約為250°C。圖b、c顯示了所有14個點的預測溫度歷史(在層沉積結束時)。該圖說明了整體能量輸入、幾何特征和制造時間對整體溫度升高的影響。例如,圖b顯示了幾何圖形左側的薄區域建造完成后,在點1和點2上方沒有進一步的直接熱量輸入的情況下,約300分鐘左右的層溫度突然下降。由于掃描面積較小,一層的掃描時間從70秒減少到50秒,導致約500分鐘的層溫度突然升高。
1.3.2. 鎖孔模式
當激光功率強度增加到約1 MW/cm2以上時,就實現了鎖孔模式。激光沖擊材料表面會提高溫度,導致熔化。隨著溫度進一步升高并達到沸點,金屬蒸汽的形成會產生反沖壓力。反沖壓力將熔融金屬向下推,形成一個細長的氣體腔,稱為鎖孔。激光進入鎖孔后,在被吸收(或部分反射出去)之前,會經歷來自前后鎖孔壁的多次反射。如圖5所示,與傳導模式相比,在PBF過程中,已經凝固的零件將經歷更多的再熔化和冷卻熱循環。
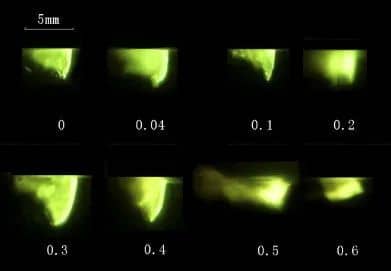
鑰匙孔形狀各異的照片。鋁膜厚度為0至0.6 mm。激光功率:1000 W,焊接速度:1 m min−1,離焦:0mm,保護氣體流量:2m3h−1。
上圖顯示了鋁膜厚度范圍為0至0.6 mm的鎖孔形狀的清晰照片。關于相機的曝光時間設置為1/1000 s,激光束和鎖孔都可以在如此短的時間內被視為靜止。實驗結果表明,氣液界面清晰可辨,鎖孔彎曲方向與焊接速度相反。鎖孔彎曲的原因是由于激光束與工件之間的相對運動,在實際的深刺激光焊接中。鎖孔的形狀由鎖孔等離子體的密度控制。當兩塊玻璃之間沒有夾住鋁膜時,鑰匙孔的形狀狹窄而深,具有可變橫截面的細長毛細管。隨著鋁膜厚度的增加,這意味著鎖孔等離子體的密度更高,孔徑增加以及更深的鎖孔形成。當薄膜的厚度增加到0.3毫米的中間厚度時,鑰匙孔達到5.3毫米的最大深度。繼續加厚鋁膜,孔徑繼續擴大;然而,鎖孔的深度急劇減少。這種現象表明,鎖孔等離子體的過量密度阻礙了入射激光束向內部材料的傳輸。多余的鎖孔等離子體會阻擋激光束,反射并重新聚焦激光束,導致鎖孔塌陷。
(責任編輯:admin)
最新內容
熱點內容